To help slow a changing global climate by at least eliminating the emissions that come directly from conventional vehicles that are powered by burning fossil fuels, automotive OEMs have started producing more vehicles that are powered by rechargeable electric batteries. In addition, some automakers only make electric vehicles.
Most new vehicle sales are still for ones with an internal combustion engine, but globally about 16% were for EVs in 2023, according to Puneet Sinha, senior director of the battery industry at Siemens Digital Industries Software, which is headquartered in Plano, Texas. That percentage is a far cry from the miniscule number on the roads about 15 years ago when a small wave of EVs hit the market.
“They were either very expensive or offered a very limited electric drive range,” Sinha said.
Battery manufacturers have made strides to lower the cost and increase the range while reducing the recharging time, but the quest for improving battery range and recharging time and lowering the cost continues. Earlier battery chemistries, such as lead-acid and nickel-cadmium, have been replaced primarily by lithium-ion cells. The batteries store and release renewable power by moving lithium ions through a liquid, the electrolyte, from the cathode to the anode and back again. They are known for their high power-to-weight ratio, energy efficiency and temperature resistance, as well as their low self-discharging capabilities, but a host of new battery technologies are under development or waiting in the wings. These include solid-state, lithium-air, lithium-sulfur and graphene batteries, as well as hydrogen fuel cells.
In addition, as lithium-ion batteries continue to evolve, battery companies are developing batteries with a solid-state electrolyte instead of a liquid one to enable lithium-ion batteries to operate safer and more robustly, Sinha said. “The liquid electrolyte is combustible, has certain limitations, more toward safety, but also toward the durability of those lithium-ion batteries.”
Solid-state batteries are being developed for both consumer electronic and EV applications, and tremendous advancements have been achieved during the past five years, Sinha said. “In the next five years, it is possible that we’ll see commercialization of solid-state batteries in some of the applications.”
Keeping Dangers in Check
Initially, lithium batteries were made with pure lithium metals, but manufacturers could not control the growth of dendrites, which are like stalactites and stalagmites but in a lithium battery, explained Brad Larschan, CEO of Avadain, which has a globally patented technology to manufacture high-quality graphene flakes. When lithium is charged and discharged, some of the lithium crystallizes and forms dendrites that grow from a battery’s anode and cathode and can pierce the separator layer. The consequence ranges from a short circuit to a fire or explosion.
“That’s why the lithium-ion battery was developed,” Larschan said. “It was such a breakthrough and led to widespread consumer use of lithium batteries.” The tradeoff, however, is that lithium-ion has only about 10 percent of the energy efficiency of pure lithium metal.
As adoption of EVs continues to increase, albeit in fits and starts, Sinha said battery production is forecast to grow tenfold by the end of the decade. That rate of growth is both a tremendous opportunity and challenge for companies in the entire supply chain, which includes companies that mine and process lithium, chemistry producers, cell suppliers, system integrators such as automakers and builders of the sophisticated machines that are needed for large-scale battery production.
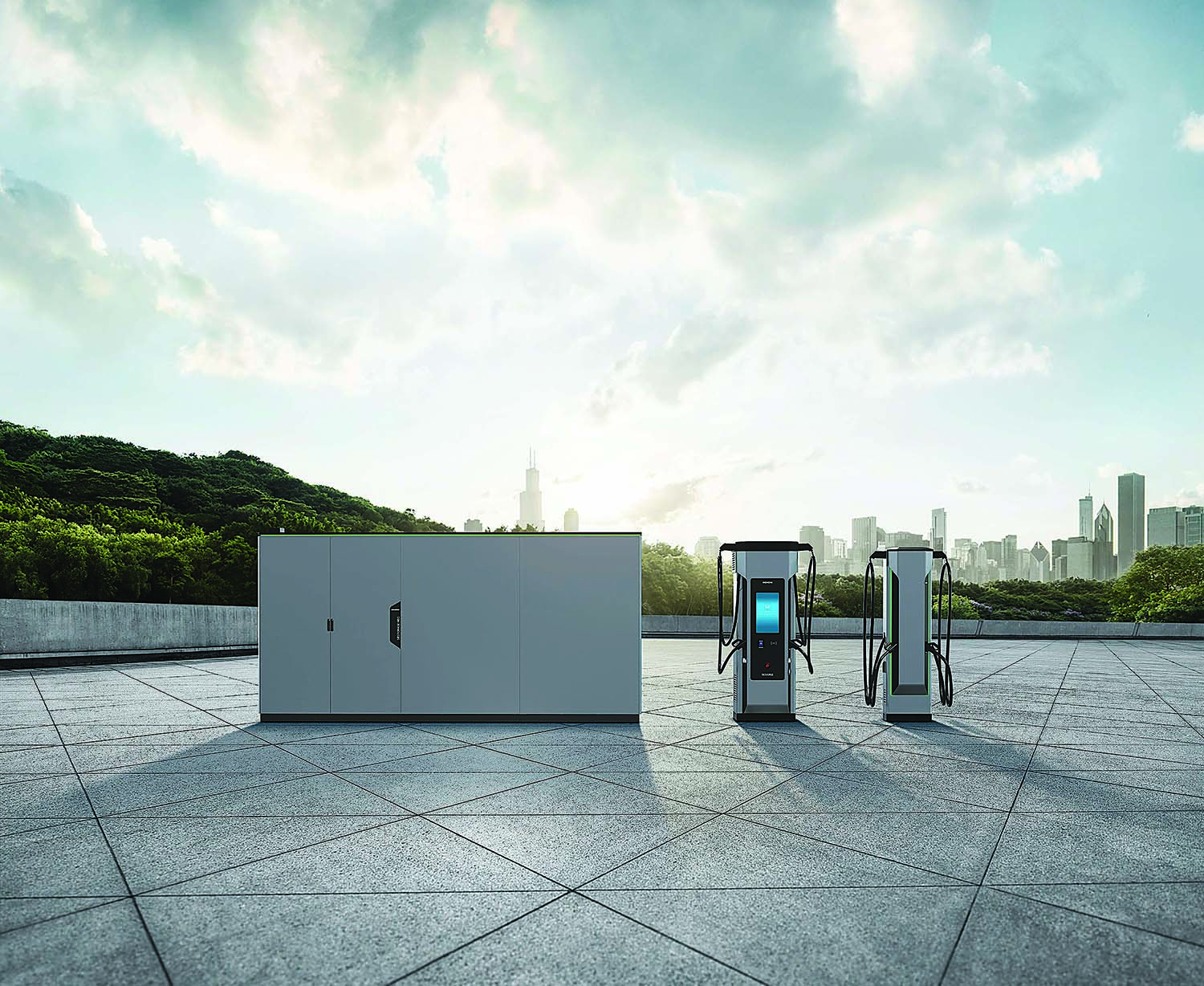
According to Sinha, manufacturing represents about 25 percent of the cost of a lithium-ion cell, partly because of a high level of scrap. He estimates that the scrap rate can reach 40 percent or more when production begins at a battery gigafactory. “Even for companies who have stable production at capacity, they struggle with a 10% or 15% scrap rate.”
One area of significant investment for battery manufacturers focuses on improving energy density, the amount of juice that can be packed into 1 kg (2.2 lbs.) of battery, Sinha said. Doing so allows an EV to go further before needing a recharge.
Because about 70% to 80% of the battery pack’s weight is in its cells, battery manufacturers are continually researching chemistries to increase the energy density in a lithium-ion cell to create lighter batteries with the same energy density, he noted.
The remaining weight is comprised of structural beams, pumps, coolant and other items in a battery pack, Sinha added. The objective is to reduce the weight of those without sacrificing the rigidity or structural integrity of the battery pack.
He noted that the key minerals that are needed to make lithium-ion batteries are nickel, cobalt and manganese, but manufacturers are looking to reduce the amount of cobalt needed because of its high cost.
One type of lithium-ion battery that is seeing an increased demand is the iron phosphate lithium battery, Sinha said, because they cost less but also have a lower energy density than conventional lithium-ion ones and, therefore, provide less range. However, they are heavier than lithium-ion batteries that have nickel, cobalt and manganese.
When manufacturing a lithium-ion EV battery, which will be increasingly performed in gigascale factories to achieve economies of scale, Sinha said it is less like building a vehicle and more like baking a cake. After mixing the proper ingredients and ensuring everything has the right properties, the cake is baked in an oven to complete the process. “It’s the same thing you need to do for a lithium-ion cell at the end of manufacturing.”
Flakes for the Future
While lithium-ion EV batteries are well-established, graphene ones are still on the drawing board. However, graphene batteries would “revolutionize” the electric vehicle industry, according to Avadain’s Larschan. “A graphene battery could almost instantly increase by three or four times the distance between charging.”
Graphene is 10 or fewer, preferably five, atomic atoms of carbon atoms arranged in a hexagonal lattice nanostructure and is 200 times stronger than steel. But not all graphene is equal.
“Think of graphene and graphene materials as a continuum, starting with graphite on the low end and large, thin and nearly defect-free graphene flakes on the high end,” Larschan said. “Graphite is nothing more than millions of layers of graphene bonded together by what are called van der Waals forces. Graphite is very plentiful, and we can separate the graphite into a high-value, great-utility material called graphene.”
He added that the larger the lateral flake size is the higher the electrical conductivity, with a size in the tens of microns being ideal. “What makes graphene such a great electrical conductor is that each graphene atom has one free electron, and it’s that electron that allows pure graphene to conduct electricity at nearly the speed of light.”
Graphene, Larschan noted, has several potential uses in an EV battery, with replacement of spherical graphite as the anode being “the easy one.” Graphite is not a particularly good conductor of electricity but is used as an anode because it can withstand high temperatures, providing a tradeoff between heat resistance and electrical conductivity. Graphene, on the other hand, has the same melting point as graphite and is “nearly a perfect electrical conductor.”
A spherical graphite anode is also relatively heavy. It represents just under 50 percent of the material in typical lithium-ion batteries and accounts for 28% of an EV battery’s weight, Larschan said, while graphene is one of the lightest materials. About three atomic layers of large, thin and nearly defect-free graphene flakes can replace the spherical graphite anode, virtually eliminating the weight of the anode. “The advantage is you can charge your battery in minutes instead of hours using graphene instead of spherical graphite.”
That replacement is the “low hanging fruit” for graphene in an EV battery, he said, and could happen in a year or so if a company commits to it. Graphene, however, is being used as an additive to enhance materials, including as an adjunct to lithium. “But I am unaware of any purely graphene battery.”
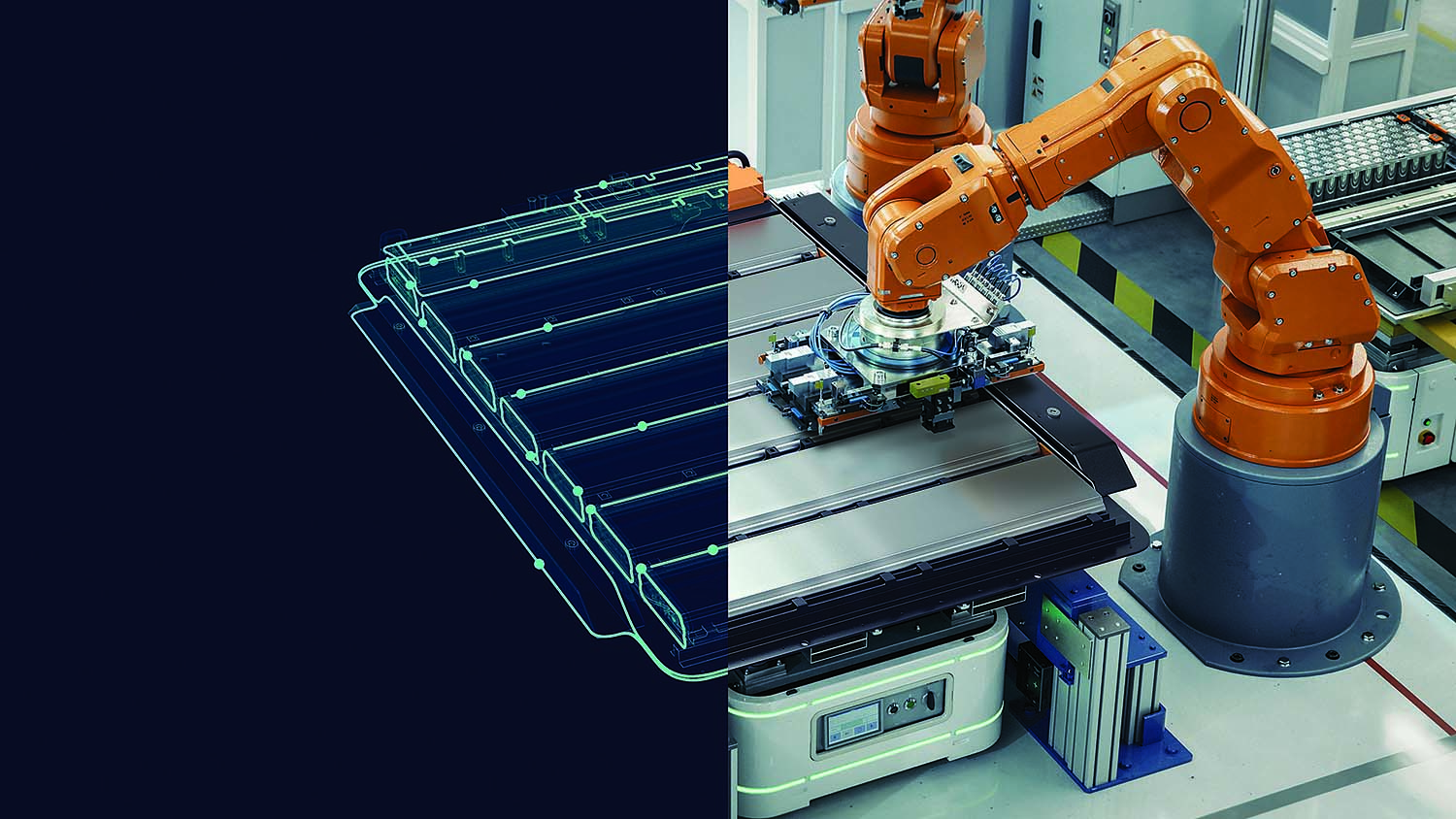
With the proper commitment from a battery manufacturer or automotive company, he added that purely graphene batteries could be available by the end of the decade. Because a sizeable number of consumers are reluctant to purchase a vehicle that requires frequent charging for long intervals and still might run out of energy before arriving at their destination, EV sales are more challenging to those who are not early adopters and already took the plunge. “Having graphene batteries would absolutely move the needle for consumer adoption of electric vehicles.”
In addition, graphene will not produce any measurable heat, is extremely stable and does not produce any toxic off-gases, Larschan said. “It doesn’t have any safety concerns. That’s one of the beautiful things about graphene is that it’s just purely carbon. Graphene will free us from the shackles and dangers of lithium, which is a scarce material anyway, to a more efficient and safe material.”
Other Offerings
As noted previously, a number of other lithium- and non-lithium-containing batteries are also in the hunt for market acceptance and, ultimately, market dominance.
Hydrogen fuel cells, for example, show great promise in powering EVs, as well as supplying a clean stationary energy source across a wide spectrum of industries, reported Persistence Market Research in Pune, India. Fuel cells produce electricity with minimal or zero emissions, particularly when using hydrogen as a fuel. They are also highly efficient in converting fuel into electricity, with some achieving efficiency rates of over 60% to significantly reduce fuel consumption and energy waste.
According to the research organization, hydrogen fuel cells face numerous restraints and challenges that can impact growth and widespread adoption. These include high initial costs, limited fuel availability in certain regions, concerns about safe and efficient storage, and limitations in applications where space and weight constraints are critical.
In addition, the lack of a well-developed and widespread hydrogen infrastructure is a significant restraint. Without adequate hydrogen production, transportation and refueling facilities, the full potential of the technology cannot be realized. Fuel cells also face competition from advanced battery technologies, which have made strides in terms of energy density, cost reduction and charging infrastructure. Batteries are often seen as a more established and familiar technology.
Lithium-air batteries are a promising technology for EVs and other applications where high energy density is important, reported New York-based Reed Intelligence. The battery uses oxygen from the air to store energy and offers a much higher theoretical energy density than lithium-ion batteries. Because of their high energy density and ability to withstand abuse, lithium-air batteries are well-suited for heavy-duty applications, such as buses and trucks.
However, lithium-air batteries are still in development, and there are some safety concerns, the consulting firm stated. For example, the batteries can be flammable if they are not properly designed and manufactured.
Another type that has the chemical element with atomic number 3 is the lithium-sulfur battery. Sulfur is abundant, cost-effective and can hold more energy than traditional ion-based batteries, the U.S. Department of Energy’s Argonne National Laboratory reported. Previously, lithium-sulfur batteries did not perform well because polysulfides dissolved into the electrolyte, which causes corrosion that lowers the number of times a battery can be recharged.
Researchers at the laboratory developed and tested a porous sulfur-containing interlayer, and the cells with the active interlayer maintained a high capacity of over 700 charge-discharge cycles. “Previous experiments with cells having the redox-inactive layer only suppressed the shuttling, but in doing so, sacrificed the energy for a given cell weight because the layer added extra weight,” said Guiliang Xu, an Argonne chemist. “By contrast, our redox-active layer adds to energy storage capacity and suppresses the shuttle effect.”
Regardless of which energy source — or sources — comes out on top, electric vehicles are poised to gain a larger share of new vehicle sales moving forward. That development will benefit some businesses and disrupt others, such as manufacturers of engine components that are not needed in a vehicle with a motor and inverter instead. “Those are new opportunities and new challenges for Tier 1 players,” Sinha said, “and many of them are evolving and growing in those areas.”
Contact Details
Related Glossary Terms
- baking
baking
1. Heating to a low temperature to remove gases. 2. Curing or hardening surface coatings, such as paints, by exposure to heat. 3. Heating to drive off moisture, as in the baking of sand cores after molding. Often used after plating or welding, or when the presence of hydrogen is suspected, to prevent embrittlement.
- burning
burning
Rotary tool that removes hard or soft materials similar to a rotary file. A bur’s teeth, or flutes, have a negative rake.
- coolant
coolant
Fluid that reduces temperature buildup at the tool/workpiece interface during machining. Normally takes the form of a liquid such as soluble or chemical mixtures (semisynthetic, synthetic) but can be pressurized air or other gas. Because of water’s ability to absorb great quantities of heat, it is widely used as a coolant and vehicle for various cutting compounds, with the water-to-compound ratio varying with the machining task. See cutting fluid; semisynthetic cutting fluid; soluble-oil cutting fluid; synthetic cutting fluid.
Contributors
Avadain
901-335-8571
www.avadaingraphene.com
Siemens Digital Industries Software
800-498-5351
www.sw.siemens.com