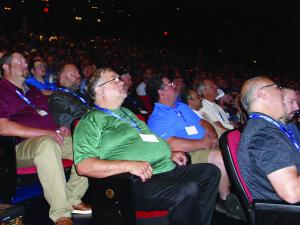
“Time is money” is an age-old adage that certainly rings true when it comes to machining metal.
At Iscar’s 2024-25 product launch July 15 at the Encore at Wynn Las Vegas resort, Jacob Harpaz, chairman and president of the Tefen, Israel-headquartered International Metalworking Co., which includes Iscar as a member, emphasized how the toolmaker’s quick-change inserts require no setup time or tool offsets, and that its cutters are designed for fast metal removal with the objective to improve productivity by at least 15%. “There’s no time for downtime. No setup time is the name of the game because time is money.”
The day-long series of presentations from Iscar USA, Arlington, Texas, featured the theme “You Machining Intelligently?” The event covered tools for turning, grooving and parting, as well as drilling and milling.
Jacob Harpaz, chairman and president of IMC, at the press event after the product launch presentations. All images courtesy A.Richter.,
Prior to the product presentations, Harpaz said in his opening address that the metalworking sector is seeing modest growth because of a moderate slowdown in the automotive and energy industries, including oil and gas, along with the ongoing geopolitical situation.
With a global shortage for mechanical engineers and CNC machinists, part manufacturers demand cutting tools that boost productivity to stay competitive, he said. Harpaz added that Iscar tools can double tool life, depending on the application, but it’s critical to convert higher tool life into higher productivity. Cutting tool purchases in half will not have much impact on profitability because tooling only represents 3% to 4% of a manufacturer’s total production costs, compared with 28% for labor, 26% for machinery, 22% for materials and 21% for factory and administration expenses. Instead of reducing production costs by 1.5% when doubling tool life, a 15% reduction is possible through fast metal removal.
According to Harpaz, these productivity gains can even be realized on older machines, and improved tool grades help overcome previous cutter limitations.
Throughout the presentations, he often stressed the importance of pinpointing coolant directly at the cutting zone and applying it at high pressures to help form, break and manage chips. Methods to enhance coolant flow through channels in tool bodies include 3D printing the channels and using computational fluid dynamics to optimize a smooth fluid flow.
Iscar’s product launch included tools for drilling intelligently.
As the price of tungsten carbide rises, Harpaz said Iscar continues to introduce more double-sided inserts for economic savings by doubling the number of cutting edges per insert. In addition, the toolmaker cut the use of carbide powder where it is not needed to further reduce costs.
In the turning presentation, he said the company offers grades for heat-resistant superalloys, hardened steel and chilled cast iron, nonferrous metals, cast iron, stainless steel and steel (ISO S, H, N, K, M and P material groups). CVD and PVD coated grades are available for the latter three groups with a color coding based on each coating’s appearance: gold for TiN, gray for TiC and purple for TiCN.
The following highlights some of the new products Harpaz covered.
For internal turning and chamfering, Iscar introduced the Picco-3-Cut multiple-cornered Picco-Cut inserts with three cutting edges for miniature applications. Coolant flows through three side channels directed to the cutting edges, and each edge can be the same or different.
The Quick-I-Groove is a uniquely shaped double-sided insert with four cutting edges for internal grooving and turning, as well as threading. The insert can be mounted on right- and left-hand tools, and internal coolant is pinpointed directly to the cutting edge. Its rigid clamping system provides high repeatability and accuracy, according to Iscar.
The lobby of the Encore Theater featured displays that focused on machining intelligently with LogiQuick.
The SumoChan ChamDrill line with a Multi-Master connection is for drilling stationary and rotating workpieces. The tool provides an easy and quick insert change, saving setup and machine downtime. In a comparison video demonstration against other insert changing systems, Harpaz noted that changing the Iscar insert consumed 19 seconds versus 51 to 210 seconds for the competition.
In his conversation with members of the press, Harpaz said drilling is Iscar’s No. 1 priority, along with remaining the market leader in parting.
For milling, where Harpaz said the trend is for cutting at a high feed rate with a shallow DOC, Iscar introduced the Mill-4-Feed cutter that accepts small 06 high-feed square inserts with four positive cutting edges. The tool is suitable for machining diverse material types with a hardness up to 65 HRC.
To grow its business, Harpaz said Iscar will continue its R&D drive, noting that the company employs more than 250 R&D specialists in its head office. In addition, IMC Group continues its growth through acquisitions. Recent ones include BSW Zerspanungswerzeuge GmbH, a manufacturer of PCBN, PCD and CVD diamond inserts in Saarwellingen, Germany, and Bisingen, Germany-based Neoboss GmbH, a tap manufacturer.
Related Glossary Terms
- chamfering
chamfering
Machining a bevel on a workpiece or tool; improves a tool’s entrance into the cut.
- chemical vapor deposition ( CVD)
chemical vapor deposition ( CVD)
High-temperature (1,000° C or higher), atmosphere-controlled process in which a chemical reaction is induced for the purpose of depositing a coating 2µm to 12µm thick on a tool’s surface. See coated tools; PVD, physical vapor deposition.
- computer numerical control ( CNC)
computer numerical control ( CNC)
Microprocessor-based controller dedicated to a machine tool that permits the creation or modification of parts. Programmed numerical control activates the machine’s servos and spindle drives and controls the various machining operations. See DNC, direct numerical control; NC, numerical control.
- coolant
coolant
Fluid that reduces temperature buildup at the tool/workpiece interface during machining. Normally takes the form of a liquid such as soluble or chemical mixtures (semisynthetic, synthetic) but can be pressurized air or other gas. Because of water’s ability to absorb great quantities of heat, it is widely used as a coolant and vehicle for various cutting compounds, with the water-to-compound ratio varying with the machining task. See cutting fluid; semisynthetic cutting fluid; soluble-oil cutting fluid; synthetic cutting fluid.
- feed
feed
Rate of change of position of the tool as a whole, relative to the workpiece while cutting.
- gang cutting ( milling)
gang cutting ( milling)
Machining with several cutters mounted on a single arbor, generally for simultaneous cutting.
- grooving
grooving
Machining grooves and shallow channels. Example: grooving ball-bearing raceways. Typically performed by tools that are capable of light cuts at high feed rates. Imparts high-quality finish.
- hardness
hardness
Hardness is a measure of the resistance of a material to surface indentation or abrasion. There is no absolute scale for hardness. In order to express hardness quantitatively, each type of test has its own scale, which defines hardness. Indentation hardness obtained through static methods is measured by Brinell, Rockwell, Vickers and Knoop tests. Hardness without indentation is measured by a dynamic method, known as the Scleroscope test.
- lapping compound( powder)
lapping compound( powder)
Light, abrasive material used for finishing a surface.
- metalworking
metalworking
Any manufacturing process in which metal is processed or machined such that the workpiece is given a new shape. Broadly defined, the term includes processes such as design and layout, heat-treating, material handling and inspection.
- milling
milling
Machining operation in which metal or other material is removed by applying power to a rotating cutter. In vertical milling, the cutting tool is mounted vertically on the spindle. In horizontal milling, the cutting tool is mounted horizontally, either directly on the spindle or on an arbor. Horizontal milling is further broken down into conventional milling, where the cutter rotates opposite the direction of feed, or “up” into the workpiece; and climb milling, where the cutter rotates in the direction of feed, or “down” into the workpiece. Milling operations include plane or surface milling, endmilling, facemilling, angle milling, form milling and profiling.
- parting
parting
When used in lathe or screw-machine operations, this process separates a completed part from chuck-held or collet-fed stock by means of a very narrow, flat-end cutting, or parting, tool.
- physical vapor deposition ( PVD)
physical vapor deposition ( PVD)
Tool-coating process performed at low temperature (500° C), compared to chemical vapor deposition (1,000° C). Employs electric field to generate necessary heat for depositing coating on a tool’s surface. See CVD, chemical vapor deposition.
- polycrystalline cubic boron nitride ( PCBN)
polycrystalline cubic boron nitride ( PCBN)
Cutting tool material consisting of polycrystalline cubic boron nitride with a metallic or ceramic binder. PCBN is available either as a tip brazed to a carbide insert carrier or as a solid insert. Primarily used for cutting hardened ferrous alloys.
- polycrystalline diamond ( PCD)
polycrystalline diamond ( PCD)
Cutting tool material consisting of natural or synthetic diamond crystals bonded together under high pressure at elevated temperatures. PCD is available as a tip brazed to a carbide insert carrier. Used for machining nonferrous alloys and nonmetallic materials at high cutting speeds.
- superalloys
superalloys
Tough, difficult-to-machine alloys; includes Hastelloy, Inconel and Monel. Many are nickel-base metals.
- tap
tap
Cylindrical tool that cuts internal threads and has flutes to remove chips and carry tapping fluid to the point of cut. Normally used on a drill press or tapping machine but also may be operated manually. See tapping.
- threading
threading
Process of both external (e.g., thread milling) and internal (e.g., tapping, thread milling) cutting, turning and rolling of threads into particular material. Standardized specifications are available to determine the desired results of the threading process. Numerous thread-series designations are written for specific applications. Threading often is performed on a lathe. Specifications such as thread height are critical in determining the strength of the threads. The material used is taken into consideration in determining the expected results of any particular application for that threaded piece. In external threading, a calculated depth is required as well as a particular angle to the cut. To perform internal threading, the exact diameter to bore the hole is critical before threading. The threads are distinguished from one another by the amount of tolerance and/or allowance that is specified. See turning.
- titanium carbide ( TiC)
titanium carbide ( TiC)
Extremely hard material added to tungsten carbide to reduce cratering and built-up edge. Also used as a tool coating. See coated tools.
- titanium carbonitride ( TiCN)
titanium carbonitride ( TiCN)
Often used as a tool coating. See coated tools.
- titanium nitride ( TiN)
titanium nitride ( TiN)
Added to titanium-carbide tooling to permit machining of hard metals at high speeds. Also used as a tool coating. See coated tools.
- tungsten carbide ( WC)
tungsten carbide ( WC)
Intermetallic compound consisting of equal parts, by atomic weight, of tungsten and carbon. Sometimes tungsten carbide is used in reference to the cemented tungsten carbide material with cobalt added and/or with titanium carbide or tantalum carbide added. Thus, the tungsten carbide may be used to refer to pure tungsten carbide as well as co-bonded tungsten carbide, which may or may not contain added titanium carbide and/or tantalum carbide.
- turning
turning
Workpiece is held in a chuck, mounted on a face plate or secured between centers and rotated while a cutting tool, normally a single-point tool, is fed into it along its periphery or across its end or face. Takes the form of straight turning (cutting along the periphery of the workpiece); taper turning (creating a taper); step turning (turning different-size diameters on the same work); chamfering (beveling an edge or shoulder); facing (cutting on an end); turning threads (usually external but can be internal); roughing (high-volume metal removal); and finishing (final light cuts). Performed on lathes, turning centers, chucking machines, automatic screw machines and similar machines.