Collaborative robots are increasingly being used to assist in manufacturing processes and have proven especially effective for simplifying material removal activities, such as sanding, grinding and polishing. Automating these typically tedious and dangerous tasks alleviates human workers from debilitating work while also improving safety and morale.
With artificial intelligence (AI) capabilities and visual detection systems, cobots can be taught to adjust their actions according to what they “see.” The positive impact of this technology for small- and medium-sized manufacturers is evident at the Paul Mueller Co., a Springfield, Missouri-based manufacturer of large stainless steel tanks for chemicals, beverages, petroleum products and other liquids.
After welding steel tank parts together, a technician manually grinds the weld seams with a heavy, handheld tool to impart a smooth finish. For long welds on the tanks, which measure 3.66 m to 6.10 m (12' to 20') in diameter, this activity is time-consuming and grueling. Workers often suffer shoulder, wrist, back and neck injuries and fatigue, causing downtime and high turnover.
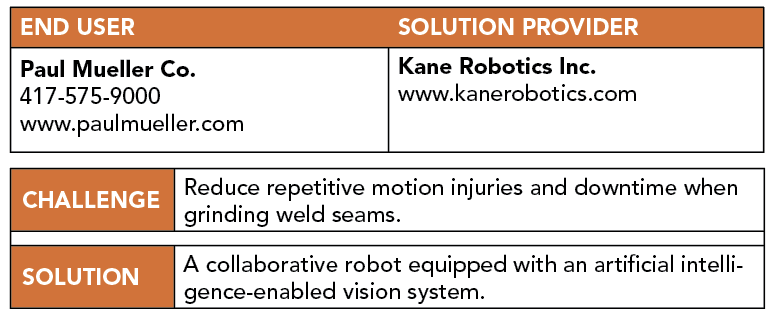
The company sought a more sustainable method for weld grinding and turned to Kane Robotics Inc., a leading developer of cobots based in Austin, Texas. Kane Robotics offers a mobile and versatile GRIT cobot that combines a robotic arm with a variety of end-of-arm tools that are preprogrammed to perform various types of material removal tasks, including metal grinding. The integration of the cobot into Paul Mueller’s manufacturing line reportedly offered Kane Robotics an opportunity to not only demonstrate the cobot’s ability to improve efficiency and safety, but also to test and perfect the company’s new GRIT Vision System. The proprietary AI-powered visual system incorporates cameras and machine learning software to teach the cobot to follow a weld seam or other uneven surface while grinding, sanding or polishing.
To incorporate the cobot system into Paul Mueller’s tank fabrication processes, Kane Robotics engineers first introduced the GRIT. The cobot easily integrated into the assembly line with its 110-volt electrical connection and flexible configuration. Kane equipped the robotic arm with an end-of-arm tool purpose-built for weld grinding, and preprogrammed the cobot to apply the appropriate speed and force over the correct area and duration to grind weld seams on the tanks.
Kane Robotics reports that its engineers quickly taught human operators to configure the cobot. Because most of the programming was already done, technicians only had to learn a few simple commands on the user-friendly interface. Installation was complete in a matter of hours, with the system up and running within days.
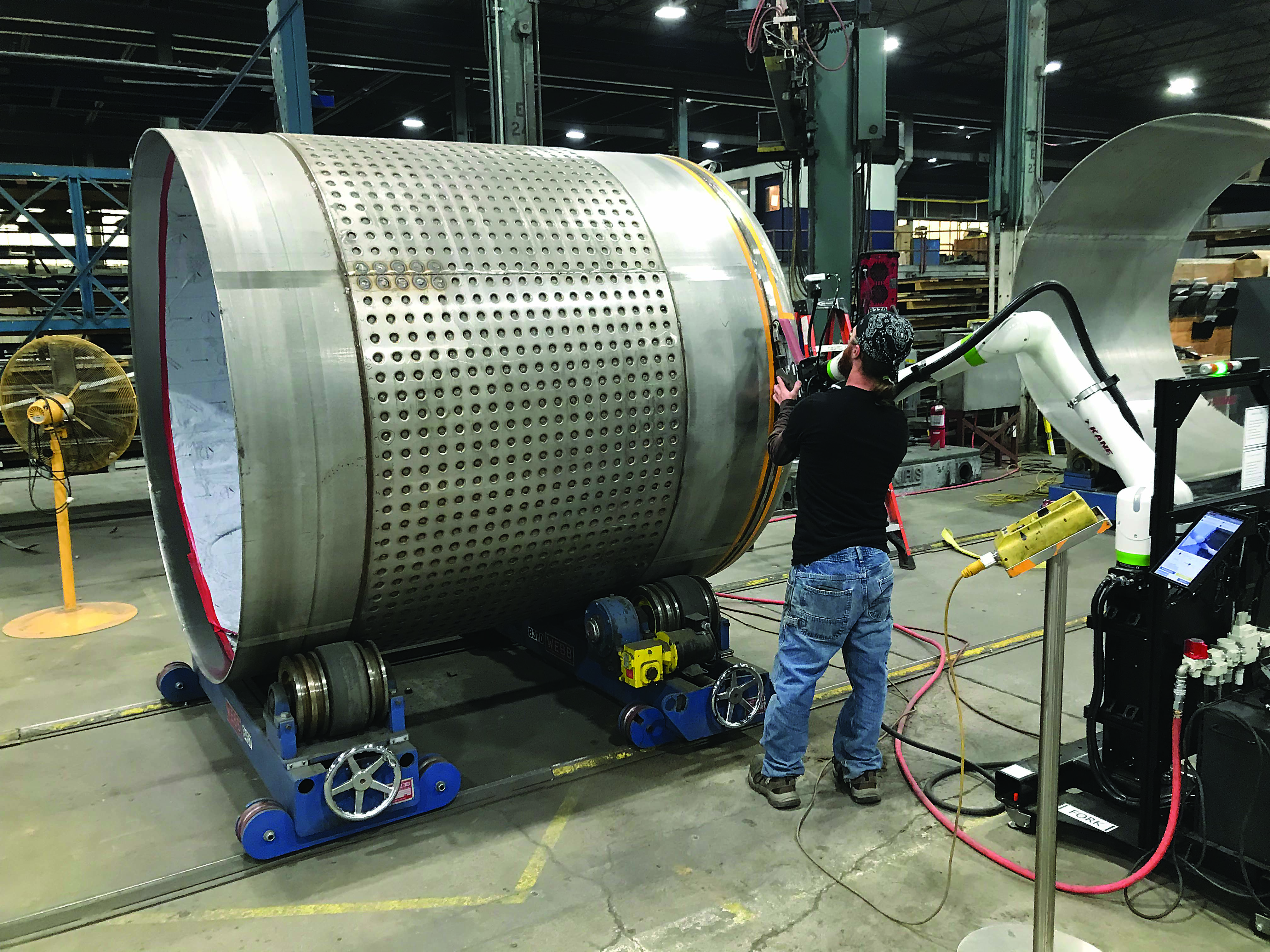
GRIT had already been proven to double weld-grinding efficiency in other use cases. The installation at Paul Mueller offered an additional benefit, as the vision system could make automated grinding even more accurate by tracking uneven weld seams and redirecting the robotic arm accordingly. The advanced vision system includes a camera attached to the cobot’s arm. A human operator positions the camera, and then the AI software performs live object detection on the weld seam.
The camera captures dozens of frames per second as the weld seam passes by on one of Paul Mueller’s rotating tanks. The camera moves slightly left and right, following the imperfect seam, and the software automatically recalibrates the robotic arm’s movement to direct the weld-grinding tool along the correct path.
The intelligent system learns to see the varying weld seam even as it disappears, as it has been taught to differentiate between an unfinished weld and a finished weld. As engineers capture more and more visual data for different types of weld seams, they teach the vision system to grind seams on various-sized tank shells and parts. Over time, the cobot solution learns to detect variations in welds and improve its accuracy. With Kane’s collaborative system, the robot does 80% of the taxing and debilitating work, while humans perform the remaining 20% that requires judgment and decision-making.
The cobot performs the physically demanding work of holding the grinding tool, and the vision system does the tiring job of detecting the wavering weld seam. The human operator adjusts the grinding speed, the appropriate force level for the selected abrasive and the number of grind passes needed to achieve the specified finish.
After implementing the cobot and vision system, Paul Mueller reported decreased repetitive motion injuries and downtime due to worker fatigue.
The Paul Mueller team continues to relay data to Kane Robotics as the manufacturer assesses the vision system in real time. One suggested improvement was including an option in the AI interface for the operator to specify the liftoff distance before and after grinding.
The positive performance of Kane Robotics’ AI vision-equipped cobot at the Paul Mueller Co. is one example of how smart automation for material removal is transforming manufacturing processes by reducing fatigue-related injuries, enhancing efficiency and improving working conditions.
Related Glossary Terms
- abrasive
abrasive
Substance used for grinding, honing, lapping, superfinishing and polishing. Examples include garnet, emery, corundum, silicon carbide, cubic boron nitride and diamond in various grit sizes.
- fatigue
fatigue
Phenomenon leading to fracture under repeated or fluctuating stresses having a maximum value less than the tensile strength of the material. Fatigue fractures are progressive, beginning as minute cracks that grow under the action of the fluctuating stress.
- grinding
grinding
Machining operation in which material is removed from the workpiece by a powered abrasive wheel, stone, belt, paste, sheet, compound, slurry, etc. Takes various forms: surface grinding (creates flat and/or squared surfaces); cylindrical grinding (for external cylindrical and tapered shapes, fillets, undercuts, etc.); centerless grinding; chamfering; thread and form grinding; tool and cutter grinding; offhand grinding; lapping and polishing (grinding with extremely fine grits to create ultrasmooth surfaces); honing; and disc grinding.
- polishing
polishing
Abrasive process that improves surface finish and blends contours. Abrasive particles attached to a flexible backing abrade the workpiece.
- robotics
robotics
Discipline involving self-actuating and self-operating devices. Robots frequently imitate human capabilities, including the ability to manipulate physical objects while evaluating and reacting appropriately to various stimuli. See industrial robot; robot.
- vision system
vision system
System in which information is extracted from visual sensors to allow machines to react to changes in the manufacturing process.