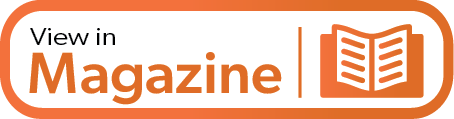
Aluminum has numerous beneficial physical properties, among them being that it is three times lighter than iron while also having a higher strength ratio. It’s also resistant to corrosion because of an aluminum-oxide layer on its exterior, and it offers good thermal conductivity and is relatively easy to machine.
Rick Crabtree, product solution manager for aluminum at Sandvik Coromant in Mebane, North Carolina, described those properties during a June 27 webinar titled “Navigating the Artistry of Aluminum Machining.” The webinar allowed Crabtree to address the rising demand for aluminum components, the corresponding challenges shops face when machining aluminum, and the cutting tools available to overcome those challenges.
Sandvik Coromant offers a range of cutting tools to effectively machine aluminum, including drills, milling tools and boring bars, according to Crabtree. For example, the M5R90 is a cartridge-based PCD cutter for roughing to semi-finishing in shoulder milling operations of automotive aluminum components, such as cylinder blocks, cylinder heads and transmission housings. The PCD tips are brazed in a steel cartridge, which allows axial adjustments. “We can run to 5 μm on axial runout, and radial runout we can achieve 50 μm.”
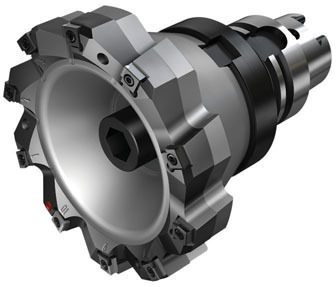
In addition, the PCD tips can be reground up to three times to prolong tool life, Crabtree said, emphasizing the need to rebalance a cutter after reconditioning the cartridge. “If they’re balanced, then we are less likely to hurt our machine spindle, and, in our instance, our balancing screws are in the side, and we can adjust those to create an even balance.”
One of the drawbacks when milling aluminum with cutters in which all the cartridges are at the same height is that burrs are likely to form, he noted. To help combat burring issues, the toolmaker offers the M5B90 fixed-pocket milling cutter, which resembles a rotary broach more than a milling tool because it is designed with a unique axial and radial positioning of the inserts, the company reports. The unique design allows chips to be cut efficiently since the minimum stock removal from each insert results in burr-free milling, which is often unavoidable with conventional milling cutters.
“If we look at the projection, or the flatness,” Crabtree said, “they are all stepped down, so our wiper only cuts 30 μm of stock at the end. Every other insert is there for roughing to make the wiper last very long.”
For one-shot roughing and finishing of thin-wall aluminum parts, the M5F90 facemill is available, and provides a rotary broaching action like the M5B90 cutter, Crabtree noted. Each insert contains both a roughing edge on the OD and a finishing edge on the facing diameter. The roughing area works as a conventional cutter and all roughing edges are on the same diameter and height. The finishing area works as an M5B90 cutter and consists of radial and axial stepped cutting edges. This positioning ensures burr-free milling.
For drilling nonferrous metals, Crabtree suggested the CoroDrill 860-NM, “an optimized drill to do high-feed penetration rates in aluminum. It has a low helix angle to help with stability and chip control.”
Related Glossary Terms
- boring
boring
Enlarging a hole that already has been drilled or cored. Generally, it is an operation of truing the previously drilled hole with a single-point, lathe-type tool. Boring is essentially internal turning, in that usually a single-point cutting tool forms the internal shape. Some tools are available with two cutting edges to balance cutting forces.
- broach
broach
Tapered tool, with a series of teeth of increasing length, that is pushed or pulled into a workpiece, successively removing small amounts of metal to enlarge a hole, slot or other opening to final size.
- broaching
broaching
Operation in which a cutter progressively enlarges a slot or hole or shapes a workpiece exterior. Low teeth start the cut, intermediate teeth remove the majority of the material and high teeth finish the task. Broaching can be a one-step operation, as opposed to milling and slotting, which require repeated passes. Typically, however, broaching also involves multiple passes.
- conventional milling ( up milling)
conventional milling ( up milling)
Cutter rotation is opposite that of the feed at the point of contact. Chips are cut at minimal thickness at the initial engagement of the cutter’s teeth with the workpiece and increase to a maximum thickness at the end of engagement. See climb milling.
- facemill
facemill
Milling cutter for cutting flat surfaces.
- gang cutting ( milling)
gang cutting ( milling)
Machining with several cutters mounted on a single arbor, generally for simultaneous cutting.
- helix angle
helix angle
Angle that the tool’s leading edge makes with the plane of its centerline.
- milling
milling
Machining operation in which metal or other material is removed by applying power to a rotating cutter. In vertical milling, the cutting tool is mounted vertically on the spindle. In horizontal milling, the cutting tool is mounted horizontally, either directly on the spindle or on an arbor. Horizontal milling is further broken down into conventional milling, where the cutter rotates opposite the direction of feed, or “up” into the workpiece; and climb milling, where the cutter rotates in the direction of feed, or “down” into the workpiece. Milling operations include plane or surface milling, endmilling, facemilling, angle milling, form milling and profiling.
- milling cutter
milling cutter
Loosely, any milling tool. Horizontal cutters take the form of plain milling cutters, plain spiral-tooth cutters, helical cutters, side-milling cutters, staggered-tooth side-milling cutters, facemilling cutters, angular cutters, double-angle cutters, convex and concave form-milling cutters, straddle-sprocket cutters, spur-gear cutters, corner-rounding cutters and slitting saws. Vertical cutters use shank-mounted cutting tools, including endmills, T-slot cutters, Woodruff keyseat cutters and dovetail cutters; these may also be used on horizontal mills. See milling.
- outer diameter ( OD)
outer diameter ( OD)
Dimension that defines the exterior diameter of a cylindrical or round part. See ID, inner diameter.
- polycrystalline diamond ( PCD)
polycrystalline diamond ( PCD)
Cutting tool material consisting of natural or synthetic diamond crystals bonded together under high pressure at elevated temperatures. PCD is available as a tip brazed to a carbide insert carrier. Used for machining nonferrous alloys and nonmetallic materials at high cutting speeds.
- wiper
wiper
Metal-removing edge on the face of a cutter that travels in a plane perpendicular to the axis. It is the edge that sweeps the machined surface. The flat should be as wide as the feed per revolution of the cutter. This allows any given insert to wipe the entire workpiece surface and impart a fine surface finish at a high feed rate.