Readers of Cutting Tool Engineering have likely made two observations about the modern machining industry.
First, the industry has experienced dramatic changes over the last 20 years. This point is proven by the bewildering variety of cutting tool geometries, substrates, coatings, toolholders, specialized machine tools, automation and software solutions available to modern manufacturers. Global competition, non-traditional materials and machine tools themselves have all driven the industry toward one fact: everything is designed to optimize the performance of the cutting tool in the cut. Specialized, high-performance tooling is now normative among high-volume manufacturers. In turn, the industry has found new ways to use this tooling, and this specialization has unlocked a silent surge of innovation across aerospace, automotive, medical, semiconductor and other industries.
Second, most undergraduate-level engineering education about machining processes hasn’t kept pace with technological advancements. The industry itself is starved for talent, and new graduates have very little context for making wise business decisions or pushing the technical boundaries of what machining can accomplish. Engineering students have usually made a few aluminum parts using low-quality tools, low-quality toolholders, and low-quality machines — with machining strategies that represent the state of the industry several decades old. Today’s world is starkly different. Material removal rates are higher, tolerances are tighter, surface quality is more controlled, and machined parts are smaller (or larger!) than most graduating engineers can imagine. Machine tools, software and automation are expected to accomplish what was impossible 20 years ago. The types of materials that can be profitably machined — and the rules and tools for machining those materials successfully — go far beyond any experience that a student might have had in a university lab.
This context is the motivation behind a new engineering course at Utah Tech University. The new course aims to create a wave of engineers who possess a fascination with the machining industry and a relevant foundation to navigate real-world decisions about modern machining processes.
Called “MECH 4990 - Modern Machining,” Utah Tech’s new course is a technical elective for junior and senior engineering students with an interest in manufacturing generally and machining processes specifically. The course is a mixture of technically deep lectures and challenging labs, but the approach is markedly different from that of most other universities. The entire course is based on one fundamental question: What do engineers need to know about modern machining processes?
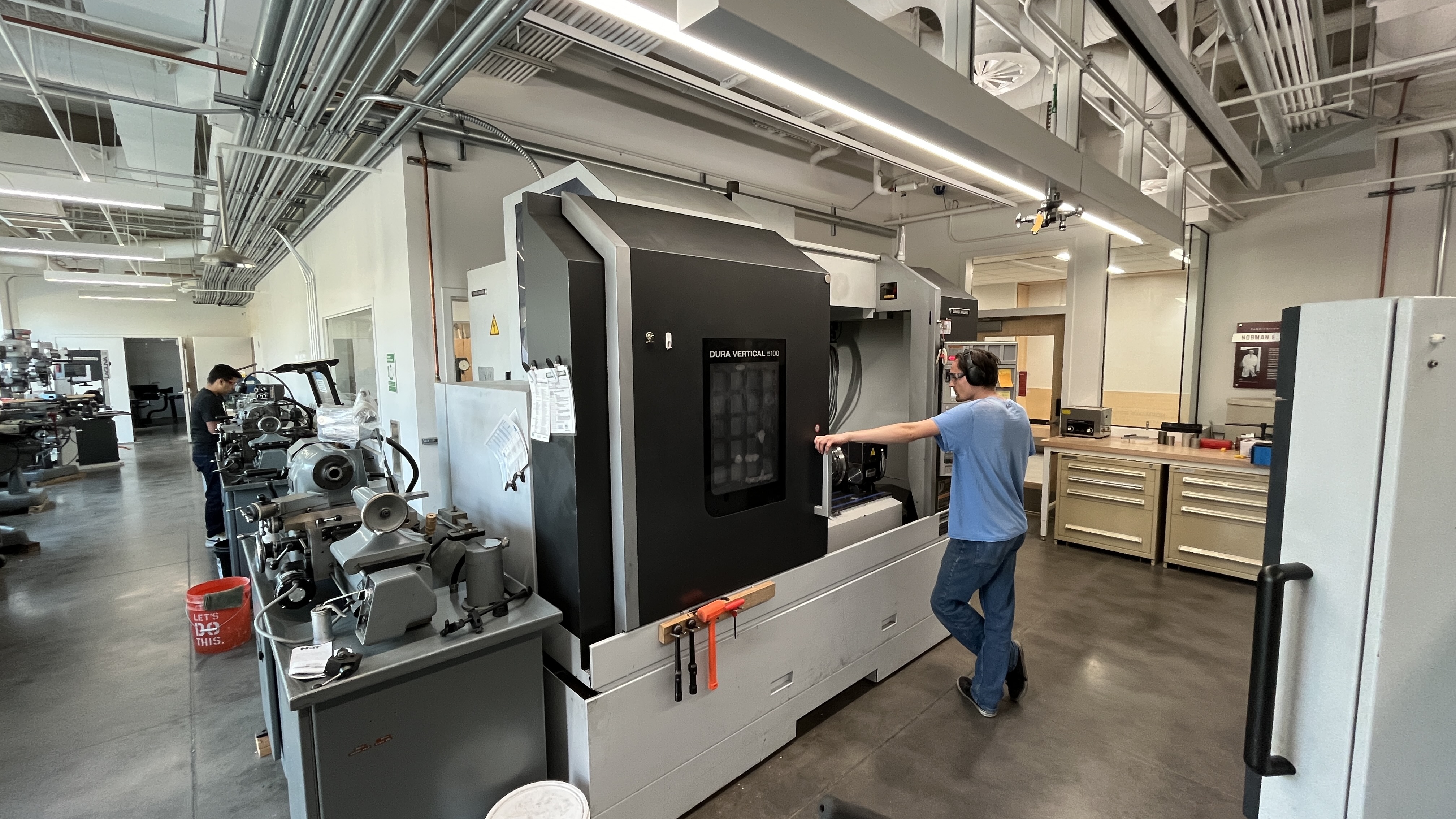
Most undergraduate-level engineering education about machining is run as if it were a crash course for would-be machinists. Typically run by ex-machinists who certainly have valuable insight, these courses can train students to design or make one or two parts with moderate success. However, they lack elements needed to prepare engineers to make engineering decisions — decisions about creating parts repeatably, reliably and profitably. In these situations, details and decisions about cutting tools, toolholding, workholding, machining strategies, automation, software, and even machine kinematics have an enormous influence on the overall success and profitability of a process. In order to help engineers make wise decisions about modern machining processes, this course is distinguished by three core ideas.
Technical Depth
First, engineering students need more technical depth. It is unfortunate how many engineers and machinists graduate without any understanding of carbide substrate quality, what phenomena actually drive chatter, when to consider PCD tooling, or even an awareness of the differences between ISO material groups. Therefore, the technical depth of this course goes beyond what most engineers (and many trained machinists) may know.
The course begins with the physics and thermodynamics of chip formation, helping students understand fundamental phenomena that constrain machining processes: temperature and force. Students will see where heat is generated as the chip is formed, how cutting forces are affected by machining strategy or chip formation, or what work-hardening actually is. These fundamentals will be used to talk about how macro- and micro-geometry affects cutting tool performance. Students also will learn to identify geometries suitable for certain materials or cutting conditions. The course will include a significant discussion of sintered carbide substrate manufacture, morphology and coating — helping students understand the reasons for choosing particular substrates and coatings for particular applications. Alternative cutting tool materials like PCD, cermets and ceramics also will be covered.
Once the cutting process and tool construction is understood, the course will move on to a broader understanding of machining processes themselves. Lectures on machine kinematics and vibration will help students understand sources of dimensional error and poor surface quality. One lecture will introduce milling toolholder technologies — both tool and spindle side — comparing their relative benefits and limitations. Specific machining strategies like trochoidal or high-feed machining will be covered, and another lecture will discuss considerations for hole making and reaming.
Pulling all this information together, several lectures cover considerations for successfully machining each ISO material group, composites and ceramics. From there, students will discuss workholding, zero-point clamping, palletization and automation — learning how and why these solutions can affect cycle time and improve dimensional repeatability.
In each case, the goal is to tie technical topics to machining economics, helping students understand how small decisions can have a big impact on the productivity of a machine tool. Since the time spent cutting material is often (or should be!) the most significant limitation for a machining process, all aspects of the process — from the design of the machine tool to the cutting fluid to the software — exist to support what happens at the cutting edge. As tool designer Viktor Astakhov is known for saying, “productivity is literally determined on the tool cutting edge.” (Astakhov, Viktor P. High-Productivity Drilling Tools: Design and Geometry. CRC Press, 2nd ed. 19-20. )
Hands-on Learning
But this course is not merely theoretical. It is profoundly hands-on, which is the second core idea that distinguishes it from typical machining education. To be fair, hands-on experience with machining is not unique among engineering curricula. But in many cases those experiences are only minimally applicable to what engineers actually do. A student who has only ever machined individual aluminum parts with low-cost tools on a low-cost machine using a vise is simply unprepared to make decisions in a high-volume role.
This course aims to make hands-on experience more relevant. Students won’t simply hear a lecture about PCD cutting tools, they’ll be running tests in a real machine to measure how PCD cutting tools can reduce cycle time and improve surface finish. After a lecture about substrate quality and cutting tool geometry, students will test multiple endmills to their breaking point to compare how substrate quality and geometry affect material removal rate and surface finish. After a lecture about vibration and harmonics, students will measure the frequency response functions of an identical tool in different toolholders, generating stability lobe diagrams for each one. By intentionally using a tool in stable and unstable conditions, students will learn why pushing tools harder and faster can sometimes make a cut more stable.
The course will also include several projects specially designed to give students relevant experiences. They will machine a titanium or nickel impeller designed by students in another course. The choice of material is intentionally difficult, and the purpose is to put students in a situation where they need to think carefully about their tool selection and approach. Another project will require students to design a multi-operation part, and then design a process (selecting workholding, designing fixtures, etc.) to make 10 of those parts repeatably. They will write work instructions for a different student to machine their 10 parts while they record data like cycle time and spindle uptime.
One project in particular deserves special mention. After discussing the details of cutting tool geometry, students will use professional endmill design software to design their own endmill for a specific cutting scenario. Since this course will have 12 students annually, the plan is to find 12 companies that would be willing to grind one of these custom endmills every year. The students then will test these endmills in a competition to see who has designed the best endmill for a specific scenario. The project is bold and full of logistical challenges; but it promises to be an amazing experience for students who are already interested in the machining industry. Imagine interviewing at a cutting tool manufacturer and being able to talk about your experience designing and testing your own endmill.
The final project is perhaps the most real-world of all. Students will find a company doing machining, anywhere in the country, and work with them to identify a problem, pain point or question. Maybe a company wants to reduce cycle time, avoid burrs on a drilled hole, improve surface finish, machine without coolant, or reduce chatter on a specific feature. Students will discuss the issue, work with tooling manufacturers, run tests using Utah Tech’s tooling and machines, and then write a report that explains the financial and technical benefits of actionable solutions. Students may suggest that companies purchase a specific tool, a new toolholder or workholding solution. This project gives students a realistic connection with actual machining processes, and it provides an opportunity for tooling and workholding manufacturers who partner with Utah Tech to put their products in front of real companies in a very personal way.
Exposure to World-Class Tools
The third core idea behind this course stems from the first two. To get excited about the technical depth of the machining industry, and to get experiences that apply to real-world decisions, engineers ought to be exposed to world-class products. The software, cutting tools, toolholders and other equipment used in a course like this should be representative of the products used by high-precision, high-volume manufacturers around the world.
This third core idea requires some justification. In an educational setting, why insist on giving students access to expensive machine tools, software and tooling with capabilities beyond what they really need? The answer is simple: because this is what engineers need to know about modern machining processes.
Unfortunately, for the sake of simplicity and cost, educational institutions almost universally use inexpensive machines, running inexpensive endmills, held in low- or average-quality sidelock or ER-style toolholders. And they run tools conservatively to avoid breaking things. Logistically and financially, this is safe; but it cultivates a false mindset that expensive tooling or workholding is unnecessary, that details don’t matter, and that machining problems are solved by slowing down. Even worse, this approach can give the impression that machining itself is uninteresting or archaic.
At Utah Tech, students will use some sidelock and ER-style holders, but more often they will use a mix of high-quality collet chucks, milling chucks and hydraulic toolholders, some of which take advantage of Utah Tech’s dual-contact spindle with TSC. Likewise, the endmills and drills students will use are of diverse quality. When high-quality cutting tools and toolholders are paired with a very capable machine, students will be startled to learn how hard they can run the tools. The course also will encourage students to machine parts from a variety of materials that would ordinarily be considered problematic in an educational environment — 304 stainless is one of the most common materials in Utah Tech's lab.
All of this variety serves a purpose. To be educated about machining processes, engineers don’t merely need to make parts. They need to think about how to make parts best. Engineers need experiences that help them navigate the complex choices they’ll face in a real job. To limit students to one specific type tooling or material would contradict this goal.
When students enter the workforce, why should they spend extra money on high-quality tooling, workholding, software or machine tools? Why use balanced toolholders? Why not just use the bare minimum? To answer these questions, they need to run production machines, use world-class tooling, cut materials that require careful planning, and program at the edge of a tool’s capability. Rather than aiming to be conservative, students must learn to maximize MRR by using tools the way they were designed to be used. Using world-class products will help students see why details about machining process really matter. After they graduate, it will give them the mindset and knowledge they need to thrive in the machining industry.
Industry Benefits
At a time when American manufacturing is experiencing a sort of resurgence, and when novel machining technologies are enabling innovation in other fields, the need for trained machinists is clear. But the need for deeper technical and practical expertise is often overlooked. Too many companies are unnecessarily held back by outdated notions that ultimately hurt their ability to compete. When they encounter a problem related to machining, an engineer or a machinist’s gut instinct might be to slow down. Some companies even claim not to have any problems with chatter simply because they never run their tools hard enough to find out! Others can’t justify using more expensive tooling because they’ve never seen how it can make a significant difference. Others buy machine tools purely based on capital cost, without considering how factors like dynamic stiffness, jerk or spindle rigidity might affect their cycle time. And many companies could benefit from some level of automation or palletization, but they simply don’t employ anyone who understands how to leverage these solutions wisely.
With technical knowledge to understand the root of a problem, and practical experience to make wise decisions about improving it, engineers who complete this course will have the mindset that this industry needs. When these students join the workforce and encounter a problem, they will be able to say, “I remember a time when the cutting tool geometry, the substrate, the machining parameters, the toolholder, the workholding or the machine tool made a huge difference in the success of a process. I was able to get amazing results when I used tools right. Let’s see what I can do.”
Course Challenges
Exposing students to modern machining practices sounds wonderful, but it is easier said than done. There are significant challenges, none more significant than budget. Giving students hands-on experiences with machine tools, tooling and raw materials is unavoidably costly. This point alone is perhaps one of the main reasons that machining education has fallen out of step with current trends. And this course, with its focus on world-class tooling and experience with difficult materials, will only amplify those costs. With such a prohibitive price tag, how can an engineering program hope to start a course like this?
Hopefully, with the machining industry’s help. Little by little, the manufacturing lab at Utah Tech has already been shaped by generosity. A few cutting tool, toolholder and workholding manufacturers have made donations or offered steep discounts that allow Utah Tech to use equipment that it could never afford otherwise. They do this because they see it as a win-win. They help Utah Tech do what it couldn’t do alone, and they put their products in the hands of potential future customers.
Even so, this new Modern Machining course requires further partnerships with interested companies. The needs are varied. Big or small, whether one-time gifts or annual support, used or new, Utah Tech needs tooling, raw materials, inspection equipment, access to software, discounts or even financial contributions from companies that want to see engineering education about machining changed.
Expertise also is needed. As the one teaching this course, I cannot be an expert in all things, and in order to make this course as relevant as possible, I want to work closely with industry professionals to develop lectures that are technically accurate and up to date. In fact, I want to start lectures by acknowledging the companies and individuals that helped develop them. For example, Lach Diamond will be featured in a lecture, and their tooling featured in a lab because a few of their folks spent several generous hours educating me about the history and use of PCD cutting tools. I also plan to take the students to a Sandvik Coromant facility in Utah that manufactures PCD cutting tools. For the students, the benefit goes beyond the classroom. I want them to graduate knowing real companies or real people that can help them when they encounter problems in a real job.
In the years to come, I want to improve the kind of equipment that we use to teach this course. Right now Utah Tech has two well-made machines — a mill and a lathe — both older DMG Mori models. They’re fantastic to start with, and frankly more machine than most engineering students ever see, but our capabilities are still limited. In the future, I want this course to include hands-on experiences related to micromachining, diamond turning, and 5-axis processes. I hope to acquire machine-tools that allow us to do that.
Goals
I have great hopes for this course. I want to see students become fascinated by the machining industry. I regularly speak with company representatives in the industry who describe a need for qualified engineering talent — not merely engineers who are technically capable, but engineers who are actually excited about their industry.
For too many decades, American engineering education has silently — mostly unknowingly — discouraged students from careers related to manufacturing. In some academic settings, manufacturing has a reputation as dirty, uninteresting work largely unfit for those with an advanced degree. This reputation is disconnected from both history and present reality. The humble factory has always been a massive engine of technical innovation, and I want this course to restore a sense of wonder, nobility and respect to careers in manufacturing. Specifically, I hope this course inspires students to pursue meaningful, lifelong careers in an industry that invisibly enables so many aspects of modern life and human flourishing.
If you are reading this magazine, I want these students to be excited about working at your company, helping you design better tools, run better processes, or build better machines. I want these students to pursue graduate degrees related to machining and then work at your company. Eventually, I want these students to be the ones making waves in this amazing industry.
This course represents the beginning of a larger movement to change the way that engineers are educated about machining processes. If students’ excitement about the course means anything, my hopes are high. Less than four minutes after midnight when Spring 2025 registration opened to Utah Tech students, the course and waitlist were both full.
Related Glossary Terms
- ceramics
ceramics
Cutting tool materials based on aluminum oxide and silicon nitride. Ceramic tools can withstand higher cutting speeds than cemented carbide tools when machining hardened steels, cast irons and high-temperature alloys.
- cermets
cermets
Cutting tool materials based mostly on titanium carbonitride with nickel and/or cobalt binder. Cermets are characterized by high wear resistance due to their chemical and thermal stability. Cermets are able to hold a sharp edge at high cutting speeds and temperatures, which results in exceptional surface finish when machining most types of steels.
- chatter
chatter
Condition of vibration involving the machine, workpiece and cutting tool. Once this condition arises, it is often self-sustaining until the problem is corrected. Chatter can be identified when lines or grooves appear at regular intervals in the workpiece. These lines or grooves are caused by the teeth of the cutter as they vibrate in and out of the workpiece and their spacing depends on the frequency of vibration.
- collet
collet
Flexible-sided device that secures a tool or workpiece. Similar in function to a chuck, but can accommodate only a narrow size range. Typically provides greater gripping force and precision than a chuck. See chuck.
- composites
composites
Materials composed of different elements, with one element normally embedded in another, held together by a compatible binder.
- coolant
coolant
Fluid that reduces temperature buildup at the tool/workpiece interface during machining. Normally takes the form of a liquid such as soluble or chemical mixtures (semisynthetic, synthetic) but can be pressurized air or other gas. Because of water’s ability to absorb great quantities of heat, it is widely used as a coolant and vehicle for various cutting compounds, with the water-to-compound ratio varying with the machining task. See cutting fluid; semisynthetic cutting fluid; soluble-oil cutting fluid; synthetic cutting fluid.
- cutting fluid
cutting fluid
Liquid used to improve workpiece machinability, enhance tool life, flush out chips and machining debris, and cool the workpiece and tool. Three basic types are: straight oils; soluble oils, which emulsify in water; and synthetic fluids, which are water-based chemical solutions having no oil. See coolant; semisynthetic cutting fluid; soluble-oil cutting fluid; synthetic cutting fluid.
- cutting tool materials
cutting tool materials
Cutting tool materials include cemented carbides, ceramics, cermets, polycrystalline diamond, polycrystalline cubic boron nitride, some grades of tool steels and high-speed steels. See HSS, high-speed steels; PCBN, polycrystalline cubic boron nitride; PCD, polycrystalline diamond.
- dynamic stiffness
dynamic stiffness
Measure of a machining system’s ability to dampen vibration from a forced input. If the dynamic stiffness of a system is not sufficient to dampen vibration, chatter occurs. See static stiffness; stiffness.
- endmill
endmill
Milling cutter held by its shank that cuts on its periphery and, if so configured, on its free end. Takes a variety of shapes (single- and double-end, roughing, ballnose and cup-end) and sizes (stub, medium, long and extra-long). Also comes with differing numbers of flutes.
- gang cutting ( milling)
gang cutting ( milling)
Machining with several cutters mounted on a single arbor, generally for simultaneous cutting.
- lathe
lathe
Turning machine capable of sawing, milling, grinding, gear-cutting, drilling, reaming, boring, threading, facing, chamfering, grooving, knurling, spinning, parting, necking, taper-cutting, and cam- and eccentric-cutting, as well as step- and straight-turning. Comes in a variety of forms, ranging from manual to semiautomatic to fully automatic, with major types being engine lathes, turning and contouring lathes, turret lathes and numerical-control lathes. The engine lathe consists of a headstock and spindle, tailstock, bed, carriage (complete with apron) and cross slides. Features include gear- (speed) and feed-selector levers, toolpost, compound rest, lead screw and reversing lead screw, threading dial and rapid-traverse lever. Special lathe types include through-the-spindle, camshaft and crankshaft, brake drum and rotor, spinning and gun-barrel machines. Toolroom and bench lathes are used for precision work; the former for tool-and-die work and similar tasks, the latter for small workpieces (instruments, watches), normally without a power feed. Models are typically designated according to their “swing,” or the largest-diameter workpiece that can be rotated; bed length, or the distance between centers; and horsepower generated. See turning machine.
- milling
milling
Machining operation in which metal or other material is removed by applying power to a rotating cutter. In vertical milling, the cutting tool is mounted vertically on the spindle. In horizontal milling, the cutting tool is mounted horizontally, either directly on the spindle or on an arbor. Horizontal milling is further broken down into conventional milling, where the cutter rotates opposite the direction of feed, or “up” into the workpiece; and climb milling, where the cutter rotates in the direction of feed, or “down” into the workpiece. Milling operations include plane or surface milling, endmilling, facemilling, angle milling, form milling and profiling.
- milling machine ( mill)
milling machine ( mill)
Runs endmills and arbor-mounted milling cutters. Features include a head with a spindle that drives the cutters; a column, knee and table that provide motion in the three Cartesian axes; and a base that supports the components and houses the cutting-fluid pump and reservoir. The work is mounted on the table and fed into the rotating cutter or endmill to accomplish the milling steps; vertical milling machines also feed endmills into the work by means of a spindle-mounted quill. Models range from small manual machines to big bed-type and duplex mills. All take one of three basic forms: vertical, horizontal or convertible horizontal/vertical. Vertical machines may be knee-type (the table is mounted on a knee that can be elevated) or bed-type (the table is securely supported and only moves horizontally). In general, horizontal machines are bigger and more powerful, while vertical machines are lighter but more versatile and easier to set up and operate.
- polycrystalline diamond ( PCD)
polycrystalline diamond ( PCD)
Cutting tool material consisting of natural or synthetic diamond crystals bonded together under high pressure at elevated temperatures. PCD is available as a tip brazed to a carbide insert carrier. Used for machining nonferrous alloys and nonmetallic materials at high cutting speeds.
- stiffness
stiffness
1. Ability of a material or part to resist elastic deflection. 2. The rate of stress with respect to strain; the greater the stress required to produce a given strain, the stiffer the material is said to be. See dynamic stiffness; static stiffness.
- toolholder
toolholder
Secures a cutting tool during a machining operation. Basic types include block, cartridge, chuck, collet, fixed, modular, quick-change and rotating.
- turning
turning
Workpiece is held in a chuck, mounted on a face plate or secured between centers and rotated while a cutting tool, normally a single-point tool, is fed into it along its periphery or across its end or face. Takes the form of straight turning (cutting along the periphery of the workpiece); taper turning (creating a taper); step turning (turning different-size diameters on the same work); chamfering (beveling an edge or shoulder); facing (cutting on an end); turning threads (usually external but can be internal); roughing (high-volume metal removal); and finishing (final light cuts). Performed on lathes, turning centers, chucking machines, automatic screw machines and similar machines.