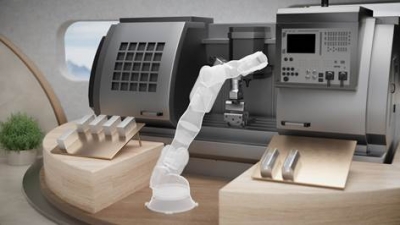
OnRobot has launched the 2FG7, a complete, low cost, easy to use, out-of-the-box, cleanroom-ready parallel gripper. Designed to enable companies of all sizes to set up gripping applications at low cost, the 2FG7 can be deployed within minutes and is specially designed to handle demanding payloads –even in tight spaces. The new 2FG7 gripper is ideal for low-volume, high-mix production and enables fast ROI for many different applications, including machine tending, material handling and assembly.
“Our customers asked for a parallel gripper that can handle payloads above 6 kg (13.22 lb) without sacrificing the ease of use that they have come to expect from OnRobot's products. Combining strength, functionality and easy programming in a small form factor, the 2FG7 is that powerful, production-ready gripper,” says Enrico Krog Iversen, CEO of OnRobot.
Boasting a maximum payload of 11 kg (24.3 lb), an external grip range of up to 74 mm (2.91 in) and a gripping force of between 20-140 N, the versatile 2FG7 can handle heavy, bulky payloads with ease. Smaller than OnRobot's RG2 and RG6 grippers –and yet more powerful than both –the 2FG7's dimensions (156 x 158 x 180 mm/6.14 x 6.22 x 7.08 in) make it the perfect gripper for use in small work envelopes, which is a major bonus in busy manufacturing facilities where space is at a premium, and in applications with tight quarters for maneuvering.
“The cost of robot hardware components has declined in recent years, but this hasn't translated into a benefit to smaller manufacturing companies because the vast majority of industrial robot peripherals remain prohibitively complex and time-consuming to deploy,” explains CEO Iversen. “OnRobot is changing all that.”
Seamlessly integrated with the OnRobot product range and compatible with all major collaborative robots and light industrial robot arms, the 2FG7 allows manufacturers of all skillsets to set up gripping applications quickly and easily. The 2FG7's ease of use ensures visibility during the deployment process, greatly reduces the need for custom parts and cuts the time to ROI. Meanwhile, intelligent feedback features, including grip detection and lost grip detection, further simplify the deployment process.
Cleanroom certified
The 2FG7 is a production-ready gripper built to withstand harsh manufacturing conditions and applications. In addition to being IP67-certified, the 2FG7 has attained cleanroom certification (ISO Class 5), which is required for many handling applications in the pharmaceutical and electronics industries. It also complies with ISO/TS 15066 regarding collaborative robot cell risk assessments.
The 2FG7 is powered by an integrated electric motor, which provides several advantages over pneumatics-based gripper systems. 2FG7 users can easily program force, speed and stroke control settings through an intuitive software interface. This makes the gripper ideal for high-mix/low-volume production since it allows for quick and easy settings adjustments depending on the parts being handled.
The precision provided by the 2FG7's electric motor allows the gripper to provide a finger position resolution of 0.1 mm (0.004 in) and a gripping time of 200 mm/s. For end users, the ability to make precise adjustments to stroke, range and finger position supports flexibility across a wide range of applications.
By contrast, pneumatic grippers provide limited, low-resolution force control through air pressure adjustments. Further, pneumatic systems don't provide intelligent grip detection capabilities and can negatively impact air quality by releasing contaminants into the work environment.
“OnRobot exists to democratize automation by providing manufacturers of all sizes with low-cost, easy-to-use products that empower them to right out of the box. The 2FG7 parallel gripper is a powerful addition to OnRobot's democratizing, Plug and Produce product family,” says CEO Iversen.
Contact Details
Related Glossary Terms
- industrial robot
industrial robot
Robot designed for industrial use. Primarily used as a material-handling device but also used for changing tools, assembling parts, and manipulating special tools and measuring devices. Depending on design, an industrial robot can be programmed to perform a task by means of a controller, or it can be “walked” through the required movements by utilizing a digitizing system that translates movements into commands that the robot can be “taught.” See robot; teaching pendant.
- parallel
parallel
Strip or block of precision-ground stock used to elevate a workpiece, while keeping it parallel to the worktable, to prevent cutter/table contact.
- payload ( workload)
payload ( workload)
Maximum load that the robot can handle safely.