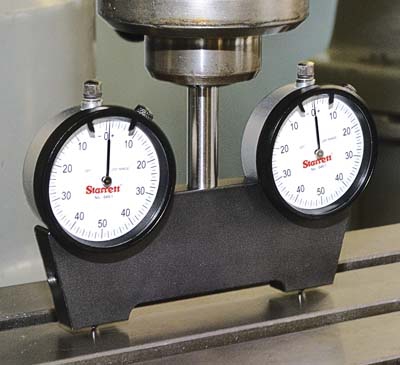
The L.S. Starrett Company has introduced its patented 649 series Spindle Square for tramming the head of a vertical milling machine. Tramming must be done regularly to ensure squareness and perpendicularity between the spindle and work surface. This device offers improved accuracy, convenience and significant time savings when compared to the traditional method of tramming with a dial test indicator, according to the company.
The Spindle Square comes assembled with two AGD Group 2 dial indicators. It has a steel body construction, black wrinkle finish and ground gaging surface. The unit weighs approximately 4 lbs. and is approximately 6¾" (172mm) wide and 5½" (140mm) long from the top of the shank to the end of the contact points.
After setting the spindle square indicators to "0" on a surface plate, the Spindle Square is placed into the collet of the milling machine. The head is brought down to the table until both indicator needles have rotated approximately one full rotation. The needles do not need to point in the same direction. Identical numerical readings, not the needle positions, indicate squareness. Normal tramming procedures are used until both indicators read the same numerical value. After setting the X-axis, the same procedure is repeated for the Y-axis.
Contact Details
Related Glossary Terms
- collet
collet
Flexible-sided device that secures a tool or workpiece. Similar in function to a chuck, but can accommodate only a narrow size range. Typically provides greater gripping force and precision than a chuck. See chuck.
- gang cutting ( milling)
gang cutting ( milling)
Machining with several cutters mounted on a single arbor, generally for simultaneous cutting.
- milling
milling
Machining operation in which metal or other material is removed by applying power to a rotating cutter. In vertical milling, the cutting tool is mounted vertically on the spindle. In horizontal milling, the cutting tool is mounted horizontally, either directly on the spindle or on an arbor. Horizontal milling is further broken down into conventional milling, where the cutter rotates opposite the direction of feed, or “up” into the workpiece; and climb milling, where the cutter rotates in the direction of feed, or “down” into the workpiece. Milling operations include plane or surface milling, endmilling, facemilling, angle milling, form milling and profiling.
- milling machine ( mill)
milling machine ( mill)
Runs endmills and arbor-mounted milling cutters. Features include a head with a spindle that drives the cutters; a column, knee and table that provide motion in the three Cartesian axes; and a base that supports the components and houses the cutting-fluid pump and reservoir. The work is mounted on the table and fed into the rotating cutter or endmill to accomplish the milling steps; vertical milling machines also feed endmills into the work by means of a spindle-mounted quill. Models range from small manual machines to big bed-type and duplex mills. All take one of three basic forms: vertical, horizontal or convertible horizontal/vertical. Vertical machines may be knee-type (the table is mounted on a knee that can be elevated) or bed-type (the table is securely supported and only moves horizontally). In general, horizontal machines are bigger and more powerful, while vertical machines are lighter but more versatile and easier to set up and operate.
- shank
shank
Main body of a tool; the portion of a drill or similar end-held tool that fits into a collet, chuck or similar mounting device.