Contact Details
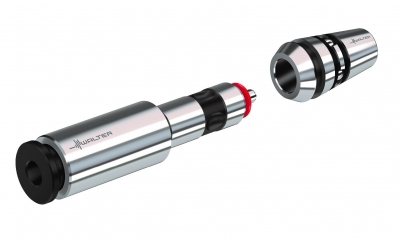
The AB735 synchronized tapping adaptor from Walter compensates for axial movement and pressure during tapping, allowing users to increase threading productivity while increasing tapping tool life. The synchronization of a machine, (i.e., the rotation of the spindle in relation to the feed) is one of the main reasons for tool wear in thread production. With the AB735 Walter offers a flexible solution which minimizes the axial forces that occur during this process.
The adaptor, which can be used in all common ER collet chucks, also means that fewer number of tools are required. Further, thread flank wear is minimized since these are strained less when chamfering. The sleek, short, compact design also makes it possible to use the adaptor in tight spaces.
More cost-effective than comparable systems but just as easy on tools, the AB735 synchronous threading adaptor maximizes tool performance. In addition to the minimized wear, the modular design of the adaptor also contributes to cost-efficiency: Exchangeable front pieces for different thread sizes or tool diameters (ER16 to ER32) can be used with the same collet. It also fits in virtually all ER adaptors, without requiring further investments.
The low maintenance requirements and high level of process reliability of the adaptor also have additional positive effects, for example, by reducing the risk of breaking the threading tool. Walter offers the quick-change system for all tool types with or without internal coolant. The AB375 accommodates internal coolant of up to 725 psi (50 bar), as well as external coolant supply. It is particularly well suited to applications in the series production of threads and/or applications where lack of synchronization results in a high tool wear rate.
Related Glossary Terms
- chamfering
chamfering
Machining a bevel on a workpiece or tool; improves a tool’s entrance into the cut.
- collet
collet
Flexible-sided device that secures a tool or workpiece. Similar in function to a chuck, but can accommodate only a narrow size range. Typically provides greater gripping force and precision than a chuck. See chuck.
- coolant
coolant
Fluid that reduces temperature buildup at the tool/workpiece interface during machining. Normally takes the form of a liquid such as soluble or chemical mixtures (semisynthetic, synthetic) but can be pressurized air or other gas. Because of water’s ability to absorb great quantities of heat, it is widely used as a coolant and vehicle for various cutting compounds, with the water-to-compound ratio varying with the machining task. See cutting fluid; semisynthetic cutting fluid; soluble-oil cutting fluid; synthetic cutting fluid.
- flank wear
flank wear
Reduction in clearance on the tool’s flank caused by contact with the workpiece. Ultimately causes tool failure.
- modular design ( modular construction)
modular design ( modular construction)
Manufacturing of a product in subassemblies that permits fast and simple replacement of defective assemblies and tailoring of the product for different purposes. See interchangeable parts.
- tapping
tapping
Machining operation in which a tap, with teeth on its periphery, cuts internal threads in a predrilled hole having a smaller diameter than the tap diameter. Threads are formed by a combined rotary and axial-relative motion between tap and workpiece. See tap.
- threading
threading
Process of both external (e.g., thread milling) and internal (e.g., tapping, thread milling) cutting, turning and rolling of threads into particular material. Standardized specifications are available to determine the desired results of the threading process. Numerous thread-series designations are written for specific applications. Threading often is performed on a lathe. Specifications such as thread height are critical in determining the strength of the threads. The material used is taken into consideration in determining the expected results of any particular application for that threaded piece. In external threading, a calculated depth is required as well as a particular angle to the cut. To perform internal threading, the exact diameter to bore the hole is critical before threading. The threads are distinguished from one another by the amount of tolerance and/or allowance that is specified. See turning.
Additional Products from Walter USA LLC
Pagination
- First page
- Previous page
- …
- 17
- 18
- 19
- 20
- 21
- 22
- 23
- 24
- 25