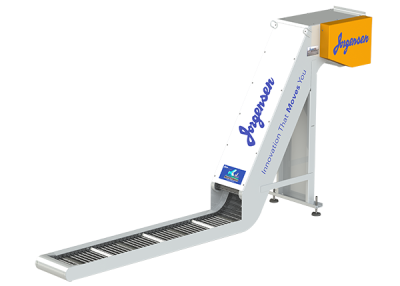
Jorgensen Conveyor and Filtration Solutions, Mequon, Wisconsin, highlighted its distinctive MunchMan hinged steel Dual-Belt Conveyor at IMTS 2024. Unique to Jorgensen, the MunchMan conveyor is well-suited for turning and milling applications that produce long, stringy or nested balls of chips and is designed to greatly reduce or eliminate conveyor jamming problems.
The MunchMan employs a unique twin-belt conveyor arrangement through the lower curve, incline and chip discharge areas of the system. The primary and secondary belts run in unison to grab hold of chips, compress them and securely carry them up steep inclines, eliminating the risk of conveyor jams caused by chip balls tumbling at the lower curve or jamming in the incline section. This patent-pending system is both efficient and cost-effective in eliminating costly machine downtime.
AR400 wear-resistant steel is used in all conveyor wear areas. Ultimate conveyor control and functionality are provided with the UVS Ecologic Control and JamManager performance. MunchMan conveyors are custom fabricated to customer requirements and have essentially the same space requirements of traditional, single-belt chip conveyors. It is compatible with other Jorgensen filtration options such as EcoFilter and PermaClean. The MunchMan conveyor is recommended as a feeder conveyor for Jorgensen’s Chip Processing System.
Contact Details
Related Glossary Terms
- gang cutting ( milling)
gang cutting ( milling)
Machining with several cutters mounted on a single arbor, generally for simultaneous cutting.
- milling
milling
Machining operation in which metal or other material is removed by applying power to a rotating cutter. In vertical milling, the cutting tool is mounted vertically on the spindle. In horizontal milling, the cutting tool is mounted horizontally, either directly on the spindle or on an arbor. Horizontal milling is further broken down into conventional milling, where the cutter rotates opposite the direction of feed, or “up” into the workpiece; and climb milling, where the cutter rotates in the direction of feed, or “down” into the workpiece. Milling operations include plane or surface milling, endmilling, facemilling, angle milling, form milling and profiling.
- turning
turning
Workpiece is held in a chuck, mounted on a face plate or secured between centers and rotated while a cutting tool, normally a single-point tool, is fed into it along its periphery or across its end or face. Takes the form of straight turning (cutting along the periphery of the workpiece); taper turning (creating a taper); step turning (turning different-size diameters on the same work); chamfering (beveling an edge or shoulder); facing (cutting on an end); turning threads (usually external but can be internal); roughing (high-volume metal removal); and finishing (final light cuts). Performed on lathes, turning centers, chucking machines, automatic screw machines and similar machines.