Contact Details
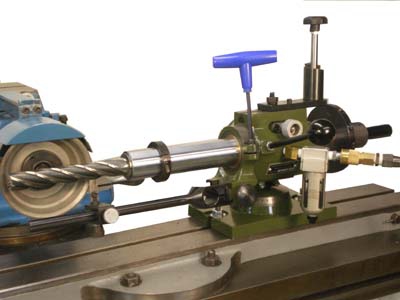
Rush Machinery Inc. offers a series of airbearing end mill grinding fixtures that allow precision sharpening of end mills, reamers, shell mills and other cutters. The spindle floats almost frictionless on a thin film of air, resulting in a smooth, even grind. The fixture quickly mounts on Rush drill and tool grinders, and it is also available with a universal base to mount on most tool and cutter or surface grinders.
The units feature a hard chrome plated and ground spindle with a 10" stroke. Tools are held by 5-C or 5-ST collets or extension bushings for up to 2" (50mm) diameter shanks. The fixtures allow for grinding the O.D. of any number of flutes and include a 12-position index plate for end grinding (other index plates are available). The micrometer infeed is graduated in .001" (.04mm) of diameter. Use of the fixture allows the operator to customize end mill geometry for optimum performance.
Related Glossary Terms
- fixture
fixture
Device, often made in-house, that holds a specific workpiece. See jig; modular fixturing.
- flutes
flutes
Grooves and spaces in the body of a tool that permit chip removal from, and cutting-fluid application to, the point of cut.
- grinding
grinding
Machining operation in which material is removed from the workpiece by a powered abrasive wheel, stone, belt, paste, sheet, compound, slurry, etc. Takes various forms: surface grinding (creates flat and/or squared surfaces); cylindrical grinding (for external cylindrical and tapered shapes, fillets, undercuts, etc.); centerless grinding; chamfering; thread and form grinding; tool and cutter grinding; offhand grinding; lapping and polishing (grinding with extremely fine grits to create ultrasmooth surfaces); honing; and disc grinding.
- micrometer
micrometer
A precision instrument with a spindle moved by a finely threaded screw that is used for measuring thickness and short lengths.
- milling machine ( mill)
milling machine ( mill)
Runs endmills and arbor-mounted milling cutters. Features include a head with a spindle that drives the cutters; a column, knee and table that provide motion in the three Cartesian axes; and a base that supports the components and houses the cutting-fluid pump and reservoir. The work is mounted on the table and fed into the rotating cutter or endmill to accomplish the milling steps; vertical milling machines also feed endmills into the work by means of a spindle-mounted quill. Models range from small manual machines to big bed-type and duplex mills. All take one of three basic forms: vertical, horizontal or convertible horizontal/vertical. Vertical machines may be knee-type (the table is mounted on a knee that can be elevated) or bed-type (the table is securely supported and only moves horizontally). In general, horizontal machines are bigger and more powerful, while vertical machines are lighter but more versatile and easier to set up and operate.