Contact Details
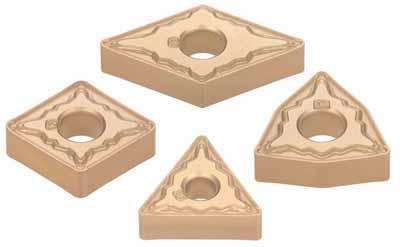
Tungaloy Corp. introduces the AM chipbreaker that increases efficiency in medium cutting of steel.
In today's metalworking industry, manufacturers are looking to improve their productivity. Increased speed and feed rates are usually the solutions to this demand. However, this also increases the cutting force on the inserts and generates excessive crater wear (wear on the rake face). This leads to sudden fracture and poor chip control due to wear on the chipbreaker.
The new AM chipbreaker features a "Lift-Ridge" shape. This latest innovation by Tungaloy minimizes the contact area between the chip and the rake surface, reduces the heat generated by chip abrasion, and prevents crater wear from developing, according to the company. The inclination on the cutting edge decreases cutting force even in machining at high speeds and feeds. In addition, optimized chipbreaker width and geometry deliver stable chip control.
The AM chipbreaker is reportedly an excellent choice for steel turning where productivity is to be improved by allowing customers to increase their process speeds and feeds.
Related Glossary Terms
- chipbreaker
chipbreaker
Groove or other tool geometry that breaks chips into small fragments as they come off the workpiece. Designed to prevent chips from becoming so long that they are difficult to control, catch in turning parts and cause safety problems.
- cutting force
cutting force
Engagement of a tool’s cutting edge with a workpiece generates a cutting force. Such a cutting force combines tangential, feed and radial forces, which can be measured by a dynamometer. Of the three cutting force components, tangential force is the greatest. Tangential force generates torque and accounts for more than 95 percent of the machining power. See dynamometer.
- feed
feed
Rate of change of position of the tool as a whole, relative to the workpiece while cutting.
- metalworking
metalworking
Any manufacturing process in which metal is processed or machined such that the workpiece is given a new shape. Broadly defined, the term includes processes such as design and layout, heat-treating, material handling and inspection.
- rake
rake
Angle of inclination between the face of the cutting tool and the workpiece. If the face of the tool lies in a plane through the axis of the workpiece, the tool is said to have a neutral, or zero, rake. If the inclination of the tool face makes the cutting edge more acute than when the rake angle is zero, the rake is positive. If the inclination of the tool face makes the cutting edge less acute or more blunt than when the rake angle is zero, the rake is negative.
- turning
turning
Workpiece is held in a chuck, mounted on a face plate or secured between centers and rotated while a cutting tool, normally a single-point tool, is fed into it along its periphery or across its end or face. Takes the form of straight turning (cutting along the periphery of the workpiece); taper turning (creating a taper); step turning (turning different-size diameters on the same work); chamfering (beveling an edge or shoulder); facing (cutting on an end); turning threads (usually external but can be internal); roughing (high-volume metal removal); and finishing (final light cuts). Performed on lathes, turning centers, chucking machines, automatic screw machines and similar machines.