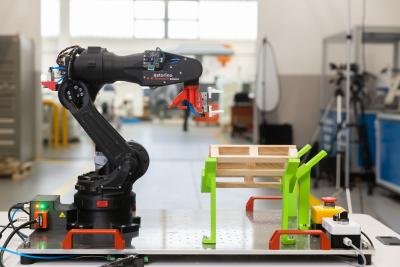
Kawasaki Robotics (USA), Inc. will premiere Astorino, a unique and affordable educational robotics platform for industrial/technical education providers, at the 2024 IMTS Smartforce Student Summit in Chicago September 9-14. Astorino offers the capabilities of a modern industrial robot at a fraction of the cost of other robots for the educational market, enabling educators to more easily equip students with the foundational, real-world skills needed as manufacturing continues to evolve.
Named after the popular open-source Arduino platform and development partner ASTOR, Astorino leverages Kawasaki Robotics’ extensive technology expertise, including hardware, firmware, control system, application software and training. The platform also supplies STL files so students can rapidly print 3D replacement parts for 99% of the robot.
“We launch the Astorino with a clear goal: to advance industrial robotics education,” said Paul Marcovecchio, Director – General Industries, Kawasaki Robotics (USA), Inc. “With this new cost-effective and dynamic robotic platform, we eliminate many barriers to entry that have kept educators from providing advanced robotics design tools to their students. Our accessible price point and ease of use will enable more educators to offer the valuable hands-on experiences so critical to success in today’s manufacturing environments.”
Affordable platform enables low student-to-equipment ratio
At the core of Astorino is a 1kg payload, 6-axis robot with a structure and programming environment nearly identical to that of a Kawasaki industrial robot. Weighing only 12 kg and powered by a 110V outlet, the robot is adoptable to any classroom environment. The Astorino platform includes a built-in control system; dedicated firmware and software; Modbus TCP and USB/Ethernet communication, and safety functions such as E-Stop and safety brakes. Motor control uses three signals (pulse/direction/enable) and steel gears reduce backlash to <5 arcmin. The robot is flexible and can also be paired with multiple options such as three kinds of grippers, a 24V IO module, a cube feeder with optical sensors and external sensors.
Educators can now afford to provide a low student-to-equipment ratio so each student can spend more time directly working with the robots. This interactive learning approach not only increases knowledge retention in areas such as mechatronics and programming but also provides a comprehensive view of robotic systems. This prepares students of all levels for real-world application environments while sparking their interest in the field.
Astorino was designed to be cost-effective for learning institutions by minimizing operational, maintenance and recurring costs. The development environment includes dedicated firmware, free software and a free code editor. By eliminating recurring costs such as software licenses and replacement parts (since the students can print 3D parts), educators have a clear idea of costs and can focus on teaching rather than budgeting.
Training Resources Prepare Instructors to Effectively Teach Robotics
Kawasaki Robotics’ long-established training department has extensive expertise in field service and a wide range of industrial robotic systems and applications. Courses range from a basic introduction to each robot, including programming and operations, to fully detailed repair and maintenance programs. Kawasaki Robotics is developing similar course materials as well as a Train-the-Trainer course for the Astorino.
“Not only do we provide state-of-art robots, tools and training to our customers, but Astorino is further proof of our commitment to helping prepare the next-generation of technicians, operators and engineers,” Marcovecchio said. “With Astorino and our extensive training resources, like-minded educators can take their teaching to a higher, more interactive level as they prepare the next generation of workers.”
The Astorino educational robotics platform can be experienced in Kawasaki Robotics’ booth – 121415 - in the IMTS Smartforce Student Summit. More details are also available at https://www.
Contact Details
Related Glossary Terms
- backlash
backlash
Reaction in dynamic motion systems where potential energy that was created while the object was in motion is released when the object stops. Release of this potential energy or inertia causes the device to quickly snap backward relative to the last direction of motion. Backlash can cause a system’s final resting position to be different from what was intended and from where the control system intended to stop the device.
- industrial robot
industrial robot
Robot designed for industrial use. Primarily used as a material-handling device but also used for changing tools, assembling parts, and manipulating special tools and measuring devices. Depending on design, an industrial robot can be programmed to perform a task by means of a controller, or it can be “walked” through the required movements by utilizing a digitizing system that translates movements into commands that the robot can be “taught.” See robot; teaching pendant.
- payload ( workload)
payload ( workload)
Maximum load that the robot can handle safely.
- robotics
robotics
Discipline involving self-actuating and self-operating devices. Robots frequently imitate human capabilities, including the ability to manipulate physical objects while evaluating and reacting appropriately to various stimuli. See industrial robot; robot.