Contact Details
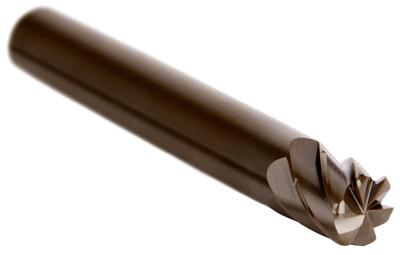
Perhaps the most basic assumption in machining is that cutting high-strength materials takes higher-strength tools. Proprietary nickel-based alloys used in gas and steam turbines, for example, are among the world's strongest materials, continually being developed to allow power plants to run at much higher temperatures. This not only provides more power to those that need it, it increases plant efficiency and reduces or eliminates harmful emissions. Superalloys, such as Inconel, Waspaloy, Rene and others come into play in turbine blades and other parts that require high strength, excellent high temperature creep resistance, phase stability, and resistance to oxidation and corrosion.
But machining such materials can be a slow, laborious, and cost-intensive experience. In general, solid carbide tooling commonly runs at speeds between 65 and 200 SFM (20 to 60 m/min) in such materials with limited tool life. New Beyond KYS40-grade solid ceramic endmills from Kennametal, however, are presenting orders-of-magnitude improvements in machining high-strength nickel-based alloys, roughing at cutting speeds up to 3,300 SFM (1000 m/min) with tool life two to three times longer than comparable solid-carbide tools.
Cutting tools made of ceramics, mainly aluminum oxide have existed since the early 20th Century. Patents on ceramic cutting tools were issued in Germany in 1913 and were commercially available in the US in the 1950s. Ceramic indexable inserts have their place today because they can operate at higher speeds in selected applications, but solid ceramic end mills were rarely seen because such tools were more brittle than carbide and did not perform well. In fact, many turbine manufacturers have taken to producing their own solid carbide end mills in house due to the high consumption of these tools.
Kennametal's new SiAlON KYS40 ceramic grade and the overall design of the solid ceramic endmill now offers the most effective way to rough nickel-based high-temperature alloys. "Cutting speeds on nickel-based superalloys can be up to 20 times higher compared to solid carbide end mills, and due to ceramic's outstanding heat resistance and stronger cutting edges (negative rake), tool life can last five times longer or more," says Thilo Mueller, global product manager at Kennametal.
Two types of KYS40 solid ceramic end mills are available, a six-fluted version for face milling and profiling; and a four-fluted, necked version for slot milling and pocketing. Both product lines allow ramping, helical interpolation, and trochoidal machining strategies as well.
The wear mechanisms and wear indication on the solid ceramic end mills is completely different from carbide, allowing running ceramic end mills far beyond the point where carbide tooling would need to be replaced. That's also the reason that this new KYS40 grade end mill is a throw-away type of tooling to allow usage beyond regular type of wear.
Whether powered by fossil fuels, hydro, or nuclear power, almost all electrical power on earth is generated by a turbine of some type. Producing, managing, and maintaining these critical components are vital to keeping the power flowing.
This puts a lot of pressure on manufacturers to continually update their machining strategies. Many factors affect this: are large numbers of similar blades required or small volumes of different blade designs? Are multiple setups and machining centers involved or single multi-axis multitasking machines? What is the CAD/CAM system being used and what is the expertise of the operators?
And, of course, what are the best tooling choices for the machining operations? Recent test results involving the new KYS40 solid ceramic end mill are insightful.
First of all, the KYS40 Beyond grade ceramic in both the four-flute and six-flute versions features an enlarged core design that improves tool rigidity and reduces deflection at high cutting speeds. Optimized end geometry and a 40-degree helix angle increase shearing action and chip evacuation.
In roughing the profile of a small turbine blade made of Inconel 718, machined dry, the EADE four-flute end mill was run at 645 m/min (2116 SFM), fed at 0.03mm/z (0.0012 IPT). Depth of cut was 0.5mm (0.0197 inches) and width of cut was 11.4mm (0.866 inches). Compared to a conventional solution, the EADE four-flute mill lasted three times longer doing the roughing in less time. This application resulted in three times more parts being produced per mill.
The six-flute EADE solid ceramic end mill was tested profiling a blisk (blade integrated disk) made of Inconel 718 and run with compressed air for chip evacuation. Unlike conventional carbide tooling, roughing to near net shape creates chips closer to dust than traditional curled chips, requiring only compressed air to blow them out of the cut. Test conditions were cutting speed of 679 m/min (2228 SFM), feed of 0.03mm/z (0.0012 IPT), and the depth of cut varied up to 0.5mm (0.0197 inches).
The results were two blisk segments machined with one tool at a 12-minute machining time per segment, which test personnel deemed "unprecedented."
The new EADE solid ceramic end mills are also featured in the new, easy-to-use "Kennametal Innovations" iPad app, free to download from the iTunes App Store. The app's simple navigation makes it easy to search via keywords to find specific tooling solutions and product groups.
Among the key features:
Product animations provide clear visual representations of processes with direct links to detailed information.
A navigation map offers drop-down menus with supplemental information, including expandable and customizable, charts and graphs.
User-driven navigation with selectable data provides quick, convenient comparisons to complimenting and competitive products.
Demonstrations and application videos provide valuable, real-world experience of the tooling technologies in actual use.
Kennametal is offering the new KYS40 ceramic end mills in the range of 3/16 to ½ inch (4 to 12mm). Running the tool does not require use of special clamping, the use of common high performance collet, power, or hydraulic chucks is fully sufficient, although the chuck must be able to run at the high speeds necessary for superalloy machining. To ensure highest tool life, final balancing is recommended.
Related Glossary Terms
- alloys
alloys
Substances having metallic properties and being composed of two or more chemical elements of which at least one is a metal.
- aluminum oxide
aluminum oxide
Aluminum oxide, also known as corundum, is used in grinding wheels. The chemical formula is Al2O3. Aluminum oxide is the base for ceramics, which are used in cutting tools for high-speed machining with light chip removal. Aluminum oxide is widely used as coating material applied to carbide substrates by chemical vapor deposition. Coated carbide inserts with Al2O3 layers withstand high cutting speeds, as well as abrasive and crater wear.
- centers
centers
Cone-shaped pins that support a workpiece by one or two ends during machining. The centers fit into holes drilled in the workpiece ends. Centers that turn with the workpiece are called “live” centers; those that do not are called “dead” centers.
- ceramics
ceramics
Cutting tool materials based on aluminum oxide and silicon nitride. Ceramic tools can withstand higher cutting speeds than cemented carbide tools when machining hardened steels, cast irons and high-temperature alloys.
- chuck
chuck
Workholding device that affixes to a mill, lathe or drill-press spindle. It holds a tool or workpiece by one end, allowing it to be rotated. May also be fitted to the machine table to hold a workpiece. Two or more adjustable jaws actually hold the tool or part. May be actuated manually, pneumatically, hydraulically or electrically. See collet.
- collet
collet
Flexible-sided device that secures a tool or workpiece. Similar in function to a chuck, but can accommodate only a narrow size range. Typically provides greater gripping force and precision than a chuck. See chuck.
- cutting speed
cutting speed
Tangential velocity on the surface of the tool or workpiece at the cutting interface. The formula for cutting speed (sfm) is tool diameter 5 0.26 5 spindle speed (rpm). The formula for feed per tooth (fpt) is table feed (ipm)/number of flutes/spindle speed (rpm). The formula for spindle speed (rpm) is cutting speed (sfm) 5 3.82/tool diameter. The formula for table feed (ipm) is feed per tooth (ftp) 5 number of tool flutes 5 spindle speed (rpm).
- depth of cut
depth of cut
Distance between the bottom of the cut and the uncut surface of the workpiece, measured in a direction at right angles to the machined surface of the workpiece.
- endmill
endmill
Milling cutter held by its shank that cuts on its periphery and, if so configured, on its free end. Takes a variety of shapes (single- and double-end, roughing, ballnose and cup-end) and sizes (stub, medium, long and extra-long). Also comes with differing numbers of flutes.
- feed
feed
Rate of change of position of the tool as a whole, relative to the workpiece while cutting.
- gang cutting ( milling)
gang cutting ( milling)
Machining with several cutters mounted on a single arbor, generally for simultaneous cutting.
- helix angle
helix angle
Angle that the tool’s leading edge makes with the plane of its centerline.
- interpolation
interpolation
Process of generating a sufficient number of positioning commands for the servomotors driving the machine tool so the path of the tool closely approximates the ideal path. See CNC, computer numerical control; NC, numerical control.
- milling
milling
Machining operation in which metal or other material is removed by applying power to a rotating cutter. In vertical milling, the cutting tool is mounted vertically on the spindle. In horizontal milling, the cutting tool is mounted horizontally, either directly on the spindle or on an arbor. Horizontal milling is further broken down into conventional milling, where the cutter rotates opposite the direction of feed, or “up” into the workpiece; and climb milling, where the cutter rotates in the direction of feed, or “down” into the workpiece. Milling operations include plane or surface milling, endmilling, facemilling, angle milling, form milling and profiling.
- milling machine ( mill)
milling machine ( mill)
Runs endmills and arbor-mounted milling cutters. Features include a head with a spindle that drives the cutters; a column, knee and table that provide motion in the three Cartesian axes; and a base that supports the components and houses the cutting-fluid pump and reservoir. The work is mounted on the table and fed into the rotating cutter or endmill to accomplish the milling steps; vertical milling machines also feed endmills into the work by means of a spindle-mounted quill. Models range from small manual machines to big bed-type and duplex mills. All take one of three basic forms: vertical, horizontal or convertible horizontal/vertical. Vertical machines may be knee-type (the table is mounted on a knee that can be elevated) or bed-type (the table is securely supported and only moves horizontally). In general, horizontal machines are bigger and more powerful, while vertical machines are lighter but more versatile and easier to set up and operate.
- profiling
profiling
Machining vertical edges of workpieces having irregular contours; normally performed with an endmill in a vertical spindle on a milling machine or with a profiler, following a pattern. See mill, milling machine.
- superalloys
superalloys
Tough, difficult-to-machine alloys; includes Hastelloy, Inconel and Monel. Many are nickel-base metals.
- width of cut
width of cut
Width of the milled surface, reflecting a face milling cutter’s radial engagement, and a peripheral milling cutter’s axial engagement, in the cut.