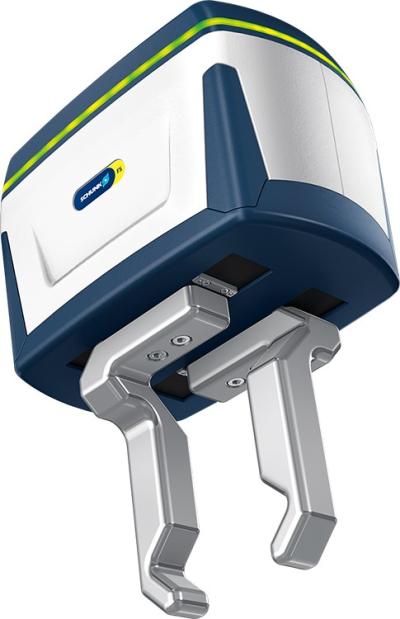
The SCHUNK Co-act EGL-C long-stroke gripper is a milestone on the way to a comprehensive human/robot collaboration: The long-stroke gripper developed for collaborative operation achieves high gripping forces up to 450 N, and combines them with a long stroke of 42.5 mm per finger. The intelligent 24 V powerhouse is suitable for handling workpiece weights of up to 2.25 kg and can be flexibly used in a wide range of applications. A further benefit: Until the planned market launch end of 2019, all the components will be DGUV-certified for HRC applications.
The gripping force of the DGUV-certified SCHUNK grippers acting on each gripper finger was previously limited to 140 N, the company now offers a new league of components with the Co-act EGL-C, and, for the first time, opens up the potential in the human/robot collaboration for handling weights beyond the small parts assembly. In this way, SCHUNK is particularly focused on the automotive-related supply industry, and also on carmakers, who are intensively working on relevant HRC scenarios.
SCHUNK Co-act team specialists are also focusing on other industries such as machine building, where the powerful grippers may be able to achieve rapid success in HRC applications. Such grippers are currently missing on the market. Their implementation has not been possible so far, since safe actuators for a load range up to 2.25 kg are currently missing on the market.
To meet the biomechanical limit values that are defined in the ISO/TS 15066 standard despite the high gripping force, the SCHUNK Co-act EGL-C gripper is equipped with a combined force-/ path measurement. Force measuring jaws and an incremental encoder are integrated in the base jaws, and permanently control the individual gripping forces and the position of the gripper fingers.
The gripping procedure is stored in the gripper, and is divided into several phases: Up to a theoretically taught distance of 4 mm to the workpiece - corresponding to far less than the thickness of a finger – the gripping force is limited to 30 N. If a collision should happen in this approach phase, e. g. due to the operator’s hand, the gripper immediately goes to the safety-monitored stop, without the risk of causing an injury. In the second phase, at a workpiece distance of < 4 mm, the fingers are closing at a freely definable maximum force of up to 450 N. If the system measures a compliance issue in the closing phase - this could happen if a gripped workpiece is too small and the operator wants to remove it manually - this movement is also automatically stopped. The same applies if the expected workpiece dimensions are exceeded by 2 mm, as e.g. no component is available.
In the third and final phase the gripper detects if the component is safely gripped and activates the integrated gripping force maintenance by applying the brake. This ensures that the gripped component does not get lost even in the event of an emergency stop. Additionally, referencing is not required in case of a power failure.
The powerful long-stroke gripper from the SCHUNK Co-act series comes completely preassembled and is available with matching interfaces for HRC robots such as KUKA, YASKAWA, FANUC, Universal Robots and NACHI. Therefore, a simple and fast commissioning by Plug & Work is possible. A commissioning assistant simplifies programming during commissioning, and a diagnostic interface allows the access to the main process and status data during the ongoing operation. The gripper is equipped with a LED light in traffic light colors that signals the current condition of the module, ensuring a smooth and intuitive collaboration with the operator.
The intelligent SCHUNK Co-act EGL-C can optionally be controlled and adjusted via PROFINET, EtherCAT, EtherNet/IP, Modbus/TCP or TCP/IP. The complete control and power electronics is installed in the housing in an efficient space-saving way, allowing a decentral but also mobile use due to its 24 V DC operating voltage. Stable guides as well as a brushless servomotor ensure a high robustness, and a permanent, reliable operation for minimal maintenance effort. The gripper will be available by the end of the year 2019.