Contact Details
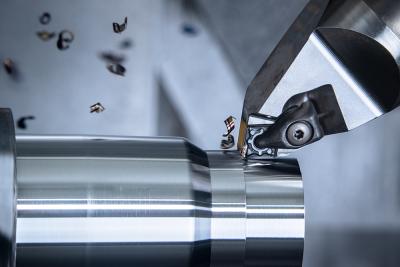
With common steel turning operations in mind, CERATIZIT has introduced three new standard coated-carbide ISO-P steel insert grades that provide up to 20% longer tool life when compared to previous generation grades. The new inserts are highly engineered for increased productivity and feature advanced substrates, geometries and CERATIZIT’s innovative Dragonskin multi-layer coating for lower heat and less tool wear.
To prevent insert waste and easily detect wear, the gold-colored TiN outer layer of the Dragonskin multilayer CVD Ti(C,N)/Al2O3/TiN coating acts as an indicator. It not only enables users to clearly identify insert wear and index before a breakage, but also prevents sharp cutting edges from going unused and the insert being inadvertently discarded. Plus, a mechanical post-coating treatment produces beneficial residual stress in the coating that results in increased process security, especially important in the large-volume production situations typically associated with turning ISO-P steels.
Each of the three grades are engineered for optimizing specific production scenarios. The CTCP115-P (ISO P15) grade has enhanced resistance to high temperatures and is ideal for use at higher cutting speeds in smooth, continuous cuts in stable cutting conditions. The CTCP125-P (ISO P25) universal steel-cutting grade balances toughness and wear resistance to provide consistent reliability in turning operations ranging from finishing to rough machining, while the CTC135-P (ISO P35) is a tough carbide grade for lower cutting speeds, interrupted cuts and unstable machining conditions.
A new UP2Date product brochure from CERATIZIT provides additional details about the new grades as well as information about a variety of other productivity-boosting metalcutting tooling and accessories. Contact CERATIZIT for more information and connect with a sales engineer for a free test cut of the ISO-P turning inserts.
Related Glossary Terms
- chemical vapor deposition ( CVD)
chemical vapor deposition ( CVD)
High-temperature (1,000° C or higher), atmosphere-controlled process in which a chemical reaction is induced for the purpose of depositing a coating 2µm to 12µm thick on a tool’s surface. See coated tools; PVD, physical vapor deposition.
- metalcutting ( material cutting)
metalcutting ( material cutting)
Any machining process used to part metal or other material or give a workpiece a new configuration. Conventionally applies to machining operations in which a cutting tool mechanically removes material in the form of chips; applies to any process in which metal or material is removed to create new shapes. See metalforming.
- residual stress
residual stress
Stress present in a body that is free of external forces or thermal gradients.
- titanium nitride ( TiN)
titanium nitride ( TiN)
Added to titanium-carbide tooling to permit machining of hard metals at high speeds. Also used as a tool coating. See coated tools.
- turning
turning
Workpiece is held in a chuck, mounted on a face plate or secured between centers and rotated while a cutting tool, normally a single-point tool, is fed into it along its periphery or across its end or face. Takes the form of straight turning (cutting along the periphery of the workpiece); taper turning (creating a taper); step turning (turning different-size diameters on the same work); chamfering (beveling an edge or shoulder); facing (cutting on an end); turning threads (usually external but can be internal); roughing (high-volume metal removal); and finishing (final light cuts). Performed on lathes, turning centers, chucking machines, automatic screw machines and similar machines.
- wear resistance
wear resistance
Ability of the tool to withstand stresses that cause it to wear during cutting; an attribute linked to alloy composition, base material, thermal conditions, type of tooling and operation and other variables.