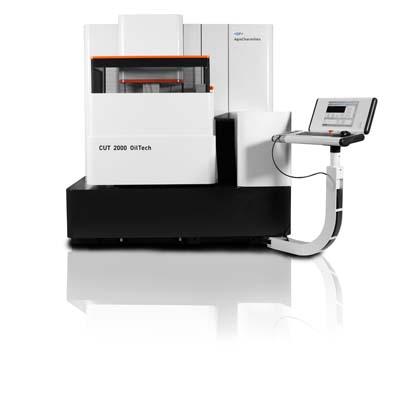
The new CUT 2000 OilTech wire EDM from GF AgieCharmilles protects workpiece surfaces by allowing manufacturers to use oil as a dielectric fluid in the machining of tungsten carbide tools for powder metallurgy, progressive dies for magnetic lamination of electric motors and transformers, high-speed stamping tools for mass-produced communication technology components, luxury watch parts and much more.
While current generators can limit electro-chemical corrosion of the cutting edge during water-based machining, it's impossible to avoid the loss of cobalt through natural dilution in water. By machining in dielectric oil, manufacturers can immerse their workpieces for long periods of time without having to worry about the effects of corrosion. The oil also enables smaller gap distances between the wire and workpiece to produce smaller internal radii when compared to water-based machining.
The CUT 2000 OilTech is equipped with a "V" series IPG-VO generator with modern design and technology to deliver finer spark gaps for better part geometry and surface finish. As standard, the machine employs wire sizes that range from 0.004" to 0.013" in diameter, enabling it to achieve surface finishes down to 0.05µm Ra in continuous operation and impeccable corner quality.
The machine can also be equipped with an optional Automatic Wire Changer, a unique wire circuit that allows manufacturers to automatically machine with two wire types or diameters for the highest possible efficiency and economy. Furthermore, an exclusive 3D setup system with a touch probe on the Z-axis detects the position of the workpiece and, when not properly aligned, the machine's Vision 5 control automatically adjusts the wire perpendicular to the surface of the workpiece.
CUT 2000 OilTech accommodates submerged workpieces up to 440 lbs. and has X-, Y and Z-axis travels of 13.77" x 9.84" x 10", respectively, and a U-, V-axis travel of +/-2.7"
Contact Details
Related Glossary Terms
- electrical-discharge machining ( EDM)
electrical-discharge machining ( EDM)
Process that vaporizes conductive materials by controlled application of pulsed electrical current that flows between a workpiece and electrode (tool) in a dielectric fluid. Permits machining shapes to tight accuracies without the internal stresses conventional machining often generates. Useful in diemaking.
- lapping compound( powder)
lapping compound( powder)
Light, abrasive material used for finishing a surface.
- powder metallurgy
powder metallurgy
Processes in which metallic particles are fused under various combinations of heat and pressure to create solid metals.
- tungsten carbide ( WC)
tungsten carbide ( WC)
Intermetallic compound consisting of equal parts, by atomic weight, of tungsten and carbon. Sometimes tungsten carbide is used in reference to the cemented tungsten carbide material with cobalt added and/or with titanium carbide or tantalum carbide added. Thus, the tungsten carbide may be used to refer to pure tungsten carbide as well as co-bonded tungsten carbide, which may or may not contain added titanium carbide and/or tantalum carbide.
- wire EDM
wire EDM
Process similar to ram electrical-discharge machining except a small-diameter copper or brass wire is used as a traveling electrode. Usually used in conjunction with a CNC and only works when a part is to be cut completely through. A common analogy is wire electrical-discharge machining is like an ultraprecise, electrical, contour-sawing operation.