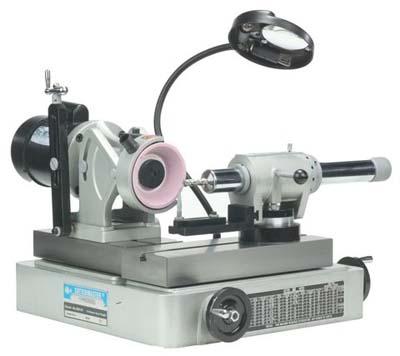
Eliminate regrind bills and save money, reduce your tool crib inventory and save more money with tool resharpener from Conquest Industries. Razor sharp cutting tools give you peak performance at all times. Perform gashing and sharpen your cutting tools the way you want with special clearance angles. Keep your machining centers running sharper tools so you can run continuously at optimum speeds and experience less down time that is draining your cash flow.
One machine does it all: spiral router bits, end mills, roughing end mills, radius end mills, milling cutters, carbide tools, and countersinks, engraving tools, lathe and form tools including reamers.
Accessories are available such as pneumatic fingers to cut sharpening time in half automatically adjusting clearance angles. A universal grinding fixture is available for gashing, to grind spade drills and can quickly adjust point clearance including radius lip grinding. Most everything with indexing or reliefs can be ground sharper whether left hand or right handed. Taper attachments are available for taper reamer and other taper applications. The Work Holding Fixture has 4 quadrants ideal for form or flat tools having compound angles.
The CUTTERMASTER Motor or Grinding wheel tilts to +35 to -8 degrees. The X-Axis has a hardened and ground lead screw with dovetail ways and has adjustable gibs traveling to 6-inches in 0.001-inch graduations. The Y-Axis has the same construction traveling to 9-Inches in 0.001-inch graduation. Flute length capacity using 5C collets using 1-¼" shank diameter and under is to 10.5 inches. Flute length capacity using end mill holder with 1-¼, 1-½ or 2 inch shanks is 8-inches. The Z-Axis vertical lift is 3-¾ inches with 180 degree motor swivel and has eight working axes for sharpening roughing end mills, chip breakers, fluting and gashing in minutes.
This Made in America CUTTERMASTER TOOL and END MILL SHARPENER is available with a LEESON 1⁄3 HP, 110 Volt (2.2 AMP, 3450 RPM) or 220 Volt (2.4 AMP, 2850 RPM) Motor retailing for $3360.
Contact Details
Related Glossary Terms
- centers
centers
Cone-shaped pins that support a workpiece by one or two ends during machining. The centers fit into holes drilled in the workpiece ends. Centers that turn with the workpiece are called “live” centers; those that do not are called “dead” centers.
- clearance
clearance
Space provided behind a tool’s land or relief to prevent rubbing and subsequent premature deterioration of the tool. See land; relief.
- fixture
fixture
Device, often made in-house, that holds a specific workpiece. See jig; modular fixturing.
- flat ( screw flat)
flat ( screw flat)
Flat surface machined into the shank of a cutting tool for enhanced holding of the tool.
- fluting
fluting
Cutting straight or spiral grooves in drills, endmills, reamers and taps to improve cutting action and remove chips.
- gang cutting ( milling)
gang cutting ( milling)
Machining with several cutters mounted on a single arbor, generally for simultaneous cutting.
- grinding
grinding
Machining operation in which material is removed from the workpiece by a powered abrasive wheel, stone, belt, paste, sheet, compound, slurry, etc. Takes various forms: surface grinding (creates flat and/or squared surfaces); cylindrical grinding (for external cylindrical and tapered shapes, fillets, undercuts, etc.); centerless grinding; chamfering; thread and form grinding; tool and cutter grinding; offhand grinding; lapping and polishing (grinding with extremely fine grits to create ultrasmooth surfaces); honing; and disc grinding.
- grinding wheel
grinding wheel
Wheel formed from abrasive material mixed in a suitable matrix. Takes a variety of shapes but falls into two basic categories: one that cuts on its periphery, as in reciprocating grinding, and one that cuts on its side or face, as in tool and cutter grinding.
- lathe
lathe
Turning machine capable of sawing, milling, grinding, gear-cutting, drilling, reaming, boring, threading, facing, chamfering, grooving, knurling, spinning, parting, necking, taper-cutting, and cam- and eccentric-cutting, as well as step- and straight-turning. Comes in a variety of forms, ranging from manual to semiautomatic to fully automatic, with major types being engine lathes, turning and contouring lathes, turret lathes and numerical-control lathes. The engine lathe consists of a headstock and spindle, tailstock, bed, carriage (complete with apron) and cross slides. Features include gear- (speed) and feed-selector levers, toolpost, compound rest, lead screw and reversing lead screw, threading dial and rapid-traverse lever. Special lathe types include through-the-spindle, camshaft and crankshaft, brake drum and rotor, spinning and gun-barrel machines. Toolroom and bench lathes are used for precision work; the former for tool-and-die work and similar tasks, the latter for small workpieces (instruments, watches), normally without a power feed. Models are typically designated according to their “swing,” or the largest-diameter workpiece that can be rotated; bed length, or the distance between centers; and horsepower generated. See turning machine.
- milling
milling
Machining operation in which metal or other material is removed by applying power to a rotating cutter. In vertical milling, the cutting tool is mounted vertically on the spindle. In horizontal milling, the cutting tool is mounted horizontally, either directly on the spindle or on an arbor. Horizontal milling is further broken down into conventional milling, where the cutter rotates opposite the direction of feed, or “up” into the workpiece; and climb milling, where the cutter rotates in the direction of feed, or “down” into the workpiece. Milling operations include plane or surface milling, endmilling, facemilling, angle milling, form milling and profiling.
- milling machine ( mill)
milling machine ( mill)
Runs endmills and arbor-mounted milling cutters. Features include a head with a spindle that drives the cutters; a column, knee and table that provide motion in the three Cartesian axes; and a base that supports the components and houses the cutting-fluid pump and reservoir. The work is mounted on the table and fed into the rotating cutter or endmill to accomplish the milling steps; vertical milling machines also feed endmills into the work by means of a spindle-mounted quill. Models range from small manual machines to big bed-type and duplex mills. All take one of three basic forms: vertical, horizontal or convertible horizontal/vertical. Vertical machines may be knee-type (the table is mounted on a knee that can be elevated) or bed-type (the table is securely supported and only moves horizontally). In general, horizontal machines are bigger and more powerful, while vertical machines are lighter but more versatile and easier to set up and operate.
- reamer
reamer
Rotating cutting tool used to enlarge a drilled hole to size. Normally removes only a small amount of stock. The workpiece supports the multiple-edge cutting tool. Also for contouring an existing hole.
- shank
shank
Main body of a tool; the portion of a drill or similar end-held tool that fits into a collet, chuck or similar mounting device.
- taper reamer
taper reamer
Reamer designed to produce a reamed hole with a specified taper. Principles of standard reamers apply. See reamer.