Contact Details
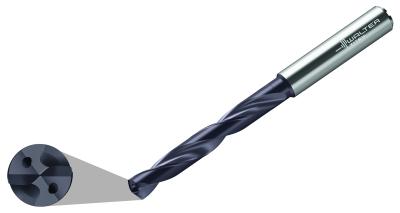
With its new X·treme Evo Plus drill, Walter is launching a new tool in the DC180 Supreme product range. Designed to boost productivity and process reliability, the solid carbide drill with internal coolant is highly effective for drilling steels, stainless steels, cast irons, non-ferrous metals, heat-resistant super alloys and hard materials (ISO P, M, K, N, S and H workpiece groups). Being a Supreme category drill, the drill is designed not just for the highest tool life, but for the highest process parameters and productivity.
Users can achieve maximum productivity with the DC180 drill due to the Krato·tec™ aluminum titanium nitride (AlTiN) multi-layer coating technology, which was specifically developed for drills and reamers. The drill features a straight cutting edge to ensure process reliability and stability. The drill has a 140°-point angle and is suitable for holemaking with emulsion, oil or minimum quantity lubrication (MQL).
When compared to competing drills, the DC180 Supreme has a tool life that is about 50% longer. An additional benefit for the DC180 drill is universal application at the highest cutting speeds. The drill is suitable for high production volume applications with a large number of holes, such as in the automotive industry. Other areas of use include the aerospace and energy industries, mold and die making, and general mechanical engineering.
The WJ30EZ-grade drill is comprised of the K30F fine-grained carbide substrate and available in diameters from 0.118 to 0.787 in. (3 to 20 mm). The DC180 Supreme in dimensions of 3 × Dc is in accordance with the DIN 6537 short standard, and the DC180 Supreme in dimensions of 5 × Dc is in accordance with the DIN 6537 long standard. Walter Xpress specials with short delivery times (maximum of three weeks) can be ordered for drilling up to 5 × Dc, as well as in step drill styles. The tool shank is in accordance with the DIN 6535 HA standard, and the shank end is in accordance with the DIN 6909 standard.
The Walter lineup of products consists of three categories of tools. Supreme tools indicate the highest level of technology and performance available. Advance tools indicate products efficiently balanced between price and performance and Perform tools are products that provide an economical solution with focused importance on price ideal for small batch production.
Related Glossary Terms
- alloys
alloys
Substances having metallic properties and being composed of two or more chemical elements of which at least one is a metal.
- cast irons
cast irons
Cast ferrous alloys containing carbon in excess of solubility in austenite that exists in the alloy at the eutectic temperature. Cast irons include gray cast iron, white cast iron, malleable cast iron and ductile, or nodular, cast iron. The word “cast” is often left out.
- coolant
coolant
Fluid that reduces temperature buildup at the tool/workpiece interface during machining. Normally takes the form of a liquid such as soluble or chemical mixtures (semisynthetic, synthetic) but can be pressurized air or other gas. Because of water’s ability to absorb great quantities of heat, it is widely used as a coolant and vehicle for various cutting compounds, with the water-to-compound ratio varying with the machining task. See cutting fluid; semisynthetic cutting fluid; soluble-oil cutting fluid; synthetic cutting fluid.
- emulsion
emulsion
Suspension of one liquid in another, such as oil in water.
- shank
shank
Main body of a tool; the portion of a drill or similar end-held tool that fits into a collet, chuck or similar mounting device.
- stainless steels
stainless steels
Stainless steels possess high strength, heat resistance, excellent workability and erosion resistance. Four general classes have been developed to cover a range of mechanical and physical properties for particular applications. The four classes are: the austenitic types of the chromium-nickel-manganese 200 series and the chromium-nickel 300 series; the martensitic types of the chromium, hardenable 400 series; the chromium, nonhardenable 400-series ferritic types; and the precipitation-hardening type of chromium-nickel alloys with additional elements that are hardenable by solution treating and aging.
- titanium nitride ( TiN)
titanium nitride ( TiN)
Added to titanium-carbide tooling to permit machining of hard metals at high speeds. Also used as a tool coating. See coated tools.
Additional Products from Walter USA LLC
Pagination
- First page
- Previous page
- …
- 17
- 18
- 19
- 20
- 21
- 22
- 23
- 24
- 25