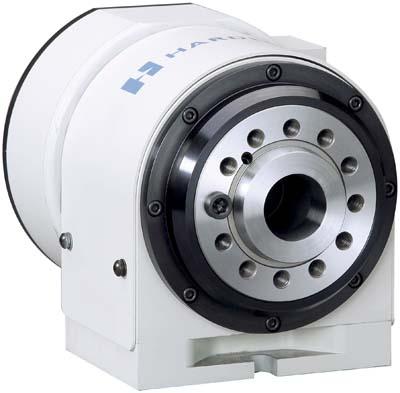
The DD100 high-speed, direct-drive Super-Precision Rotary Table manufactured by Hardinge is a high-speed parts positioner with +/1 3 arc-sec accuracy and 4 arc-sec repeatability. It's smart technology in a small footprint that can take your production to the next level. Hardinge direct-drive rotary tables are ideal for the aerospace and medical industries requiring super-precision parts. The DD100 direct-drive high-speed positioner also works well for drill and tap and laser processing.
The DD100 is capable of spindle speeds up to 4200 degrees-per-second and up to 600 rpm continuous rotation. That's over 10x faster than a gear-driven indexer, according to the company. The Hardinge A2-4 spindle nose accepts standard 5C tooling, when used with a collet closer, to provide high-precision gripping of many part shapes, sizes and materials. 5C gripping options include collets, expanding collets, step chucks for larger part diameters, jaw chucks and fixture plates. Hardinge direct-drive rotary tables have a surprisingly simple design consisting of a housing, bearings, encoder and spindle. There are far fewer parts and no gears to wear. A rare earth, permanent-magnet DC torque motor is wrapped around the spindle and operates with a programmed gear ratio of one-to-one.
The encoder is mounted directly to the spindle to provide super-precision position feedback. Direct drive technology has proven to be a more efficient way to convert electrical energy directly into mechanical motion. The cross-roller spindle bearing is permanently lubricated for life. Because the direct-drive torque motor has no mechanical gearing, there is no backlash. And since there is no backlash, bi-directional movement can be made without the need to compensate for backlash error. Hardinge systems guarantee a maximum runout of two ten-thousandths total indicator reading.
The best feature of this unit is its longevity. Years from now, your DD100 will test-out at the same accuracy and repeatability that it had when you purchased it! When compared to a standard geared system, the geared unit would need to be periodically adjusted for backlash and the oil would have to be routinely changed. Even with the adjustments and maintenance, accuracy would still be lost due to wearing of the gears.
The standard DD100 rotary package utilizes the Hardinge direct-drive all-digital servo control and can be used with most any machine. However, the unit is most productive as a true fourth-axis. In this case, the unit is directly connected to the machine, fully operating with the other axes. Hardinge's direct-drive technology complements today's machines that have faster axis travel and is compatible with "look-ahead" programming when integrated as a fourth axis to the machine. These units are ideal for large part runs on a dedicated machine producing a family of similar parts.
Contact Details
Related Glossary Terms
- backlash
backlash
Reaction in dynamic motion systems where potential energy that was created while the object was in motion is released when the object stops. Release of this potential energy or inertia causes the device to quickly snap backward relative to the last direction of motion. Backlash can cause a system’s final resting position to be different from what was intended and from where the control system intended to stop the device.
- collet
collet
Flexible-sided device that secures a tool or workpiece. Similar in function to a chuck, but can accommodate only a narrow size range. Typically provides greater gripping force and precision than a chuck. See chuck.
- fixture
fixture
Device, often made in-house, that holds a specific workpiece. See jig; modular fixturing.
- tap
tap
Cylindrical tool that cuts internal threads and has flutes to remove chips and carry tapping fluid to the point of cut. Normally used on a drill press or tapping machine but also may be operated manually. See tapping.