Contact Details
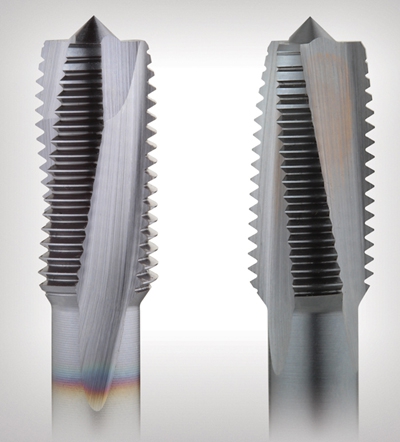
Emuge Corp. announced a comprehensive line of high-performance tools for threading demanding nickel/superalloy materials to 46 HRC. The new program includes tools ranging from taps with unique new geometry designs to reliable solid carbide thread mills designed for challenging aerospace, powergen and oil industry applications. A full line of sizes from no. 4 to ¾" are available in UNC, UNF and metric, 87 sku's in total.
Emuge's Nickel Alloy Program includes new DF-NI and C-NI taps. With Emuge's Variable Helix Correction (VHC) technology, DF-NI taps feature a specially ground relief geometry in the primary cutting zone that generates a smaller and tightly rolled chip formation for enhanced chip control to prevent damage caused by chips jamming in the tap teeth. With a 10 degree right-hand spiral flute, VHC taps are also available in STI thread sizes for jet engine components. New C-NI taps offer an advanced left-hand helical Flute form with special rake and relief to optimize chip evacuation in the forward direction and add strength to the cutting teeth for enhanced tool life and process security.
Both taps are designed with special relief geometry in the chamfer and thread section to help overcome the high hardness and extreme elastic memory of precipitation hardened nickel alloys. Taps are manufactured with premium HSS-E and are TiCN coated for exceptional heat and wear resistance. Modified bottoming chamfer (2-3 threads on VHC taps) reduces torque and increases tool life. Taps are 3BX class of fit for internal UNJ threading applications. DIN length is available for improved chip clearance in hard-to-reach applications.
Also included in the new program are Rekord KEG-NI style taps with VHC technology for tapping NPT and NPTF taper pipe threads in nickel-based super alloys. NPT and NPTF taper pipe taps come in thread sizes from 1⁄16-27 to 1"-11-½.
Mark Hatch, Emuge Corp. Product Director said, "From taps featuring our new VHC technology and new advance left-hand flute design to solid carbide thread mills, the new program offers complete solutions for today's demanding super alloy challenges."
The new Nickel Program also encompasses a number of thread mill styles. THREADS-ALL Z-GF style thread mills require only eight stock standard tool sizes to produce 100+ commonly produced screw thread designations. They provide easy machining of difficult materials, one tool for through and blind holes and total control over pitch diameter limits. Offering an exceptional balance of performance and price, SHUR-THREAD GFI-IKZ thread mills with internal coolant feature specially engineered multiple-spiral flutes to eliminate chatter, a large cutter diameter with high profile correction to ensure true-to-gauge threads and an extended milling portion which allows for 2xD length of cut.
GFI thread mills for taper pipe feature multiple flute designs with precise symmetrical spacing and constant rake angle to optimize cutting performance and thread quality, a high profile correction ratio which allows for enlarged cutting diameter to eliminate tool deflection and improved chip removal and a precision ground shank with clamping flat for a simple and secure tool holding solution.
Related Glossary Terms
- alloys
alloys
Substances having metallic properties and being composed of two or more chemical elements of which at least one is a metal.
- chatter
chatter
Condition of vibration involving the machine, workpiece and cutting tool. Once this condition arises, it is often self-sustaining until the problem is corrected. Chatter can be identified when lines or grooves appear at regular intervals in the workpiece. These lines or grooves are caused by the teeth of the cutter as they vibrate in and out of the workpiece and their spacing depends on the frequency of vibration.
- chip clearance
chip clearance
In milling, the groove or space provided in the cutter body that allows chips to be formed by the inserts.
- clearance
clearance
Space provided behind a tool’s land or relief to prevent rubbing and subsequent premature deterioration of the tool. See land; relief.
- coolant
coolant
Fluid that reduces temperature buildup at the tool/workpiece interface during machining. Normally takes the form of a liquid such as soluble or chemical mixtures (semisynthetic, synthetic) but can be pressurized air or other gas. Because of water’s ability to absorb great quantities of heat, it is widely used as a coolant and vehicle for various cutting compounds, with the water-to-compound ratio varying with the machining task. See cutting fluid; semisynthetic cutting fluid; soluble-oil cutting fluid; synthetic cutting fluid.
- flat ( screw flat)
flat ( screw flat)
Flat surface machined into the shank of a cutting tool for enhanced holding of the tool.
- flutes
flutes
Grooves and spaces in the body of a tool that permit chip removal from, and cutting-fluid application to, the point of cut.
- gang cutting ( milling)
gang cutting ( milling)
Machining with several cutters mounted on a single arbor, generally for simultaneous cutting.
- hardness
hardness
Hardness is a measure of the resistance of a material to surface indentation or abrasion. There is no absolute scale for hardness. In order to express hardness quantitatively, each type of test has its own scale, which defines hardness. Indentation hardness obtained through static methods is measured by Brinell, Rockwell, Vickers and Knoop tests. Hardness without indentation is measured by a dynamic method, known as the Scleroscope test.
- milling
milling
Machining operation in which metal or other material is removed by applying power to a rotating cutter. In vertical milling, the cutting tool is mounted vertically on the spindle. In horizontal milling, the cutting tool is mounted horizontally, either directly on the spindle or on an arbor. Horizontal milling is further broken down into conventional milling, where the cutter rotates opposite the direction of feed, or “up” into the workpiece; and climb milling, where the cutter rotates in the direction of feed, or “down” into the workpiece. Milling operations include plane or surface milling, endmilling, facemilling, angle milling, form milling and profiling.
- milling machine ( mill)
milling machine ( mill)
Runs endmills and arbor-mounted milling cutters. Features include a head with a spindle that drives the cutters; a column, knee and table that provide motion in the three Cartesian axes; and a base that supports the components and houses the cutting-fluid pump and reservoir. The work is mounted on the table and fed into the rotating cutter or endmill to accomplish the milling steps; vertical milling machines also feed endmills into the work by means of a spindle-mounted quill. Models range from small manual machines to big bed-type and duplex mills. All take one of three basic forms: vertical, horizontal or convertible horizontal/vertical. Vertical machines may be knee-type (the table is mounted on a knee that can be elevated) or bed-type (the table is securely supported and only moves horizontally). In general, horizontal machines are bigger and more powerful, while vertical machines are lighter but more versatile and easier to set up and operate.
- pitch
pitch
1. On a saw blade, the number of teeth per inch. 2. In threading, the number of threads per inch.
- rake
rake
Angle of inclination between the face of the cutting tool and the workpiece. If the face of the tool lies in a plane through the axis of the workpiece, the tool is said to have a neutral, or zero, rake. If the inclination of the tool face makes the cutting edge more acute than when the rake angle is zero, the rake is positive. If the inclination of the tool face makes the cutting edge less acute or more blunt than when the rake angle is zero, the rake is negative.
- relief
relief
Space provided behind the cutting edges to prevent rubbing. Sometimes called primary relief. Secondary relief provides additional space behind primary relief. Relief on end teeth is axial relief; relief on side teeth is peripheral relief.
- shank
shank
Main body of a tool; the portion of a drill or similar end-held tool that fits into a collet, chuck or similar mounting device.
- tap
tap
Cylindrical tool that cuts internal threads and has flutes to remove chips and carry tapping fluid to the point of cut. Normally used on a drill press or tapping machine but also may be operated manually. See tapping.
- tapping
tapping
Machining operation in which a tap, with teeth on its periphery, cuts internal threads in a predrilled hole having a smaller diameter than the tap diameter. Threads are formed by a combined rotary and axial-relative motion between tap and workpiece. See tap.
- threading
threading
Process of both external (e.g., thread milling) and internal (e.g., tapping, thread milling) cutting, turning and rolling of threads into particular material. Standardized specifications are available to determine the desired results of the threading process. Numerous thread-series designations are written for specific applications. Threading often is performed on a lathe. Specifications such as thread height are critical in determining the strength of the threads. The material used is taken into consideration in determining the expected results of any particular application for that threaded piece. In external threading, a calculated depth is required as well as a particular angle to the cut. To perform internal threading, the exact diameter to bore the hole is critical before threading. The threads are distinguished from one another by the amount of tolerance and/or allowance that is specified. See turning.
- titanium carbonitride ( TiCN)
titanium carbonitride ( TiCN)
Often used as a tool coating. See coated tools.
- wear resistance
wear resistance
Ability of the tool to withstand stresses that cause it to wear during cutting; an attribute linked to alloy composition, base material, thermal conditions, type of tooling and operation and other variables.