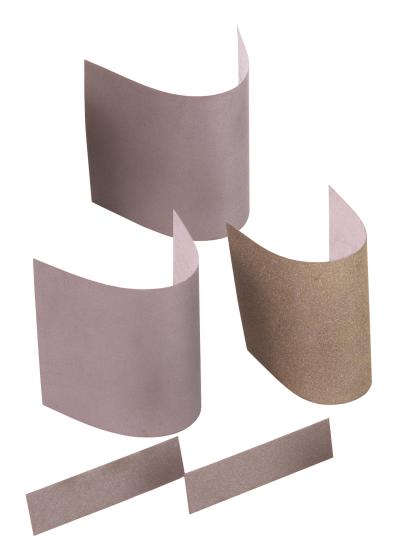
Titan Tool Supply Inc., a worldwide supplier of industrial-grade optical instrumentation and precision micro finishing tools, today announced the global market introduction of its Dia-Strip and Dia-Sheet lapping and polishing film, designed to provide cost-effective, reliable, micro finishing support for a variety of challenging lapping and deburring tasks, including the precision polishing of plastic molds, die cast dies, carbide, and ceramics.
The robust design of Titan Tool Supply’s Dia-Strip and Dia-Sheet lapping and polishing film incorporates pure virgin diamond powders in their highest concentrated forms. This slows for maximum material strength, durability, and performance. The powders are first expertly graded for uniformity, and then held into place by a thin nickel. With this approach, 90% of the grains are left exposed for cutting, yet are unable to escape the film due to the strength of the bonding agent. This unique construction makes Dia-Sheets and Dia-Strips highly durable, yet also flexible, bendable, and formable.
As a result, the film can cut virtually any material, including steel, stainless steel, carbide, ceramics, glass, plastics and wood. It is also compatible with EDM surface finishes, which otherwise are typically too hard to be touched by most abrasives.
Dia-Strip and Dia-Sheet film is offered with a choice of either 2” x 4” sheets (Dia-Sheets); or 0.5” x 2” strips (Dia-Strips), and in thicknesses ranging from 0.003” to 0.019”. It is further offered with a choice of six unique grits, ranging from coarse 80/100 (0.012” thickness), to superfine 1100 (0.003” thickness). Overall film flexibility and thickness is directly proportional to customer choice of coarseness or grain size.
Titan Tool Supply’s Dia-Strip and Dia-Sheet lapping and polishing film is also highly adaptable to a variety of specialty precision micro finishing applications. The film can be easily cut to size via the use of scissors or tin snips and is supplied with 3M double-sided industrial tape. As the film backing is completely flat, it can bond onto any material and form virtually any shape needed in order to create specialty tooling, lapping, and deburring wheels. This also makes the film particularly useful within plastic mold and cast die manufacturing applications, where the precision polishing of thin slots and slits is a typical finishing requirement, and yet where the use of traditional polishing stones would be otherwise precluded, as they are too prone to breakage.
The film is also ideal for precision micro finishing lapping and polishing requirements within space-constrained environments, as well as the lapping of curves, contours, or other complex geometries. Additional applications for Dia-Strip and Dia-Sheet film include specialty de-burring tools, diamond wheels, specially shaped diamond dressers for Aluminum Oxide or Silicon Carbide grinding wheels and stones, specialty hones, and sanding discs.
Contact Details
Related Glossary Terms
- aluminum oxide
aluminum oxide
Aluminum oxide, also known as corundum, is used in grinding wheels. The chemical formula is Al2O3. Aluminum oxide is the base for ceramics, which are used in cutting tools for high-speed machining with light chip removal. Aluminum oxide is widely used as coating material applied to carbide substrates by chemical vapor deposition. Coated carbide inserts with Al2O3 layers withstand high cutting speeds, as well as abrasive and crater wear.
- backing
backing
1. Flexible portion of a bandsaw blade. 2. Support material behind the cutting edge of a tool. 3. Base material for coated abrasives.
- ceramics
ceramics
Cutting tool materials based on aluminum oxide and silicon nitride. Ceramic tools can withstand higher cutting speeds than cemented carbide tools when machining hardened steels, cast irons and high-temperature alloys.
- electrical-discharge machining ( EDM)
electrical-discharge machining ( EDM)
Process that vaporizes conductive materials by controlled application of pulsed electrical current that flows between a workpiece and electrode (tool) in a dielectric fluid. Permits machining shapes to tight accuracies without the internal stresses conventional machining often generates. Useful in diemaking.
- flat ( screw flat)
flat ( screw flat)
Flat surface machined into the shank of a cutting tool for enhanced holding of the tool.
- grinding
grinding
Machining operation in which material is removed from the workpiece by a powered abrasive wheel, stone, belt, paste, sheet, compound, slurry, etc. Takes various forms: surface grinding (creates flat and/or squared surfaces); cylindrical grinding (for external cylindrical and tapered shapes, fillets, undercuts, etc.); centerless grinding; chamfering; thread and form grinding; tool and cutter grinding; offhand grinding; lapping and polishing (grinding with extremely fine grits to create ultrasmooth surfaces); honing; and disc grinding.
- lapping
lapping
Finishing operation in which a loose, fine-grain abrasive in a liquid medium abrades material. Extremely accurate process that corrects minor shape imperfections, refines surface finishes and produces a close fit between mating surfaces.
- polishing
polishing
Abrasive process that improves surface finish and blends contours. Abrasive particles attached to a flexible backing abrade the workpiece.
- titanium nitride ( TiN)
titanium nitride ( TiN)
Added to titanium-carbide tooling to permit machining of hard metals at high speeds. Also used as a tool coating. See coated tools.