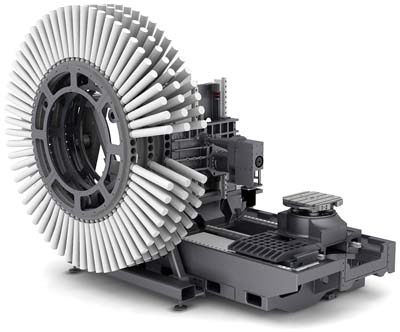
With the DMC 60 H linear, DMG/Mori Seiki are starting an impressive performance offensive in the area of fast precision centers for productive serial production up to the 5-axis simultaneous area.
High precision and continuous accuracy on the one hand, speed and dynamics on the other; adding to this extreme reliability in serial production and modular configuration levels as well as intelligent automation concepts for adaptation to individual process chains and factory processes. This reads like concrete demands from the field of complex horizontal machining. And they are all impressive features of the new DMC 60 H linear from DMG/Mori Seiki. The high level of positioning accuracy of less than 4 µm is one example, with a repeat accuracy of less than 6µm. Equally representative is the usage of linear drives for acceleration values of 1 g and extreme speeds of up to 100 m/min, which keep process times to a minimum. Furthermore, the unique concept of the tool magazine with rapid chip-to-chip times of only 2.2 seconds ensures unlimited high productivity. And while the warranty period of 60 months for the linear drives creates trust, the modular concept provides the customer with the impressive flexibility to always be able to find the right machine configuration for any manufacturing task thinkable, from the Powertrain version with direct loading capacity from the top/front to the automated 5-axis machining with integrated swivel-round table.
The field of application of the DMC 60 H linear is varied: Gearbox and coupling housings, cylinder heads or for example hydraulic blocks. However, all workpieces make high demands on accuracy and require a high degree of flexibility. With the most recent model of the DMC H series, DMG/Mori Seiki create the perfect basis for a broad range of applications, starting with the optimum utilisation of the work area: With the standard version the maximum workpiece size is 800 x 1,030mm with a weight of up to 600 kg. The travelling column concept enables traverse paths of 630, 800 and 850mm in X-, Y- and Z-direction. DMG/Mori Seiki have also considered the requirements of the users with regard to the design of the DMC 60 H linear and developed a machine with optimum ergonomics and a space requirement of just 11.9 m² for the pallet changer version.
The linear drives of the X-, Y- and Z-axes are at the centre of the machine concept. This makes rapid traverse speeds of up to 100 m/min and acceleration values of 1 g possible. A warranty period of 60 months underlines the longevity of this wear- and maintenance-free drive technology.
DMG/Mori Seiki use an oil/air lubricated model as main spindle for the standard version with 12,000 min-1. It has a capacity of 20 kW and a torque o 110 Nm. Optionally an 18,000 rpm spindle with 34 kW and 110 Nm is available. For heavy machining, DMG/MORI SEIKI provide a spindle with a powerful torque with 10,000 min-1, 46 kW and 200 Nm.
To minimize thermal deviations, DMG/Mori Seiki rely on comprehensive cooling of all relevant components, like linear drives, motor spindle and NC round table. Furthermore, all drives are outside of the work area, to avoid temperature affecting the machining. The compact rotary magazine is one of the special highlights. The basic version of the DMC 60 H linear has a magazine with 63 tools, which can be extended by four more rings with 60 additional pockets each. Apart from the slim design of 2,500mm, the extremely fast provisioning times even for a large number of tools of 3.4 up to max. 5.6 seconds and extremely short chip-to-chip times of 2.2 seconds are impressive. This innovative concept ensures that the maximum version of the machine with 303 tools just gains 1 metre in width.
A particular feature is the option to insert new tools into the magazine (from two wheels) with the tool changeover active – parallel primary time and auxiliary time tooling. Cone cleaning and broken tool detector parallel to primary processing time round off the excellent overall picture. With regard to the development of the DMC 60 H linear, DMG/Mori Seiki also have optimised chip removal within the machine. Steep and vertical covers ensure an unhindered fall through the machine bed. A spiral conveyor in the center of the machine transports the chips to the rear, so that connection to a central chip removal can be easily realised. The modular design of the DMC 60 H linear enables different configuration levels. The highest range of machining options is achieved with the 5-axis version. Here the traverse paths are 630/800/750mm, whereby the maximum workpiece size is 800 x 800mm and the workpiece weight is up to 450 kg. The swivel range of the NC round table is 220 degrees and ranges from -20 to +200 degrees. The 5-axis as well as 4-axis version of the DMC 60 H linear are optionally available for the powertrain version as version with pallet changer.
Contact Details
Related Glossary Terms
- centers
centers
Cone-shaped pins that support a workpiece by one or two ends during machining. The centers fit into holes drilled in the workpiece ends. Centers that turn with the workpiece are called “live” centers; those that do not are called “dead” centers.
- modular design ( modular construction)
modular design ( modular construction)
Manufacturing of a product in subassemblies that permits fast and simple replacement of defective assemblies and tailoring of the product for different purposes. See interchangeable parts.
- numerical control ( NC)
numerical control ( NC)
Any controlled equipment that allows an operator to program its movement by entering a series of coded numbers and symbols. See CNC, computer numerical control; DNC, direct numerical control.
- parallel
parallel
Strip or block of precision-ground stock used to elevate a workpiece, while keeping it parallel to the worktable, to prevent cutter/table contact.
- rapid traverse
rapid traverse
Movement on a CNC mill or lathe that is from point to point at full speed but, usually, without linear interpolation.