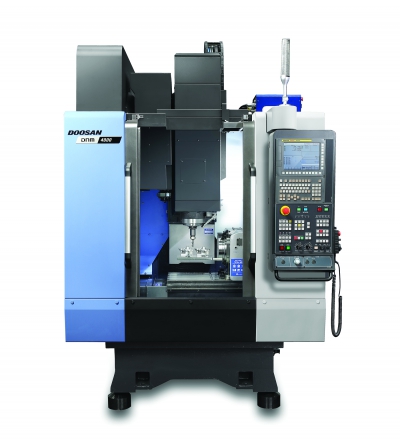
Doosan Machine Tools announces the addition of the DNM 4000 to its line of vertical machining centers. This compact VMC was designed for lean cell applications where space is tight, but productivity and cutting performance are essential.
Able to take more aggressive cuts than similarly sized 30 taper drill – tap machines, the DNM 4000 is suitable for machining small parts in tough-to machine materials for a range of industries including medical, aerospace, automotive, job shops, firearms and die and mold. Featuring a 12,000-rpm, 25-hp, 40-taper spindle with 86 ft.-lbs. of torque and a standard BIG-PLUS dual-contact interface, the DNM 4000 delivers short cycle times, fine part surface finishes and long tool life.
This vertical machining center has a compact footprint of only 65”W x 112”L x 108”H and travels of 20.5” in X, 15.7” in Y and 18.9” in Z. The two-door design reportedly incorporates the largest opening width in its class, allowing for easy operator access. The coolant system is located in the rear of the machine so the DNM can be placed mere inches from the neighboring machines.
The DNM 4000 comes with a long list of standard features. These include a 20-tool capacity magazine with a 1.3-second tool-to-tool time, standard spindle cooler, Doosan Smart Thermal Monitoring software, grease lubrication system and 230-psi through-spindle coolant. The FANUC i control with Easy Operation Package (EOP) software developed by Doosan provides numerous functions designed for convenient operation and reduced setup time.
“The DNM 4000 was purposefully developed to be small in size, but not in power,” said Andy McNamara, director of sales at Doosan Machine Tools America. “Manufacturers can now enjoy increased productivity and performance without sacrificing compactness.”
Contact Details
Related Glossary Terms
- centers
centers
Cone-shaped pins that support a workpiece by one or two ends during machining. The centers fit into holes drilled in the workpiece ends. Centers that turn with the workpiece are called “live” centers; those that do not are called “dead” centers.
- coolant
coolant
Fluid that reduces temperature buildup at the tool/workpiece interface during machining. Normally takes the form of a liquid such as soluble or chemical mixtures (semisynthetic, synthetic) but can be pressurized air or other gas. Because of water’s ability to absorb great quantities of heat, it is widely used as a coolant and vehicle for various cutting compounds, with the water-to-compound ratio varying with the machining task. See cutting fluid; semisynthetic cutting fluid; soluble-oil cutting fluid; synthetic cutting fluid.
- machining center
machining center
CNC machine tool capable of drilling, reaming, tapping, milling and boring. Normally comes with an automatic toolchanger. See automatic toolchanger.
- tap
tap
Cylindrical tool that cuts internal threads and has flutes to remove chips and carry tapping fluid to the point of cut. Normally used on a drill press or tapping machine but also may be operated manually. See tapping.