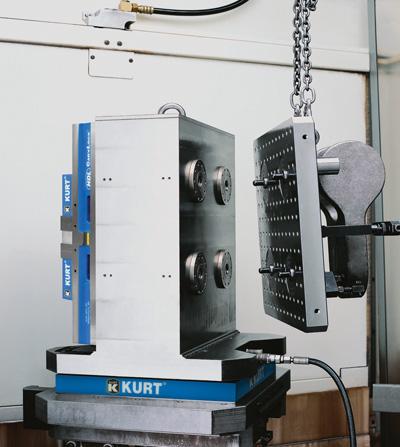
Small to large part workholding setups align and lock into position fast and accurately using Kurt Manufacturing Co.'s DockLock system. The patented DockLock system provides a fast, accurate and repeatable method for making setup changes on all types of horizontal and vertical machining centers.
Available in pneumatic and hydraulic models, DockLock models are available in sizes for light to heavy-duty applications. With repeatable mounting accuracy to +/-0.0002 inch on a typical part setup, the DockLock system ensures high quality finishes, no scrap parts and substantial setup time reduction, according to the company. A typical workholding setup change requiring 20 minutes using standard methods is done in less than 2 minutes with the DockLock from Kurt Workholding.
With DockLock, complicated machine setups are simplified. Vises and fixtures mount quickly and easily to the DockLock. It allows the user to instantly locate or remove the workholding from a machine, or move it offline or to another machine and/or back again in just seconds with zero-point accuracy every time. With robust holding force, the workholding locks into position and remains immobile. Heavy fixtures self-align with minimal operator effort. Once positioned, DockLock's patented collet retention system dampens vibration tendencies in the workholding setup, ensuring workholding rigidity during the machining process.
The standard, automatic and heavy duty hydraulic models have a retention force of 9,000 lbs., per locking cylinder (40,000 newtons). The heaviest duty models have a retention force of 20,000 lbs.
Additional DockLock features include top-down design making the fixture handling process fast and easy. With the optional air-blast system, the system is easy to keep free of chips and coolant. Also, the system's rugged design requires minimal maintenance and ensures long life through repeated use.
Contact Details
Related Glossary Terms
- centers
centers
Cone-shaped pins that support a workpiece by one or two ends during machining. The centers fit into holes drilled in the workpiece ends. Centers that turn with the workpiece are called “live” centers; those that do not are called “dead” centers.
- collet
collet
Flexible-sided device that secures a tool or workpiece. Similar in function to a chuck, but can accommodate only a narrow size range. Typically provides greater gripping force and precision than a chuck. See chuck.
- coolant
coolant
Fluid that reduces temperature buildup at the tool/workpiece interface during machining. Normally takes the form of a liquid such as soluble or chemical mixtures (semisynthetic, synthetic) but can be pressurized air or other gas. Because of water’s ability to absorb great quantities of heat, it is widely used as a coolant and vehicle for various cutting compounds, with the water-to-compound ratio varying with the machining task. See cutting fluid; semisynthetic cutting fluid; soluble-oil cutting fluid; synthetic cutting fluid.
- fixture
fixture
Device, often made in-house, that holds a specific workpiece. See jig; modular fixturing.