Contact Details
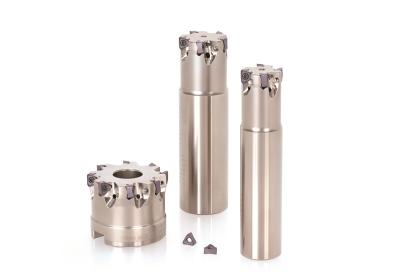
Tungaloy expands its DoForce-Tri line of square shoulder milling cutters to include a size 07 insert, with six cutting edges for precision milling and insert economy.
As machines increase their sophistication and complexity, their mechanical components are also becoming smaller and more intricate; many simple and weak structured parts are produced by near net shape molding, requiring minimum stock removal. To efficiently machine complex structures while avoiding tool-work interferences, many manufacturers resort to square shoulder milling tools. For light depth of cut applications, they prefer close-pitched cutters that ensure more than one cutting edge is always engaged in the cut for added stability and efficiency.
The DoForce-Tri 07 insert allows the insert density and feed capability to be as high as double that of the conventional, trigonal insert, while maintaining the same DOC. This is possible because of the innovative, curved cutting edge geometry on a smaller insert. This new 07 insert ensures light cutting forces while maintaining better stability than standard positive milling inserts making it perfect for machining weak workpiece setups on low rigidity machines. The insert has 6 cutting edges that include wiper edges for good surface finishes. The tool also has high wall accuracy because of the optimized insert design.
The cutter diameters are available in ranges from 18 mm to 32 mm and 0.75" to 1.25" for the cylindrical type, and 40 mm and 50 mm and 2.0" for the shell mill (bore) type.
At a Glance
Six edged double-sided insert
Close pitch cutter design with up to 2x insert density over conventional cutters
Higher cutting performance than standard positive inserts in applications ≤2 mm DOC
Provides high level of face and shoulder milling capabilities
11 metric and eight inch cutter bodies and four inserts to be added
Related Glossary Terms
- depth of cut
depth of cut
Distance between the bottom of the cut and the uncut surface of the workpiece, measured in a direction at right angles to the machined surface of the workpiece.
- feed
feed
Rate of change of position of the tool as a whole, relative to the workpiece while cutting.
- gang cutting ( milling)
gang cutting ( milling)
Machining with several cutters mounted on a single arbor, generally for simultaneous cutting.
- milling
milling
Machining operation in which metal or other material is removed by applying power to a rotating cutter. In vertical milling, the cutting tool is mounted vertically on the spindle. In horizontal milling, the cutting tool is mounted horizontally, either directly on the spindle or on an arbor. Horizontal milling is further broken down into conventional milling, where the cutter rotates opposite the direction of feed, or “up” into the workpiece; and climb milling, where the cutter rotates in the direction of feed, or “down” into the workpiece. Milling operations include plane or surface milling, endmilling, facemilling, angle milling, form milling and profiling.
- milling machine ( mill)
milling machine ( mill)
Runs endmills and arbor-mounted milling cutters. Features include a head with a spindle that drives the cutters; a column, knee and table that provide motion in the three Cartesian axes; and a base that supports the components and houses the cutting-fluid pump and reservoir. The work is mounted on the table and fed into the rotating cutter or endmill to accomplish the milling steps; vertical milling machines also feed endmills into the work by means of a spindle-mounted quill. Models range from small manual machines to big bed-type and duplex mills. All take one of three basic forms: vertical, horizontal or convertible horizontal/vertical. Vertical machines may be knee-type (the table is mounted on a knee that can be elevated) or bed-type (the table is securely supported and only moves horizontally). In general, horizontal machines are bigger and more powerful, while vertical machines are lighter but more versatile and easier to set up and operate.
- pitch
pitch
1. On a saw blade, the number of teeth per inch. 2. In threading, the number of threads per inch.
- wiper
wiper
Metal-removing edge on the face of a cutter that travels in a plane perpendicular to the axis. It is the edge that sweeps the machined surface. The flat should be as wide as the feed per revolution of the cutter. This allows any given insert to wipe the entire workpiece surface and impart a fine surface finish at a high feed rate.