Contact Details
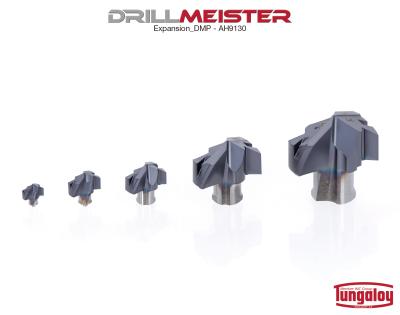
Tungaloy has further expanded its DrillMeister exchangeable head drill system by adding 30 more DMP drill heads in AH9130 grade to further improve the drill’s wear resistance for general purpose drilling applications that require hole diameters ranging from 6.0 to 25.9 mm (.236″-1.020″). This expansion is scheduled to be completed by the end of August 2021.
AH9130 is Tungaloy’s latest PVD technology specifically designed for high-performance drilling applications. With better wear resistance compared with existing first-choice grade AH725, the grade delivers extremely long tool life in drilling applications, particularly of carbon steel and alloy steel.
With increased DMP offerings in AH9130 grade, DrillMeister provides optimal solution with maximum tool life and wear prediction across all ranges of drilling applications.
The DrillMeister and DMP drill head
DrillMeister exchangeable head drills are a super productive, accurate, and cost efficient drill series. A single drill body can hold five different styles of drill heads in diameters ranging from 6.0 mm to 25.9 mm (.236″ to 1.020″). The drill heads are available in general purpose DMP style, DMC for high precision holes, DMH with enhanced drill corner geometry for drilling thin walls, DMF with flat edges ideal for counterboring, and DMN for non-ferrous applications.
The DMP style drill head features a 140 degree tip angle with a sharp cutting edge and optimized flute configuration that allows safe chip evacuation and tool stability.
Related Glossary Terms
- counterboring
counterboring
Enlarging one end of a drilled hole. The enlarged hole, which is concentric with the original hole, is flat on the bottom. Counterboring is used primarily to set bolt heads and nuts below the workpiece surface.
- flat ( screw flat)
flat ( screw flat)
Flat surface machined into the shank of a cutting tool for enhanced holding of the tool.
- physical vapor deposition ( PVD)
physical vapor deposition ( PVD)
Tool-coating process performed at low temperature (500° C), compared to chemical vapor deposition (1,000° C). Employs electric field to generate necessary heat for depositing coating on a tool’s surface. See CVD, chemical vapor deposition.
- wear resistance
wear resistance
Ability of the tool to withstand stresses that cause it to wear during cutting; an attribute linked to alloy composition, base material, thermal conditions, type of tooling and operation and other variables.