Contact Details
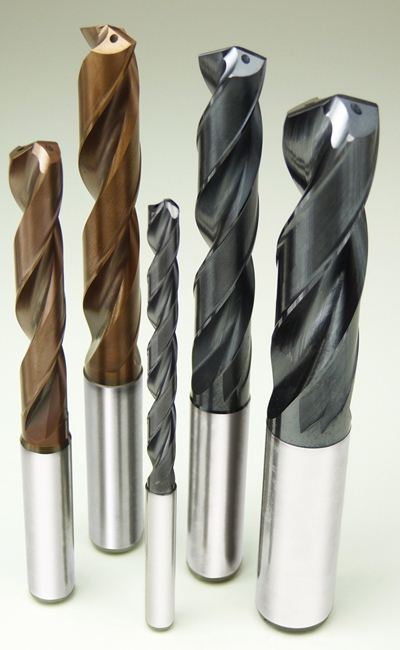
Emuge Corp. announced the North American debut of an extensive line of high performance solid-carbide drills to further enhance its broad range of taps and threading tools. The new Emuge EF series drills are the result of extensive R&D and incorporate special geometry, proprietary carbide grades and a PVD coating design that reportedly is unique to the industry. The result is three to five times faster penetration rate than conventional carbide and cobalt drills, in addition to exceptional, high quality threads and longer tool life.
"We are excited to roll out this major introduction to the U.S. and Canadian marketplace," said Bob Hellinger, president of Emuge Corp. "It makes perfect sense for Emuge to have a drill product line to complement our leading line of taps and thread mills and it provides our customers the best holemaking solutions for their tapping applications."
In addition to the drill line introduction, beginning in the fourth quarter of 2015, Emuge will be offering complete grinding/reconditioning services for all drill products at their West Boylston, Mass., facility.
The EF drills, engineered and made by Emuge in Germany, feature a double-margin flute design for added stability and rounder/straighter holes. A unique flute construction enables superb chip evaluation, and a self-centering design allows drilling in one shot, eliminating peck cycles and pre-spot operations. Emuge drills are made of a special sub-micron grain carbide grade for extraordinary abrasion resistance and durability, and a unique multi-layer PVD coating resists chipping/cracking for exceptionally long tool life.
A full range of product is available in 3XD, 5XD, and 8XD drill styles in solid & coolant-fed designs for convenience and application versatility. More than 2,000 standard SKUs will be stocked in Emuge's West Boylston facility.
Related Glossary Terms
- physical vapor deposition ( PVD)
physical vapor deposition ( PVD)
Tool-coating process performed at low temperature (500° C), compared to chemical vapor deposition (1,000° C). Employs electric field to generate necessary heat for depositing coating on a tool’s surface. See CVD, chemical vapor deposition.
- tapping
tapping
Machining operation in which a tap, with teeth on its periphery, cuts internal threads in a predrilled hole having a smaller diameter than the tap diameter. Threads are formed by a combined rotary and axial-relative motion between tap and workpiece. See tap.
- threading
threading
Process of both external (e.g., thread milling) and internal (e.g., tapping, thread milling) cutting, turning and rolling of threads into particular material. Standardized specifications are available to determine the desired results of the threading process. Numerous thread-series designations are written for specific applications. Threading often is performed on a lathe. Specifications such as thread height are critical in determining the strength of the threads. The material used is taken into consideration in determining the expected results of any particular application for that threaded piece. In external threading, a calculated depth is required as well as a particular angle to the cut. To perform internal threading, the exact diameter to bore the hole is critical before threading. The threads are distinguished from one another by the amount of tolerance and/or allowance that is specified. See turning.