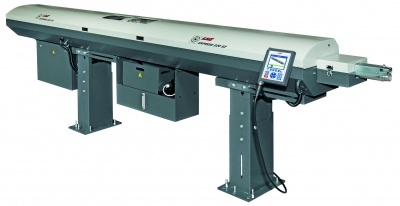
The LNS Express 220 S2 automatic, magazine bar feeder faultlessly loads 12’ long bars with diameters from 2 mm to 20 mm and, with bar preparation, up to 26 mm to accommodate 20 mm machines with 26 mm bar capacity. The enhanced bar feeder uses a simple loading assistance design for small diameter bars with a proprietary, automatic loading mechanism and bar selection system to precisely and consistently load small bars, especially in the 2 mm to 4 mm diameter range, without failure, according to the company.
Built on the proven Express 332 S2’s rigid platform, Express 220 S2 provides vibration damping, quick changeovers and a host of exclusive features that improve productivity and reduce production costs, including:
- Standard, high-capacity, 240 mm wide magazine tray and optional extended capacity magazine tray for unattended and lights-out production.
- Patented, high-speed, headstock synchronization system that meets the requirements of today’s sliding headstock machines.
- Sturdy, fully automatic, 6” hydrostatic front stabilizer that eliminates residual vibration between the bar feeder and the lathe.
- A prompting, hand-held HMI with touch screen for easier operation.
- The latest servo drive and PLC technologies.
- Ethernet readiness with a 500 parts library that reduces changeover time and material waste.
- Optional, proprietary retraction system that facilitates easier maintenance and provides the ability to perform non-guide bushing applications.
Contact Details
Related Glossary Terms
- bushing
bushing
Cylindrical sleeve, typically made from high-grade tool steel, inserted into a jig fixture to guide cutting tools. There are three main types: renewable, used in liners that in turn are installed in the jig; press-fit, installed directly in the jig for short production runs; and liner (or master), installed permanently in a jig to receive renewable bushing.
- lathe
lathe
Turning machine capable of sawing, milling, grinding, gear-cutting, drilling, reaming, boring, threading, facing, chamfering, grooving, knurling, spinning, parting, necking, taper-cutting, and cam- and eccentric-cutting, as well as step- and straight-turning. Comes in a variety of forms, ranging from manual to semiautomatic to fully automatic, with major types being engine lathes, turning and contouring lathes, turret lathes and numerical-control lathes. The engine lathe consists of a headstock and spindle, tailstock, bed, carriage (complete with apron) and cross slides. Features include gear- (speed) and feed-selector levers, toolpost, compound rest, lead screw and reversing lead screw, threading dial and rapid-traverse lever. Special lathe types include through-the-spindle, camshaft and crankshaft, brake drum and rotor, spinning and gun-barrel machines. Toolroom and bench lathes are used for precision work; the former for tool-and-die work and similar tasks, the latter for small workpieces (instruments, watches), normally without a power feed. Models are typically designated according to their “swing,” or the largest-diameter workpiece that can be rotated; bed length, or the distance between centers; and horsepower generated. See turning machine.