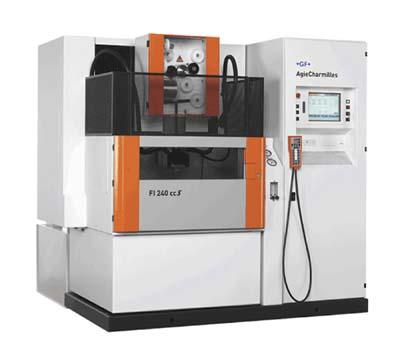
GF AgieCharmilles says its FI240CCS wire EDM combines ease of use with maximum reliability, proven performance and world-class speed. The FI240CCS is the smallest of three machines in GF AgieCharmilles' CCS series of wire EDMs and features a high XYUV feed-rate of 2 ips. The FI240CCS has a space saving compact design and a polymer granite base for thermo stability and vibration dampening. The machine is also equipped with the energy efficient FI CC digital generator. From roughing to finishing, the generator is "zero voltage" to protect parts against electrolytic effects. As a result, users benefit from dramatically improved machining speed and surface integrity, as well as exceptional clean surface quality of less than RMS 4 microinch of machined material. Additionally, the generator allows the FI240CCS to machine materials with a variety of wire diameters at a 38-in2/hr cutting speed, and impart a surface roughness of Ra 0.1 ThermoCut 2 and Integrated Collision Protection (ICP) also come standard on the FI240CCS. ThermoCut 2, a unique high-speed and maintenance-free wire threading system, boosts productivity by stretching wire and cutting it under the effect of heat, bringing the spark-to-spark time down to less than 24 seconds. Additionally, the collision protection works effectively at a high XYUV feed-rate of 2 ips, allowing the FI240CCS to cut variable work piece thicknesses like mold inserts with out any witness marks.
Contact Details
Related Glossary Terms
- cutting speed
cutting speed
Tangential velocity on the surface of the tool or workpiece at the cutting interface. The formula for cutting speed (sfm) is tool diameter 5 0.26 5 spindle speed (rpm). The formula for feed per tooth (fpt) is table feed (ipm)/number of flutes/spindle speed (rpm). The formula for spindle speed (rpm) is cutting speed (sfm) 5 3.82/tool diameter. The formula for table feed (ipm) is feed per tooth (ftp) 5 number of tool flutes 5 spindle speed (rpm).
- electrical-discharge machining ( EDM)
electrical-discharge machining ( EDM)
Process that vaporizes conductive materials by controlled application of pulsed electrical current that flows between a workpiece and electrode (tool) in a dielectric fluid. Permits machining shapes to tight accuracies without the internal stresses conventional machining often generates. Useful in diemaking.
- threading
threading
Process of both external (e.g., thread milling) and internal (e.g., tapping, thread milling) cutting, turning and rolling of threads into particular material. Standardized specifications are available to determine the desired results of the threading process. Numerous thread-series designations are written for specific applications. Threading often is performed on a lathe. Specifications such as thread height are critical in determining the strength of the threads. The material used is taken into consideration in determining the expected results of any particular application for that threaded piece. In external threading, a calculated depth is required as well as a particular angle to the cut. To perform internal threading, the exact diameter to bore the hole is critical before threading. The threads are distinguished from one another by the amount of tolerance and/or allowance that is specified. See turning.
- wire EDM
wire EDM
Process similar to ram electrical-discharge machining except a small-diameter copper or brass wire is used as a traveling electrode. Usually used in conjunction with a CNC and only works when a part is to be cut completely through. A common analogy is wire electrical-discharge machining is like an ultraprecise, electrical, contour-sawing operation.