Contact Details
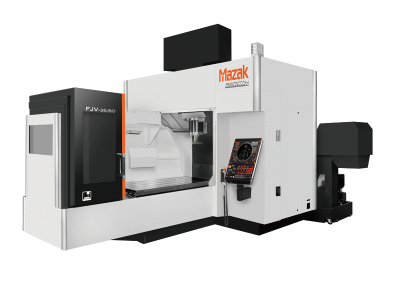
The high-speed Mazak FJV-35/80 double-column vertical machining center offers high precision over extended periods of operation with enhanced performance, Intelligent Functions and rigid machine construction. Suitable for a wide range of industries, including aerospace, construction, die and mold, and heavy machine, the versatile FJV-35/80 accommodates up to 6,614 lbs. on a 88.19" x 29.53" work table.
The special design of this vertical machining center eliminates the spindle overhang often incorporated in C-frame vertical machining centers, ensuring extremely precise machining over extended periods of operation. Furthermore, the machine's ergonomics and space-saving design ensure convenient loading/unloading of large workpieces and overall ease of operation.
Mazak can equip the FJV-35/80 with a powerful 50-taper, 50-hp, 10,000-rpm integrated spindle that generates up to 433 ft.-lbs. of torque for heavy-duty cutting of large cast iron, steel and aluminum workpieces. Options include a 7,000-rpm high-torque spindle for heavy-duty machining of steel or cast iron material, along with a high-speed 18,000-rpm, CAT 40 spindle for enhanced efficiency with aluminum and other nonferrous materials. A completely covered machining area keeps chips contained for easier cleanup and workplace safety.
Extensive X/Y/Z machine axis travels of 78.74", 31.50" and 25.98", along with rapid traverse speeds of 1,574 ipm (X and Y) and 1,181 ipm (Z), allow the FJV-35/80 to maneuver quickly around large workpieces for significantly shorter part-processing times. A 30-tool magazine helps reduce setup time while it enables redundant tooling and unattended, uninterrupted production.
The FJV-35/80’s MAZATROL SmoothG CNC control makes it easy to generate programs for processing complex parts through off-centerline machining, as well as angled drilling, milling and tapping with effortless programming in EIA/ISO or MAZATROL conversational language. The control also incorporates a wide variety of advanced programming functions for complete ease of use and high-speed, high-accuracy machining performance.
Related Glossary Terms
- centers
centers
Cone-shaped pins that support a workpiece by one or two ends during machining. The centers fit into holes drilled in the workpiece ends. Centers that turn with the workpiece are called “live” centers; those that do not are called “dead” centers.
- computer numerical control ( CNC)
computer numerical control ( CNC)
Microprocessor-based controller dedicated to a machine tool that permits the creation or modification of parts. Programmed numerical control activates the machine’s servos and spindle drives and controls the various machining operations. See DNC, direct numerical control; NC, numerical control.
- gang cutting ( milling)
gang cutting ( milling)
Machining with several cutters mounted on a single arbor, generally for simultaneous cutting.
- inches per minute ( ipm)
inches per minute ( ipm)
Value that refers to how far the workpiece or cutter advances linearly in 1 minute, defined as: ipm = ipt 5 number of effective teeth 5 rpm. Also known as the table feed or machine feed.
- machining center
machining center
CNC machine tool capable of drilling, reaming, tapping, milling and boring. Normally comes with an automatic toolchanger. See automatic toolchanger.
- milling
milling
Machining operation in which metal or other material is removed by applying power to a rotating cutter. In vertical milling, the cutting tool is mounted vertically on the spindle. In horizontal milling, the cutting tool is mounted horizontally, either directly on the spindle or on an arbor. Horizontal milling is further broken down into conventional milling, where the cutter rotates opposite the direction of feed, or “up” into the workpiece; and climb milling, where the cutter rotates in the direction of feed, or “down” into the workpiece. Milling operations include plane or surface milling, endmilling, facemilling, angle milling, form milling and profiling.
- rapid traverse
rapid traverse
Movement on a CNC mill or lathe that is from point to point at full speed but, usually, without linear interpolation.
- tapping
tapping
Machining operation in which a tap, with teeth on its periphery, cuts internal threads in a predrilled hole having a smaller diameter than the tap diameter. Threads are formed by a combined rotary and axial-relative motion between tap and workpiece. See tap.