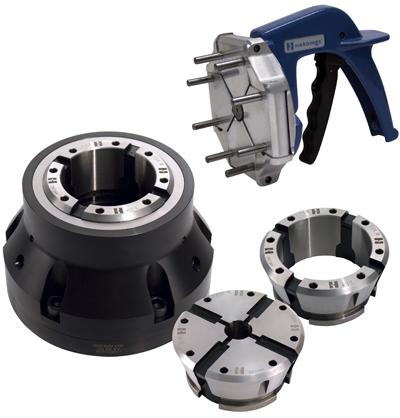
Hardinge Inc. announces the release of the 80mm FlexC vulcanized collet system. The collet chucks mount directly to the machine spindle. The 80mm vulcanized collets are inserted and removed with a manual compression wrench for collet changeover in less than ten seconds. That's 8x faster than it takes to change a collet in a standard collet chuck and 19x faster that it takes to change three jaws on a jaw chuck, according to the company.
But quick changeover is not the only benefit of this system. The FlexC collet system falls in the "special accuracy" collet classification having guaranteed accuracy within .0004" (.010mm) TIR for style A (pull-back Dead-length stationary stop) and .0008" (.020mm) TIR for style DL (push-to-close). These systems achieve the same gripping capability as conventional collets while using less draw bar force. Additionally, the all too frequent variation in bar stock will no longer be a hindrance. The collet head has a gripping range of +/-.020" (.5mm) of its nominal size to allow for variation in bar stock without having to change the collet. Because there is no collet body, the collet segments will remain parallel to the stock even when there are variations in the bar stock. This parallel clamping insures full bearing contact with the part for optimum holding power and reduced push back.
The Hardinge FlexC collet system is an ideal substitute for 3-jaw chucks because it weighs less, has a lower profile and changes over much faster. Hardinge FlexC collet systems are interchangeable with other brands on the market. Consider the FlexC collet system over other conventional collet adapters to meet special accuracy requirements, or mount it on a chuck-style lathe or rotary indexer for increased versatility. Collets are available in round and hex smooth, round and hex serrated, square smooth, emergency and S-master styles.
"The Hardinge FlexC Collet Systems are ideal for the job shop environment where machines experience multiple changeovers daily," states Michael Levanduski, Sales Manager, Hardinge Workholding. "Our test results have proven that our FlexC 80 quick-change vulcanized collet system will provide our customers with a highly durable, fully sealed, accurate gripping solution. We're happy to offer an expanded line that now accommodates 42mm, 65mm and 80mm machines."
Contact Details
Related Glossary Terms
- chuck
chuck
Workholding device that affixes to a mill, lathe or drill-press spindle. It holds a tool or workpiece by one end, allowing it to be rotated. May also be fitted to the machine table to hold a workpiece. Two or more adjustable jaws actually hold the tool or part. May be actuated manually, pneumatically, hydraulically or electrically. See collet.
- collet
collet
Flexible-sided device that secures a tool or workpiece. Similar in function to a chuck, but can accommodate only a narrow size range. Typically provides greater gripping force and precision than a chuck. See chuck.
- lathe
lathe
Turning machine capable of sawing, milling, grinding, gear-cutting, drilling, reaming, boring, threading, facing, chamfering, grooving, knurling, spinning, parting, necking, taper-cutting, and cam- and eccentric-cutting, as well as step- and straight-turning. Comes in a variety of forms, ranging from manual to semiautomatic to fully automatic, with major types being engine lathes, turning and contouring lathes, turret lathes and numerical-control lathes. The engine lathe consists of a headstock and spindle, tailstock, bed, carriage (complete with apron) and cross slides. Features include gear- (speed) and feed-selector levers, toolpost, compound rest, lead screw and reversing lead screw, threading dial and rapid-traverse lever. Special lathe types include through-the-spindle, camshaft and crankshaft, brake drum and rotor, spinning and gun-barrel machines. Toolroom and bench lathes are used for precision work; the former for tool-and-die work and similar tasks, the latter for small workpieces (instruments, watches), normally without a power feed. Models are typically designated according to their “swing,” or the largest-diameter workpiece that can be rotated; bed length, or the distance between centers; and horsepower generated. See turning machine.
- parallel
parallel
Strip or block of precision-ground stock used to elevate a workpiece, while keeping it parallel to the worktable, to prevent cutter/table contact.
- total indicator runout ( TIR)
total indicator runout ( TIR)
Combined variations of all dimensions of a workpiece, measured with an indicator, determined by rotating the part 360°.