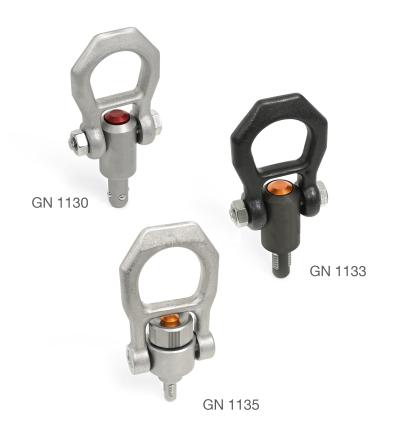
JW Winco has added self-securing threaded lifting pins to its product range for lifting, securing, and transporting equipment. Anywhere workpieces, fixtures, or system components have a threaded hole, the new threaded lifting pins can be inserted quickly for use as a lifting mechanism and removed just as easily with a push of a button. These new pins are a faster, more practical alternative to lifting eye bolts, load rings, and welded-on eyelets.
The new threaded lifting pins GN 1133 and GN 1135 function similarly to the GN 1130 lifting pins, which have been a popular JW Winco product for years. These new pins are each secured in place by four spring-loaded threaded elements (instead of balls). Pressing the spring-loaded aluminum button causes the elements to retract into the pin so that it can be inserted into a threaded hole. Once the button is released, the elements engage with the threading. This engagement allows the pins to accept significantly higher axial forces than ball lock pins. To release the pin from the component, press the button once more.
The shackle is suitable for attaching typical lifting gear such as chains or slings, and all versions can swivel 180 degrees. On JW Winco's standard part GN 1135, the shackle additionally features a rotating bearing, allowing it to accept forces in any direction without causing the pin to move within the supporting thread. Standard part GN 1135 is recognizable by the ring-shaped bearing and the ergonomically shaped pin head. All versions also feature a safety bar to prevent pressing the spring-loaded button accidentally. The threaded lifting pins are available in steel and stainless steel and come in eight thread sizes from ½ x13 to 1x8 inch and M8 to M20 metric, each in a single length between 0.472 and 0.866 inches (12 and 22 mm).
Contact Details
Related Glossary Terms
- threading
threading
Process of both external (e.g., thread milling) and internal (e.g., tapping, thread milling) cutting, turning and rolling of threads into particular material. Standardized specifications are available to determine the desired results of the threading process. Numerous thread-series designations are written for specific applications. Threading often is performed on a lathe. Specifications such as thread height are critical in determining the strength of the threads. The material used is taken into consideration in determining the expected results of any particular application for that threaded piece. In external threading, a calculated depth is required as well as a particular angle to the cut. To perform internal threading, the exact diameter to bore the hole is critical before threading. The threads are distinguished from one another by the amount of tolerance and/or allowance that is specified. See turning.