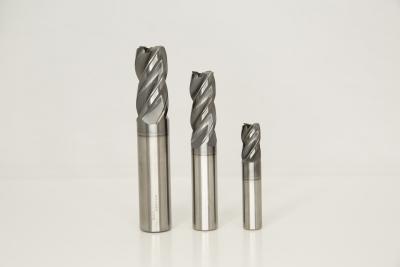
Greenleaf Corporation has announced Greenleaf-360, a new line of high-performance solid carbide end mills to complement the XSYTIN®-360 line of solid ceramic end mills. Greenleaf-360 end mills combine a proprietary flute design with a high-performance carbide substrate, which allows for fast and efficient material removal with less stress induced into the part. An excellent combination of strength, toughness, and heat resistance enables machining capabilities from roughing to finishing with extended tool life and predictability. Greenleaf-360 high-performance end mills have shown speed and feed performance 25-50% higher than the competition with extended tool life.
Greenleaf-360 end mills use a substrate that has proven capability in a wide variety of materials, from low carbon steel alloys to heat-resistant alloys. The sub-micron grade provides great toughness and wear resistance that offers customers one grade that can be applied in many different applications.
The unique PVD coating that is standard on all Greenleaf-360 end mills provides added productivity and performance. The coating offers a very low coefficient of friction with an extremely high service temperature range. This combination results in high wear resistance and allows for higher speed capabilities, especially in heat-resistant alloys.
“I am extremely excited about the introduction of Greenleaf-360 to our solid round tool offering. This high-performance carbide end mill line provides increased tool life and productivity for our customers, which ultimately leads to increased value. As a world leader in material science and tooling innovation, we worked hard to make sure that our carbide end mill introduction was one of true high performance,” says Bernie McConnell, Executive Vice President - Commercial at Greenleaf Corporation. “The high-performance carbide end mill market opens up a whole new opportunity for Greenleaf to expand our presence and market share in new and existing customers.”
Unique features and benefits of Greenleaf-360 end mills include:
-
A proprietary flute design that reduces cutting forces and provides maximum material removal
-
Full line of 4, 5, and 7 flute configurations provides solutions from full slotting to high-speed machining
-
Extended shank length options allow for effective completion of long-reach applications
-
High-performance substrate and coating combination offers versatility in machining various workpiece materials
-
Regrind capabilities to like-new condition for added cost savings and value
Ideally suited for machining materials in the aerospace, automotive, die & mold, medical, and power generation industries, Greenleaf-360 inch and metric end mills are available now.
Contact Details
Related Glossary Terms
- alloys
alloys
Substances having metallic properties and being composed of two or more chemical elements of which at least one is a metal.
- feed
feed
Rate of change of position of the tool as a whole, relative to the workpiece while cutting.
- milling machine ( mill)
milling machine ( mill)
Runs endmills and arbor-mounted milling cutters. Features include a head with a spindle that drives the cutters; a column, knee and table that provide motion in the three Cartesian axes; and a base that supports the components and houses the cutting-fluid pump and reservoir. The work is mounted on the table and fed into the rotating cutter or endmill to accomplish the milling steps; vertical milling machines also feed endmills into the work by means of a spindle-mounted quill. Models range from small manual machines to big bed-type and duplex mills. All take one of three basic forms: vertical, horizontal or convertible horizontal/vertical. Vertical machines may be knee-type (the table is mounted on a knee that can be elevated) or bed-type (the table is securely supported and only moves horizontally). In general, horizontal machines are bigger and more powerful, while vertical machines are lighter but more versatile and easier to set up and operate.
- physical vapor deposition ( PVD)
physical vapor deposition ( PVD)
Tool-coating process performed at low temperature (500° C), compared to chemical vapor deposition (1,000° C). Employs electric field to generate necessary heat for depositing coating on a tool’s surface. See CVD, chemical vapor deposition.
- shank
shank
Main body of a tool; the portion of a drill or similar end-held tool that fits into a collet, chuck or similar mounting device.
- slotting
slotting
Machining, normally milling, that creates slots, grooves and similar recesses in workpieces, including T-slots and dovetails.
- wear resistance
wear resistance
Ability of the tool to withstand stresses that cause it to wear during cutting; an attribute linked to alloy composition, base material, thermal conditions, type of tooling and operation and other variables.