Contact Details
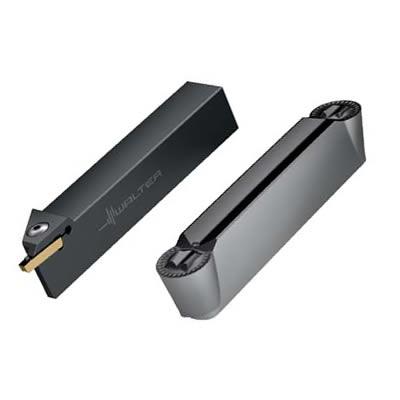
Walter USA, LLC has announced a series of enhancements to its line of grooving products. Heading the bill is the RF8 profiling insert, which features excellent chip control and a precision ground, sharp cutting edge designed for difficult to machine materials.
While this geometry is excellent for stainless steel, high temperature alloys, and steels, it is also good on all materials where a light depth of cut is required, which in turn makes chip control more challenging. It also reduces cutting forces on thin or unstable components. The RF8 undercuts up to 230 degrees processing angle and provides a very high level of surface quality.
The CF6 cutting tool insert geometry, a key part of this product line extension, also has light cutting forces and is excellent for small parts and thin wall tubes. The new 1.5mm insert, combined with the 10 degree lead angle for reduced pip and burr formation makes this a very effective system for parting off.
Walter has also announced the introduction of inch dimension grooving and groove turning inserts in the tough new Tiger-tec Silver grades WSM33S and WSM43S. The UF4 geometry for grooving and groove-turning, RD4 geometry for radius grooving and profiling, and new 1.5mm wide parting off inserts with 10 degree lead angle for reduced pip and burr formation.
Additional toolholders in the grooving system now available as part of this product line enhancement include: G1011 grooving and cutoff toolholders with ½-in. or 5⁄8-in. shanks, and 1-in. shank tools with increased depth of cut up to 1.26-in.; G1111 face grooving tool holders for face groove diameters from 1.3-in. to 19.7-in.; and G1511 and G1521 tools for snap-ring and O-ring grooves, which are capable of both radial and face grooving operations for groove depths up to 0.236-in.
Related Glossary Terms
- alloys
alloys
Substances having metallic properties and being composed of two or more chemical elements of which at least one is a metal.
- burr
burr
Stringy portions of material formed on workpiece edges during machining. Often sharp. Can be removed with hand files, abrasive wheels or belts, wire wheels, abrasive-fiber brushes, waterjet equipment or other methods.
- cutoff
cutoff
Step that prepares a slug, blank or other workpiece for machining or other processing by separating it from the original stock. Performed on lathes, chucking machines, automatic screw machines and other turning machines. Also performed on milling machines, machining centers with slitting saws and sawing machines with cold (circular) saws, hacksaws, bandsaws or abrasive cutoff saws. See saw, sawing machine; turning.
- depth of cut
depth of cut
Distance between the bottom of the cut and the uncut surface of the workpiece, measured in a direction at right angles to the machined surface of the workpiece.
- grooving
grooving
Machining grooves and shallow channels. Example: grooving ball-bearing raceways. Typically performed by tools that are capable of light cuts at high feed rates. Imparts high-quality finish.
- lead angle
lead angle
Angle between the side-cutting edge and the projected side of the tool shank or holder, which leads the cutting tool into the workpiece.
- parting
parting
When used in lathe or screw-machine operations, this process separates a completed part from chuck-held or collet-fed stock by means of a very narrow, flat-end cutting, or parting, tool.
- profiling
profiling
Machining vertical edges of workpieces having irregular contours; normally performed with an endmill in a vertical spindle on a milling machine or with a profiler, following a pattern. See mill, milling machine.
- shank
shank
Main body of a tool; the portion of a drill or similar end-held tool that fits into a collet, chuck or similar mounting device.
- turning
turning
Workpiece is held in a chuck, mounted on a face plate or secured between centers and rotated while a cutting tool, normally a single-point tool, is fed into it along its periphery or across its end or face. Takes the form of straight turning (cutting along the periphery of the workpiece); taper turning (creating a taper); step turning (turning different-size diameters on the same work); chamfering (beveling an edge or shoulder); facing (cutting on an end); turning threads (usually external but can be internal); roughing (high-volume metal removal); and finishing (final light cuts). Performed on lathes, turning centers, chucking machines, automatic screw machines and similar machines.
Additional Products from Walter USA LLC
Pagination
- First page
- Previous page
- …
- 17
- 18
- 19
- 20
- 21
- 22
- 23
- 24
- 25