Contact Details
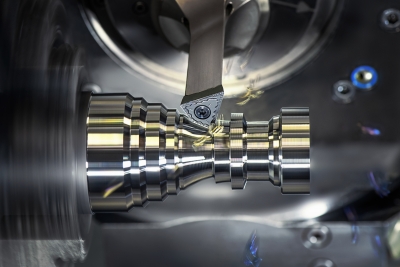
High Dynamic Turning, or HDT for short, from Ceratizit has turned conventional turning methods completely upside down. This new turning technology combined with the dynamic FreeTurn tooling, means that in the future it will be possible to carry out all traditional turning operations such as roughing, finishing, contour turning, face turning and longitudinal turning with just one tool. HDT is therefore an uncompromising method of turning.
For 100 years, new cutting materials, new chipbreakers and a few new tooling systems have been invented to optimize turning. However, the actual basic turning process has remained relatively unchanged. Even today, a contour is created with an indexable insert at a fixed angle to the workpiece. This has not changed even with the addition of controllable axes in modern turning/milling centers, machines which are intended to serve one purpose above all: to manufacture a component as completely as possible within a single machine. Ceratizit has taken advantage of the systematics of these turning/milling centers and developed the High Dynamic Turning system. The simple idea behind HDT: The tool approach and point of contact in the machine can be varied as opposed to conventional turning.
Instead of the classic, static position of the insert in the holder, the milling spindle is now used to produce the corresponding approach angle to the workpiece. The use of the spindle drive, in conjunction with the slim, axial tool design of the FreeTurn tools by Ceratizit creates a degree of freedom of 360° without the risk of collision, thus providing unprecedented flexibility. Due to the rotation around its own tool axis, the cutting-edge change can be done without interrupting the cutting process.
Additionally, the angle of approach, or lead angle, is freely variable at any time and can even be changed while cutting. This not only enables flexible machining of almost every workpiece contour, but also optimal chipbreaking, higher feed rates and an increase in tool life. Depending on the machine capabilities, the technology can be used functionally in all areas of turning operations. The approach of the milling spindle on the Y/Z axis on turning/milling centers is widespread. As a result, further possibilities can be achieved with HDT that seemed previously unachievable. For example, cutting from above and below is possible. Depending on the machining area and workpiece size, this freedom can be an important criterion.
In the future of High Dynamic Turning, the static turning tools of the past will be replaced by dynamic ones. One such dynamic tooling solution is FreeTurn by Ceratizit. The defining characteristic of FreeTurn tooling is its simple structure. The toolholder, together with its slim shank and axial concept which optimizes the direction of the cutting forces into the spindle, form a stable unit. At the front there is a multi-sided insert, which is simply screwed in place. The trick: The patent pending FreeTurn insert can consist of several cutting edges with different properties. This allows for different angle points, corner radii or chip breakers - even different coatings and cutting materials are conceivable. The tool can therefore be adapted to the machining requirements offering the advantage of replacing several tools. This in turn leads to significant savings in tool change times, tool magazine loadouts and tools themselves. One feature is making components with highly complex contours without limitation using only one FreeTurn tool. This flexibility ensures that complex component holding can be quickly and effectively adapted to the new machining situation.
With High Dynamic Turning and the FreeTurn tools, a new era in turning has arrived. In terms of efficiency, HDT exceeds the conventional turning process many times over and, as the experts from Ceratizit are convinced, will replace the classic approaches sooner rather than later. After all, the new turning technology will continue to open and reveal possibilities in the future to make turning processes faster and more precise.
Related Glossary Terms
- approach angle
approach angle
Angle between the insert’s side-cutting edge and the line perpendicular to the milling cutter’s axis of rotation. Approach angle, which is also known as cutting edge angle, is used with metric units of measurement. See lead angle.
- centers
centers
Cone-shaped pins that support a workpiece by one or two ends during machining. The centers fit into holes drilled in the workpiece ends. Centers that turn with the workpiece are called “live” centers; those that do not are called “dead” centers.
- feed
feed
Rate of change of position of the tool as a whole, relative to the workpiece while cutting.
- gang cutting ( milling)
gang cutting ( milling)
Machining with several cutters mounted on a single arbor, generally for simultaneous cutting.
- indexable insert
indexable insert
Replaceable tool that clamps into a tool body, drill, mill or other cutter body designed to accommodate inserts. Most inserts are made of cemented carbide. Often they are coated with a hard material. Other insert materials are ceramic, cermet, polycrystalline cubic boron nitride and polycrystalline diamond. The insert is used until dull, then indexed, or turned, to expose a fresh cutting edge. When the entire insert is dull, it is usually discarded. Some inserts can be resharpened.
- lead angle
lead angle
Angle between the side-cutting edge and the projected side of the tool shank or holder, which leads the cutting tool into the workpiece.
- milling
milling
Machining operation in which metal or other material is removed by applying power to a rotating cutter. In vertical milling, the cutting tool is mounted vertically on the spindle. In horizontal milling, the cutting tool is mounted horizontally, either directly on the spindle or on an arbor. Horizontal milling is further broken down into conventional milling, where the cutter rotates opposite the direction of feed, or “up” into the workpiece; and climb milling, where the cutter rotates in the direction of feed, or “down” into the workpiece. Milling operations include plane or surface milling, endmilling, facemilling, angle milling, form milling and profiling.
- shank
shank
Main body of a tool; the portion of a drill or similar end-held tool that fits into a collet, chuck or similar mounting device.
- toolholder
toolholder
Secures a cutting tool during a machining operation. Basic types include block, cartridge, chuck, collet, fixed, modular, quick-change and rotating.
- turning
turning
Workpiece is held in a chuck, mounted on a face plate or secured between centers and rotated while a cutting tool, normally a single-point tool, is fed into it along its periphery or across its end or face. Takes the form of straight turning (cutting along the periphery of the workpiece); taper turning (creating a taper); step turning (turning different-size diameters on the same work); chamfering (beveling an edge or shoulder); facing (cutting on an end); turning threads (usually external but can be internal); roughing (high-volume metal removal); and finishing (final light cuts). Performed on lathes, turning centers, chucking machines, automatic screw machines and similar machines.