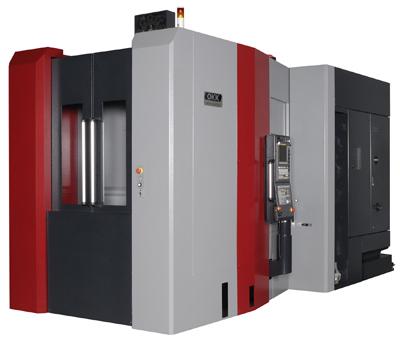
Like its HMC400, OKK's new HMC500 Horizontal Machining Center is thoroughly built for speed and faster cycle times. Featuring a 500mm pallet, the HMC500 is also designed to accommodate some of the largest workpieces in its class.
Performing 20 percent faster than OKK's HM500S, the HMC500 achieves a rapid feed rate of 63 meters per minute (2480 ipm) with acceleration of 1G (XYZ). It is constructed with a lightweight column, featuring a rigid stepped X axis rail design, and a high-speed built-in rotary table. A large bearing in the B axis of the rotary table, and a multi clamp pallet system, ensure rigidity.
The HMC500 boasts exceptionally fast automatic pallet and tool changers. Furthermore, a maximum tool length of 550mm means deep boring operations can be completed without rotating the pallet, resulting in additional time savings and improved accuracy. A high torque and rigid 15K Big Plus Spindle allows the HMC500 to reach cutting speeds of 15,000 rpm in a mere 1.7 seconds (with 50 HP), for faster machining of a variety of tough materials, including 1018 steel. This machine is 25 percent faster at rigid tapping than OKK's HM500S with the same cutting condition. The spindle design also improves tool accessibility. The distance from the spindle nose to the pallet center is 70mm.
Maintenance was also considered in the time-saving design of the HMC500. The 1000 PSI coolant through spindle unit features a 5µm bag filter, which can be easily replaced without interrupting the cycle. More than three times longer life can be achieved compared to conventional line filter systems, according to the company. What's more, virtually all maintenance controls and gauges are centrally located on the front of the machine for convenient daily inspection.
Contact Details
Related Glossary Terms
- boring
boring
Enlarging a hole that already has been drilled or cored. Generally, it is an operation of truing the previously drilled hole with a single-point, lathe-type tool. Boring is essentially internal turning, in that usually a single-point cutting tool forms the internal shape. Some tools are available with two cutting edges to balance cutting forces.
- coolant
coolant
Fluid that reduces temperature buildup at the tool/workpiece interface during machining. Normally takes the form of a liquid such as soluble or chemical mixtures (semisynthetic, synthetic) but can be pressurized air or other gas. Because of water’s ability to absorb great quantities of heat, it is widely used as a coolant and vehicle for various cutting compounds, with the water-to-compound ratio varying with the machining task. See cutting fluid; semisynthetic cutting fluid; soluble-oil cutting fluid; synthetic cutting fluid.
- feed
feed
Rate of change of position of the tool as a whole, relative to the workpiece while cutting.
- machining center
machining center
CNC machine tool capable of drilling, reaming, tapping, milling and boring. Normally comes with an automatic toolchanger. See automatic toolchanger.
- tapping
tapping
Machining operation in which a tap, with teeth on its periphery, cuts internal threads in a predrilled hole having a smaller diameter than the tap diameter. Threads are formed by a combined rotary and axial-relative motion between tap and workpiece. See tap.