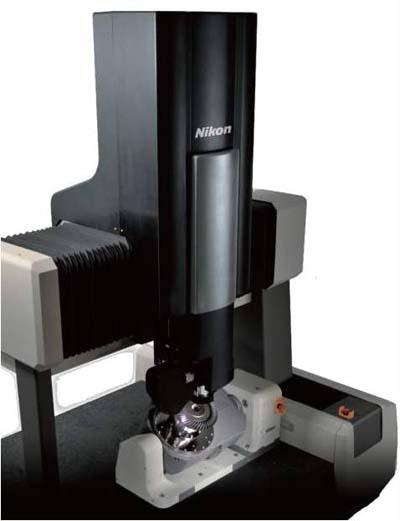
Nikon Metrology introduces the HN-6060, a next-generation non-contact inspection system providing the latest in metrology capabilities. Advanced laser scanning, 5-axis synchronized hardware control, ultra-stiff design and powerful processing software, the HN-6060 sets the standard for fast, ultra-precise inspection of complex shapes. This includes gear teeth, turbine blades, appliance housings and much more.
"The HN-6060 multi-sensor system builds upon the Nikon Metrology portfolio of vision systems and 3D solutions," says Myles Richard, Managing Director of Americas for Nikon Metrology, "It addresses the need for fast, high-accuracy 3D inspection of complex shapes by combining innovative optical technology with the highest precision measurement hardware."
The newly designed laser scanning sensor extracts the surface form and waviness data in one scan. Previously tactile gear-inspection tools needed to rely on 2D sections of data. This new advancement provides better inspection possibilities, revealing all shape and waviness information in one simple measurement.
"What the HN-6060 provides is a much easier, quicker and more precise method of 3D data capture than metrology systems have demonstrated before," says Robert Wasilesky, Senior Vice President of Sales for Nikon Metrology. "The demand for high-accuracy 3D surface metrology systems continue to increase as the automotive, aerospace and appliances industries also implement higher precision."
The metrology system's laser scanner and SFF (shape from focus) sensor use active texture projection to perform high-precision measurement of shapes even with glossy surfaces or no surface texture. Touch probes and optical heads with built-in TTL laser AF complete the multi-sensor system. This allows it to perform shape measurements of parts such as complex automotive and machined components, molded parts, and medical devices.
Another core element of the HN-6060 is its five axes synchronized hardware control. This allows optimum part orientation to the sensor and can measure the part from different angles. The system is not only designed to measure complex surfaces such as hypoid gears, worm gears and helical gears, but it also inspects turbine blades, digital camera housings, complex closures and more.
The HN-6060 software seamlessly integrates with the measurement hardware and is designed for user operability and safety. It features macro-based teach in, simulation for collision avoidance, easy acquisition of point clouds from 2D and 3D shapes, and insightful part-to-CAD comparison.
Contact Details
Related Glossary Terms
- metrology
metrology
Science of measurement; the principles on which precision machining, quality control and inspection are based. See precision machining, measurement.
- part orientation
part orientation
Designing the assembly machine, feeding mechanism and the part itself so the parts to be assembled are properly aligned prior to and during the assembly operation.
- precision machining ( precision measurement)
precision machining ( precision measurement)
Machining and measuring to exacting standards. Four basic considerations are: dimensions, or geometrical characteristics such as lengths, angles and diameters of which the sizes are numerically specified; limits, or the maximum and minimum sizes permissible for a specified dimension; tolerances, or the total permissible variations in size; and allowances, or the prescribed differences in dimensions between mating parts.
- surface texture
surface texture
Repetitive or random deviations from the nominal surface, which form 3-D topography of the surface. See flows; lay; roughness; waviness.
- waviness
waviness
The more widely spaced component of the surface texture. Includes all irregularities spaced more widely than the instrument cutoff setting. See flows; lay; roughness.