Contact Details
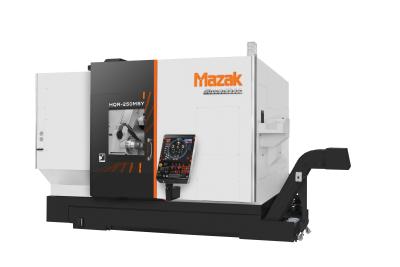
Mazak Corp.'s HQR-250MSY multitask turning center can process parts using a wide range of different tools. With its upper turret with rotary tool milling (M), second spindle (S) and Y-axis capabilities (Y), this productive machine delivers Done In One part-processing opportunities and high-volume throughput.
The twin-spindle, twin-turret configuration can easily complete machining from slug and/or bar material in a single setup. Furthermore, the balanced cutting of the upper and lower turrets promotes high part throughput. By operating together or separately, the twin opposed turning spindles allow a single part to be machined on all surfaces through a coordinated hand-off between spindles. Alternately, two different parts can be machined simultaneously on one machine. In cases where the part configuration permits, balanced machining can potentially remove up to 25% of the cycle time.
The spindles are supported by large-diameter bearings for high spindle rigidity. The main spindle features a 10" chuck, 3.58" spindle bore and 35-hp integral spindle motor that provides a maximum speed of 4,000 rpm. The second spindle has an 8" chuck, optional 3.58” spindle bore and a 35 hp integral spindle motor that offers a 4,000-rpm top speed. Both have full C-axis control for part positioning and contouring with indexing increments of 0.0001 degrees.
Both the upper and lower turrets accommodate 12 tools each and have 4" Y-axis travel capability for off-centerline operations – for additional flexibility, turrets may be expanded to 16 positions each. Rotary tool spindles on each turret deliver 6,000 rpm and 7.5 hp for milling and drilling functionality.
The machine comes equipped with the Mazatrol SmoothG CNC, which makes it easy to generate programs for processing high-production complex parts through offcenterline machining as well as angled drilling, milling and tapping. Through its Smooth Technology platform, the Mazatrol SmoothG offers several advanced programming functions, including Smooth Corner Control, which reduces vibrations and shortens machining cycle times through cutter path adjustments made when machining into corners, and Intelligent Pocket Milling, which engages a high-efficiency toolpath when milling out part cavities.
For continuous unmanned operations, the HQR-250MSY easily integrates with an optional bar feeder and unloader or robot loader/unloader.
Related Glossary Terms
- chuck
chuck
Workholding device that affixes to a mill, lathe or drill-press spindle. It holds a tool or workpiece by one end, allowing it to be rotated. May also be fitted to the machine table to hold a workpiece. Two or more adjustable jaws actually hold the tool or part. May be actuated manually, pneumatically, hydraulically or electrically. See collet.
- computer numerical control ( CNC)
computer numerical control ( CNC)
Microprocessor-based controller dedicated to a machine tool that permits the creation or modification of parts. Programmed numerical control activates the machine’s servos and spindle drives and controls the various machining operations. See DNC, direct numerical control; NC, numerical control.
- gang cutting ( milling)
gang cutting ( milling)
Machining with several cutters mounted on a single arbor, generally for simultaneous cutting.
- milling
milling
Machining operation in which metal or other material is removed by applying power to a rotating cutter. In vertical milling, the cutting tool is mounted vertically on the spindle. In horizontal milling, the cutting tool is mounted horizontally, either directly on the spindle or on an arbor. Horizontal milling is further broken down into conventional milling, where the cutter rotates opposite the direction of feed, or “up” into the workpiece; and climb milling, where the cutter rotates in the direction of feed, or “down” into the workpiece. Milling operations include plane or surface milling, endmilling, facemilling, angle milling, form milling and profiling.
- tapping
tapping
Machining operation in which a tap, with teeth on its periphery, cuts internal threads in a predrilled hole having a smaller diameter than the tap diameter. Threads are formed by a combined rotary and axial-relative motion between tap and workpiece. See tap.
- toolpath( cutter path)
toolpath( cutter path)
2-D or 3-D path generated by program code or a CAM system and followed by tool when machining a part.
- toolpath( cutter path)2
toolpath( cutter path)
2-D or 3-D path generated by program code or a CAM system and followed by tool when machining a part.
- turning
turning
Workpiece is held in a chuck, mounted on a face plate or secured between centers and rotated while a cutting tool, normally a single-point tool, is fed into it along its periphery or across its end or face. Takes the form of straight turning (cutting along the periphery of the workpiece); taper turning (creating a taper); step turning (turning different-size diameters on the same work); chamfering (beveling an edge or shoulder); facing (cutting on an end); turning threads (usually external but can be internal); roughing (high-volume metal removal); and finishing (final light cuts). Performed on lathes, turning centers, chucking machines, automatic screw machines and similar machines.