Contact Details
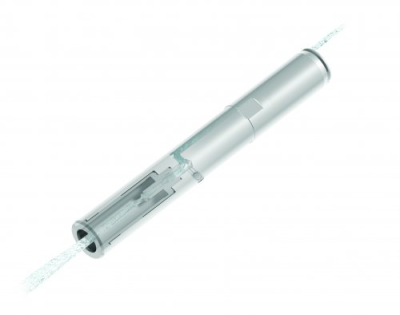
Reaching deep inside a workpiece to drill holes can be a real bear. You’ve tried taper length and aircraft drills, but even those made of solid carbide are apt to wander when hanging out of the chuck unsupported. Maybe you’ve combatted the problem with special extended-reach drill holders, although these are not only expensive, but limited to specific fixed lengths. A double-angle or ER-style collet extension might be worth a try, yet these aren’t exactly compact, and any runout or imbalance is exaggerated at long length to diameter ratios—if drill walk isn’t bad enough, you’re now left fighting the holder itself as it flexes and vibrates. Hole accuracy becomes questionable,
tool life is poor, and productivity suffers as you reduce feed rates in an attempt to keep the drill running true. Surely there’s a better way.
Kennametal thinks so. The tooling manufacturer recently developed a hydraulic chuck extension that meets these challenges while also increasing flexibility and reducing costs. Michael Schuffenhauer, senior global product manager tooling systems at Kennametal, says the company has been producing hydraulic chucks for the past 30 years, and has become quite knowledgeable about the technology behind them as a result. This new tool leverages that
extensive experience.
“We asked our customers, ‘How do you drill holes in deep cavities and complex pockets? Do you have problems with reaching past clamps and fixtures?’” he says. “We wanted to know how they were dealing with these issues, and the effectiveness of their existing solution. Then we set out to develop a better one.”
Kennametal’s new line of hydraulic chuck (HC) extensions meets that goal handily. Schuffenhauer lists a number of key features that make the product unlike any other currently available. These include:
-Runout to within 3 μm (0.00012 in.) at 2.5 x D (half that of its nearest competitor), providing
exceptional tool life and hole quality.
-Because it’s balanced to G2.5 at 25,000 rpm, vibration is greatly reduced at higher spindle
speeds.
-Vibration is further dampened by the hydraulic clamping mechanism within the chuck body.
-Internal channels make through the tool coolant easy to setup—no hoses or adapters needed.
-An ultra-slim design allows, for example, a 12-mm drill to be clamped in a 20-mm chuck body (or a
½-inch drill in a ¾-inch shank).
-A variety of reducer sleeves is available for both inch and metric sizes, providing maximum
flexibility at minimum cost.
-Drill and reamer shanks down to 3 mm (0.125 in.) can be accommodated.
-Suitable for rotating and stationary applications alike.
“Our HC Extensions are for customers that need the flexibility of a modular system but want to avoid the expense and limitations of a custom solution, as well as the constraints that come with traditional toolholders,” Schuffenhauer says. “We believe the improved performance and ease-of-use offered by this new product will soon make it the leading drill extension on the market. It’s quite simply a great design.”
Ease of use means no need for heat-shrink machines. Tool lengths are adjustable up to 10 mm (0.393 in.) axially. A specially ground chamfer on the end of the shank eases insertion into the hydraulic chuck. Prepared wrench flats provide safe and convenient handling, without the need for a torque wrench. A one-piece design eliminates concerns over contamination and downtime due to maintenance. And most importantly, the clamping mechanism eliminates operator to operator tightening variations.
“That’s an important point,” notes Schuffenhauer. “With traditional collet nut systems, the amount of torque applied during tool changes can vary widely, increasing the chance of runout or tool slippage. The same can be said for competing hydraulic extension chucks. But with our solution, there’s no chance of over or under-tightening. It’s not only extremely accurate, but it’s extremely accurate every time.”
For all its performance, the design is simple—just set any h6 tool shank inside the HC Extension and turn the clamping screw on the end of the unit until seated. This causes a hydraulic piston within the unit to move forward, compressing the locating sleeve, and gripping the tool. Again, total runout as measured 2.5 x D from the chuck face will not exceed 3 μm (0.00012 in.), and the extension’s superior balance characteristics make it an ideal choice for today’s high rpm machine tools.
At the end of the day, says Schuffenhauer, customers want to achieve the safest, most economical, and predictable way to machine parts, hopefully with tooling and equipment that is easy to use. The HC Extension meets all of these criteria and more. “If you look at it from a high level, the HC Extension gives you the flexibility of a collet system with the precision of shrink fit, and easier setup than either. You get the best of all worlds. And because of the HC’s extreme accuracy and balance, you don’t have to settle for substandard tool life and performance as would
with purely mechanical clamping systems.”
Related Glossary Terms
- chuck
chuck
Workholding device that affixes to a mill, lathe or drill-press spindle. It holds a tool or workpiece by one end, allowing it to be rotated. May also be fitted to the machine table to hold a workpiece. Two or more adjustable jaws actually hold the tool or part. May be actuated manually, pneumatically, hydraulically or electrically. See collet.
- collet
collet
Flexible-sided device that secures a tool or workpiece. Similar in function to a chuck, but can accommodate only a narrow size range. Typically provides greater gripping force and precision than a chuck. See chuck.
- coolant
coolant
Fluid that reduces temperature buildup at the tool/workpiece interface during machining. Normally takes the form of a liquid such as soluble or chemical mixtures (semisynthetic, synthetic) but can be pressurized air or other gas. Because of water’s ability to absorb great quantities of heat, it is widely used as a coolant and vehicle for various cutting compounds, with the water-to-compound ratio varying with the machining task. See cutting fluid; semisynthetic cutting fluid; soluble-oil cutting fluid; synthetic cutting fluid.
- feed
feed
Rate of change of position of the tool as a whole, relative to the workpiece while cutting.
- reamer
reamer
Rotating cutting tool used to enlarge a drilled hole to size. Normally removes only a small amount of stock. The workpiece supports the multiple-edge cutting tool. Also for contouring an existing hole.
- shank
shank
Main body of a tool; the portion of a drill or similar end-held tool that fits into a collet, chuck or similar mounting device.