Contact Details
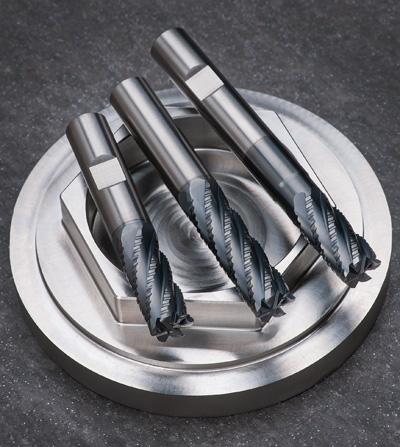
IMCO Carbide Tool announced a January launch for a new high-performance end mill designed specifically to overcome the challenges of machining in high-temperature alloys.
"The new INCONEX line is a real breakthrough in productivity for machining in Inconel, Hastalloy, Waspalloy, and similar high-temp alloys," said Perry Osburn, IMCO president.
Tested in-house against an array of competitor's end mills and IMCO's Omega-6 design, INCONEX end mills lasted up to three times longer than competitors' designs and twice as long as the Omega-6 tools.
"Today's high-temp alloys were engineered to hold up under some of the worst conditions on the planet," said Matt Osburn, IMCO vice president, operations. "When you're machining, those same high-strength properties become barriers to productivity. They can chew through conventional cutting tools in no time. INCONEX M8 Series tools are designed with high-strength properties and a special chip creation design to break through those barriers and keep on going."
New INCONEX M8 Series tools feature a carbide core with 20 percent higher transverse rupture strength and six flutes with optimized rake and relief angles for maximum cutting edge engagement. Advanced AlCrNX coating protects the tool's specially engineered cutting edges from the intense heat generated in the cutting zone.
"Then we developed a new chip creation design," explained Steve Avers, application support team leader. "Each cutting edge is specially shaped to reduce edge wearing stress in the cutting zone. An added benefit of the new design is much smaller chips that can be easily flushed from the work zone."
"With increased demand for hi-temp alloys in the aerospace and energy industries, INCONEX M8 Series tools will fill a real need for longer tool life," said IMCO Sales Manager Tim Elfreich. "It's a big step ahead."
Features include:
• All tools made with corner radius to revent chipping in "crazy-strong" metals.
• Specially designed cutting edges to reduce edge damaging stresses in the cutting zone for longer tool life.
• Tough carbide core offers higher transverse rupture strength for longer tool life.
• Six high-strength flutes provides higher cutting-edge engagement and more cutting edges for longer tool life.
• Optimized rake and relief angle, with premium eccentric grind and edge treatment for prolonged wear.
• Advanced AlCrNX coating to keep tool lubricated and cutting longer in high-temperature alloys.
• Neck relief option to improve stability, minimize flute length and maximize reach.
Related Glossary Terms
- alloys
alloys
Substances having metallic properties and being composed of two or more chemical elements of which at least one is a metal.
- flutes
flutes
Grooves and spaces in the body of a tool that permit chip removal from, and cutting-fluid application to, the point of cut.
- milling machine ( mill)
milling machine ( mill)
Runs endmills and arbor-mounted milling cutters. Features include a head with a spindle that drives the cutters; a column, knee and table that provide motion in the three Cartesian axes; and a base that supports the components and houses the cutting-fluid pump and reservoir. The work is mounted on the table and fed into the rotating cutter or endmill to accomplish the milling steps; vertical milling machines also feed endmills into the work by means of a spindle-mounted quill. Models range from small manual machines to big bed-type and duplex mills. All take one of three basic forms: vertical, horizontal or convertible horizontal/vertical. Vertical machines may be knee-type (the table is mounted on a knee that can be elevated) or bed-type (the table is securely supported and only moves horizontally). In general, horizontal machines are bigger and more powerful, while vertical machines are lighter but more versatile and easier to set up and operate.
- rake
rake
Angle of inclination between the face of the cutting tool and the workpiece. If the face of the tool lies in a plane through the axis of the workpiece, the tool is said to have a neutral, or zero, rake. If the inclination of the tool face makes the cutting edge more acute than when the rake angle is zero, the rake is positive. If the inclination of the tool face makes the cutting edge less acute or more blunt than when the rake angle is zero, the rake is negative.
- relief
relief
Space provided behind the cutting edges to prevent rubbing. Sometimes called primary relief. Secondary relief provides additional space behind primary relief. Relief on end teeth is axial relief; relief on side teeth is peripheral relief.