Contact Details
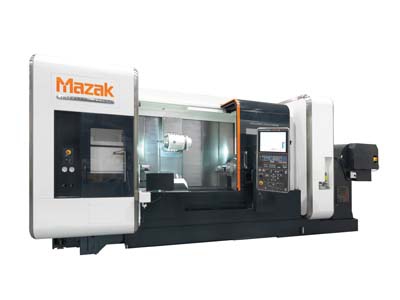
The Mazak INTEGREX i-200ST Multi-Tasking machine efficiently processes mid-size complex components. It offers versatility and high accuracy in a compact design as well as features twin spindles, a lower turret and milling spindle for unbeatable Done-In-One productivity.
As a Level 4 machine in Mazak's Five Levels of Multi-Tasking, the INTEGREX i-200ST turns, drills, taps and mills, while offering off-centerline and full simultaneous 5-axis contouring. Mazak developed its Five Levels of Multi-Tasking as an effective way for manufacturers to determine the best multi-tasking technology for meeting their specific application and process needs.
Within the Five Levels of Multi-Tasking, Level 1 machines typically offer a single turning spindle and drum-style turret with rotating tool capability for processing minimally complex workpieces. Level 2 machines add Y-axis functionality for off-center operations and Done-In-One machining together with either a twin spindle and milling turret or twin spindle/twin turret machine configuration. Level 3 Multi-Tasking machines feature independent milling spindle headstocks with B-axis indexing, as well as Y-axis travels and tool storage magazines. Level 4 machines emphasize automation and processing large or highly complex workpieces using full, simultaneous 5-axis machining. Level 5 is the addition of specialized machining tasks, such as gear cutting, honing and grinding, that transform Level 4 machines into Level 5 Ultra-Tasking machines that process even the most demanding and complex parts complete in single setups.
Both turning spindles on the INTEGREX i-200ST provide equal high performance with spindle speeds of 5,000 rpm and C-axis turning control. And both have a bore capacity measuring 3" (76mm) in diameter.
For C-axis contouring versatility at either turning spindle, the INTEGREX i-200ST vertically mounted milling spindle provides 30 hp (22 kW), 12,000 rpm and a rotating Baxis range of -30 degrees to +240 degrees. Mazak's unique roller cam drive for the B-axis ensures higher accuracy and rigidity, while providing zero backlash. A 36-tool (72-tool optional) magazine allows for fast tool changes and provides ample tooling for continuous part processing.
The lower turret on the INTEGREX i-200ST model comes standard for 9 turning tools. The lower turret working in combination with the machine's milling spindle that can be applied to either side of the machine headstock reduces machining cycle times.
Mazak incorporates its MX Hybrid Roller Guide System into the INTEGREX i-200ST for durability and reliability that result in long-term accuracy. The MX Hybrid Roller Guide System dampens vibration to extend tool life, handles higher load capacities, accelerates and decelerates quicker to shorten cycle times, consumes less oil for "Greener" operations, and lasts longer with less required maintenance.
For a compact multi-tasking center, the INTEGREX i-200ST provides an ample Y-axis travel of 9.8" (249mm) and vertical X-axis of 24.2" (615mm), with 4.92" (125mm) below centerline. The machine accommodates parts up to 25.9" (657.8mm) in diameter. And because its tool magazine is located at the front, machine operators can do programming and tool setup with minimal required movement. Additionally, all machine lubrication points and gages are gathered into a single panel for ease of viewing and maintenance.
Related Glossary Terms
- backlash
backlash
Reaction in dynamic motion systems where potential energy that was created while the object was in motion is released when the object stops. Release of this potential energy or inertia causes the device to quickly snap backward relative to the last direction of motion. Backlash can cause a system’s final resting position to be different from what was intended and from where the control system intended to stop the device.
- computer-aided manufacturing ( CAM)
computer-aided manufacturing ( CAM)
Use of computers to control machining and manufacturing processes.
- gang cutting ( milling)
gang cutting ( milling)
Machining with several cutters mounted on a single arbor, generally for simultaneous cutting.
- grinding
grinding
Machining operation in which material is removed from the workpiece by a powered abrasive wheel, stone, belt, paste, sheet, compound, slurry, etc. Takes various forms: surface grinding (creates flat and/or squared surfaces); cylindrical grinding (for external cylindrical and tapered shapes, fillets, undercuts, etc.); centerless grinding; chamfering; thread and form grinding; tool and cutter grinding; offhand grinding; lapping and polishing (grinding with extremely fine grits to create ultrasmooth surfaces); honing; and disc grinding.
- milling
milling
Machining operation in which metal or other material is removed by applying power to a rotating cutter. In vertical milling, the cutting tool is mounted vertically on the spindle. In horizontal milling, the cutting tool is mounted horizontally, either directly on the spindle or on an arbor. Horizontal milling is further broken down into conventional milling, where the cutter rotates opposite the direction of feed, or “up” into the workpiece; and climb milling, where the cutter rotates in the direction of feed, or “down” into the workpiece. Milling operations include plane or surface milling, endmilling, facemilling, angle milling, form milling and profiling.
- turning
turning
Workpiece is held in a chuck, mounted on a face plate or secured between centers and rotated while a cutting tool, normally a single-point tool, is fed into it along its periphery or across its end or face. Takes the form of straight turning (cutting along the periphery of the workpiece); taper turning (creating a taper); step turning (turning different-size diameters on the same work); chamfering (beveling an edge or shoulder); facing (cutting on an end); turning threads (usually external but can be internal); roughing (high-volume metal removal); and finishing (final light cuts). Performed on lathes, turning centers, chucking machines, automatic screw machines and similar machines.