Contact Details
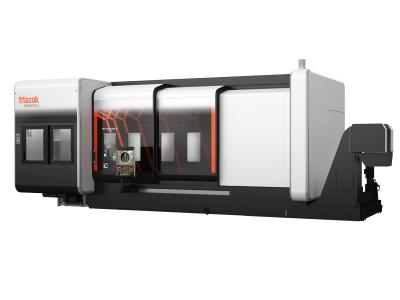
Mazak Corp.'s Integrex i-500 advanced multitask machine is the biggest model in the Integrex i Series family and offers manufacturers more options for machining large, complex workpieces. The machine is available with a 5.2” bore and a 15” chuck on the main horizontal turning spindle and is capable of C-axis indexing in 0.0001-degree increments and comes standard with a 40-hp (30 kW) integral spindle motor that provides a maximum spindle speed of 2,500 rpm.
Customers may select one of four different spindle bore configurations depending on application requirements. A high torque/max rpm’s option are available. Additionally, a 30-hp (22 kW), 12,000-rpm milling integral motor spindle rotates in the B-axis throughout a range of +210 and -30 degrees from vertical. A compact milling spindle head, in conjunction with a generous Y-axis stroke of 16.93" (430 mm), create an increased working capacity for larger applications. Optional milling spindle configurations include a 12,000-rpm, 50-hp (37 kW) high-output spindle, a 20,000-rpm, 32-hp (24 kW) high-speed spindle and a 10,000-rpm, 50-hp (37 kW) CAT 50 taper spindle.
For increased versatility, the Integrex i-500 accommodates workpieces up to 27.56" (700 mm) in diameter and 62.09"L (1,577 mm) / 96.65"L (2,455 mm) or 115.96”L (2,920mm) in part lengths for the 1500U/2500U/3000U configurations, respectively. It is also able to meet the machining requirements of a wide variety of workpieces thanks to its tool magazine capacities, which range from the standard 36 tools up to the maximum of 220 in a 40 taper with field expansion capability or up to 108 tools in a 50 taper magazine.
Further options for the Integrex i-500 include a long drill stocker for the 2500U/3000U models, a variety of steady rests capable of supporting workpieces up to 16.14" (410 mm) in diameter and an NC tailstock with built-in center. Optionally available for Done-In-One is a second spindle with three spindle bore options and for increase part
throughput a nine-postion lower turret is available with 10,000-rpm milling available.
Related Glossary Terms
- chuck
chuck
Workholding device that affixes to a mill, lathe or drill-press spindle. It holds a tool or workpiece by one end, allowing it to be rotated. May also be fitted to the machine table to hold a workpiece. Two or more adjustable jaws actually hold the tool or part. May be actuated manually, pneumatically, hydraulically or electrically. See collet.
- gang cutting ( milling)
gang cutting ( milling)
Machining with several cutters mounted on a single arbor, generally for simultaneous cutting.
- milling
milling
Machining operation in which metal or other material is removed by applying power to a rotating cutter. In vertical milling, the cutting tool is mounted vertically on the spindle. In horizontal milling, the cutting tool is mounted horizontally, either directly on the spindle or on an arbor. Horizontal milling is further broken down into conventional milling, where the cutter rotates opposite the direction of feed, or “up” into the workpiece; and climb milling, where the cutter rotates in the direction of feed, or “down” into the workpiece. Milling operations include plane or surface milling, endmilling, facemilling, angle milling, form milling and profiling.
- numerical control ( NC)
numerical control ( NC)
Any controlled equipment that allows an operator to program its movement by entering a series of coded numbers and symbols. See CNC, computer numerical control; DNC, direct numerical control.
- turning
turning
Workpiece is held in a chuck, mounted on a face plate or secured between centers and rotated while a cutting tool, normally a single-point tool, is fed into it along its periphery or across its end or face. Takes the form of straight turning (cutting along the periphery of the workpiece); taper turning (creating a taper); step turning (turning different-size diameters on the same work); chamfering (beveling an edge or shoulder); facing (cutting on an end); turning threads (usually external but can be internal); roughing (high-volume metal removal); and finishing (final light cuts). Performed on lathes, turning centers, chucking machines, automatic screw machines and similar machines.