Contact Details
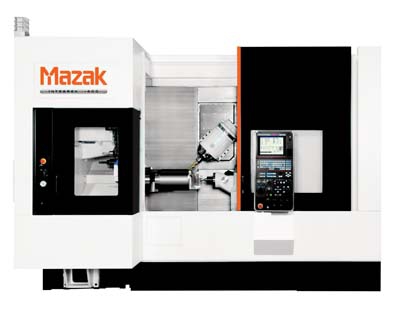
February 2012 — The Mazak INTEGREX j-400 is a technologically innovative machine that provides Multi-Tasking capabilities for processing large and complex components. It performs 4-axis simultaneous machining with 5-axis tool tip positioning, providing significant advantages in productivity, accuracy and flexibility.
Unlike Multi-Tasking machines with drum-style turrets, Mazak's INTEGREX j-400 comes standard with a 20-tool magazine (36- and 72-tool magazines optional) for increasing versatility in part production. The machine's main turning spindle with C-axis control features a 12" chuck mounted on a 30 hp (22 kW), 3,300-rpm integral spindle that generates high levels of torque for even the most demanding jobs.
The INTEGREX j-400 also includes a powerful 30 hp (22 kW), 12,000-rpm milling spindle that can be indexed in 5 degree (or optional 1 degree) increments from -30 degrees to 190 degrees, making it possible to perform O.D. machining, as well as turning, facing, grooving and threading with the same flash tool. It also makes it easy to perform incline machining and all other conventional machining processes. Additionally, the milling spindle can be radially indexed and clamped, enabling the same tool to be used for turning in both forward and reverse directions.
Though the INTEGREX j-400 is compact with a footprint measuring 166.93" x 106.50" (4,240mm x 2,705mm), it offers a maximum machining diameter of 19.7" (500mm) and maximum length of 24.76" (629mm) with minimum tool interference for large workpieces. Its long axis strokes allow face milling, end milling and drilling to take place above and below the centerline without C-axis indexing. In addition, the machine's true Y-axis design allows for a larger machine envelope and tool reach, reduced interference and excellent chip evacuation when compared to conventional machines.
Constructed for high rigidity and featuring new high-response servomotors, the INTEGREX j-400 delivers high repeatability of tool tip positioning. Additionally, the machine incorporates Mazak's MX Hybrid Roller Guide System that delivers levels of durability and reliability that result in long-term accuracy. The Mazak MX Hybrid Roller Guide System increases vibration dampening to extend tool life, handles higher load capacities, accelerates and decelerates quicker to shorten cycle times, consumes less oil for "Greener" operations, and lasts longer with less required maintenance.
Mazak makes the programming of multiple part surfaces on the INTEGREX j-Series easy with its MATRIX NEXUS CNC control. The control allows for both conversational and EIA/ISO programming, and ensures easy programming for C-axis, Y-axis and angle machining. MATRIX also provides realistic 3D machining simulations, time study analysis and the Mazak Voice Advisor, which assists operators during set up to make initial operations smoother and safer.
Related Glossary Terms
- chuck
chuck
Workholding device that affixes to a mill, lathe or drill-press spindle. It holds a tool or workpiece by one end, allowing it to be rotated. May also be fitted to the machine table to hold a workpiece. Two or more adjustable jaws actually hold the tool or part. May be actuated manually, pneumatically, hydraulically or electrically. See collet.
- computer numerical control ( CNC)
computer numerical control ( CNC)
Microprocessor-based controller dedicated to a machine tool that permits the creation or modification of parts. Programmed numerical control activates the machine’s servos and spindle drives and controls the various machining operations. See DNC, direct numerical control; NC, numerical control.
- flash
flash
Thin web or film of metal on a casting that occurs at die partings and around air vents and movable cores. This excess metal is due to necessary working and operating clearances in a die. Flash also is the excess material squeezed out of the cavity as a compression mold closes or as pressure is applied to the cavity.
- gang cutting ( milling)
gang cutting ( milling)
Machining with several cutters mounted on a single arbor, generally for simultaneous cutting.
- grooving
grooving
Machining grooves and shallow channels. Example: grooving ball-bearing raceways. Typically performed by tools that are capable of light cuts at high feed rates. Imparts high-quality finish.
- milling
milling
Machining operation in which metal or other material is removed by applying power to a rotating cutter. In vertical milling, the cutting tool is mounted vertically on the spindle. In horizontal milling, the cutting tool is mounted horizontally, either directly on the spindle or on an arbor. Horizontal milling is further broken down into conventional milling, where the cutter rotates opposite the direction of feed, or “up” into the workpiece; and climb milling, where the cutter rotates in the direction of feed, or “down” into the workpiece. Milling operations include plane or surface milling, endmilling, facemilling, angle milling, form milling and profiling.
- threading
threading
Process of both external (e.g., thread milling) and internal (e.g., tapping, thread milling) cutting, turning and rolling of threads into particular material. Standardized specifications are available to determine the desired results of the threading process. Numerous thread-series designations are written for specific applications. Threading often is performed on a lathe. Specifications such as thread height are critical in determining the strength of the threads. The material used is taken into consideration in determining the expected results of any particular application for that threaded piece. In external threading, a calculated depth is required as well as a particular angle to the cut. To perform internal threading, the exact diameter to bore the hole is critical before threading. The threads are distinguished from one another by the amount of tolerance and/or allowance that is specified. See turning.
- turning
turning
Workpiece is held in a chuck, mounted on a face plate or secured between centers and rotated while a cutting tool, normally a single-point tool, is fed into it along its periphery or across its end or face. Takes the form of straight turning (cutting along the periphery of the workpiece); taper turning (creating a taper); step turning (turning different-size diameters on the same work); chamfering (beveling an edge or shoulder); facing (cutting on an end); turning threads (usually external but can be internal); roughing (high-volume metal removal); and finishing (final light cuts). Performed on lathes, turning centers, chucking machines, automatic screw machines and similar machines.