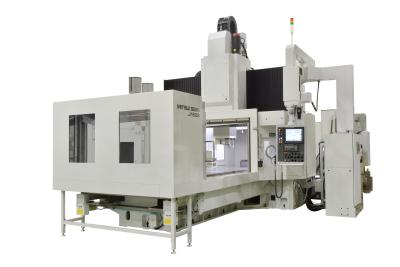
According to Mitsui Seiki USA, one of the leading builders of jig borers, the market demand for these ultra-precise machines is on the rise. “Jig borers typically last 25 to 30 years,” said Mitsui Seiki USA’s Bill Malanche, COO. “Now seems to be the time that people are retiring their legacy machines and looking to buy new.” Mitsui Seiki’s newest line, the J12/J/16 jig borer series, combines large capacity and high precision to meet the increasing need for accuracy for machining workpieces such as molds and castings. The machines offer Y-axis stroke of either 1,250 mm or 1,600 mm, with standard table sizes of 2,400 mm x 1,250 mm or 2,900 mm x 1,600 mm.
The machines’ strong and durable structures provide table lateral movement accuracy of 2.5 µm or better. The Z-axis guide system is restrained on four sides to maximize rigidity and reliability, and dual ball screws ensure stable feed motion.
For precision holemaking applications, XY interpolation enables the J12/J16 machines to carry out high-precision contouring by utilizing an end mill instead of a boring tool, eliminating the need to manually adjust a boring tool to accurately finish the hole diameter avoiding bottlenecks. Pitch accuracy is within 5 µm even for large-pitch holes.
The machines feature a 12,000 rpm 50 taper spindle and automatic toolchange capacity of 60 tools. Additional options such as quill spindle, increased work capacity, as well as automation features are available to meet the customers’ needs.
“Machines in Mitsui Seiki’s J12/J/16 jig borer series are engineered to process a large range of part sizes with unceasing repeatability,” said Malanche. “They provide the durability, accuracy and flexibility required in today’s highly-competitive manufacturing environment.”
Contact Details
Related Glossary Terms
- boring
boring
Enlarging a hole that already has been drilled or cored. Generally, it is an operation of truing the previously drilled hole with a single-point, lathe-type tool. Boring is essentially internal turning, in that usually a single-point cutting tool forms the internal shape. Some tools are available with two cutting edges to balance cutting forces.
- feed
feed
Rate of change of position of the tool as a whole, relative to the workpiece while cutting.
- interpolation
interpolation
Process of generating a sufficient number of positioning commands for the servomotors driving the machine tool so the path of the tool closely approximates the ideal path. See CNC, computer numerical control; NC, numerical control.
- jig
jig
Tooling usually considered to be a stationary apparatus. A jig assists in the assembly or manufacture of a part or device. It holds the workpiece while guiding the cutting tool with a bushing. A jig used in subassembly or final assembly might provide assembly aids such as alignments and adjustments. See fixture.
- milling machine ( mill)
milling machine ( mill)
Runs endmills and arbor-mounted milling cutters. Features include a head with a spindle that drives the cutters; a column, knee and table that provide motion in the three Cartesian axes; and a base that supports the components and houses the cutting-fluid pump and reservoir. The work is mounted on the table and fed into the rotating cutter or endmill to accomplish the milling steps; vertical milling machines also feed endmills into the work by means of a spindle-mounted quill. Models range from small manual machines to big bed-type and duplex mills. All take one of three basic forms: vertical, horizontal or convertible horizontal/vertical. Vertical machines may be knee-type (the table is mounted on a knee that can be elevated) or bed-type (the table is securely supported and only moves horizontally). In general, horizontal machines are bigger and more powerful, while vertical machines are lighter but more versatile and easier to set up and operate.
- pitch
pitch
1. On a saw blade, the number of teeth per inch. 2. In threading, the number of threads per inch.