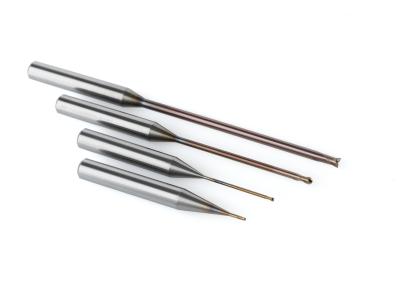
Shops that struggle to machine microsized workpiece surfaces can now impart superior surface finishes and enhance accuracy and precision with the new Seco Tools JM100 Mini endmills. In micromachining operations with zero visibility of workpiece and cutting tool, the JM100 Mini delivers long tool life, stability and guaranteed surface quality thanks to its extremely precise geometries, virtually zero runout, advanced coatings and tight radius tolerances.
Targeted to achieve fine surface finishes on mold and die components and able to machine tool steel as hard as 48 to 65 HRC, the JM100 Mini helps shops minimize secondary benchwork that can increase part processing time. The endmill’s special coating reduces tool wear to help lower overall tool costs and eliminate the need for frequent tool changes. It also ensures smooth and consistent surface finishes that yield exceptional part performance. Tight radius tolerances of ±0.005μm on the tool reduce runout virtually to zero, increasing output and contributing to lower cost per part with high process precision, stability and reliability.
The JM100 Mini is available in tool diameters from 0.2 mm to 3.0 mm (0.008" to 0.118") and corner radii ranging from 0.05 mm to 0.3 mm (0.002" to 0.012") RE = ±0.005, with 2- and 3-flute versions.