Contact Details
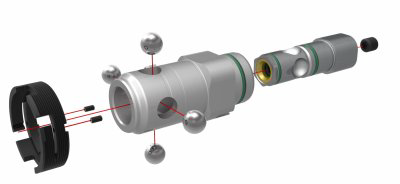
Kennametal Inc. says the bending moment of KM4X is substantially higher than any tooling interface available on the market, superior even to Kennametal’s own KM design. So when aerospace giant Boeing came to Kennametal with a request for a heavy-duty spindle connection capable of outperforming traditional CAT and BT-style adapters, tooling
engineers turned to this robust and well-established platform as a starting point. The result was a 100 mm spindle connection with four ball tracks instead of two and up to 40 percent greater clamping force than comparably sized KM tooling.
That was 15 years ago. KM continues to thrive, and was adopted in 2008 by the International Organization for Standardization (ISO) as ISO standard 26622. The original Boeing-inspired design has been renamed as well, and marketed for the past several years as KM4X100, a spindle platform popular with machine builders such as Fives
Group, Mitsui Seiki, Stama and others, as well as those machine shops looking for superior rigidity in demanding machining conditions.
That popularity is about to grow. Kennametal has announced the KM4X tooling family has gained a 63 mm sibling, one aimed at a broader machine tool platform and, therefore, greater availability to the machining community.
“Just as we did with Boeing, we challenged ourselves to make a great solution even better,” says Bill Redman, Kennametal global product manager, tooling systems. “The clamping strength, bending stiffness, and rpm capabilities of the KM4X63 are dramatically higher than virtually any other connection out there.”
Redman and others on the product management and engineering team aren’t done. They recently approached a number of machine builders to ask for opinions on the initial KM4X product offering. Based on that feedback, Kennametal continues to expand the portfolio—the KM4X lineup now includes shrink fit toolholders, HydroForce hydraulic chucks, TG and ER collet chucks, and a variety of other spindle tooling, clamping units and modular adapters, with more on the way.
“By the end of 2016, we're going to add roughly 30 new line items, most of which will be extensions in the 80 to 200 mm range, and centerline turning tools to support mill-turnapplications,” says Redman. “We’ve found that, because of KM4X’s extreme rigidity, we can greatly increase gage lengths. This means our customers can reach much farther
without having to buy a special tool, something that’s especially important with 5-axis machining—they can basically add on whatever extension length is needed and off they go, in both static or rotating applications. We're pretty excited about that.”
One example of this is a 674 mm gage length (26.54 in.) KM4X boring bar. “KM4X63 has a maximum bending moment of 2,100 Nm (1548 ft. lb.) and, depending on the machine, clamping force of 36 to 58 Kn (8093 to 13038 lb.),” he says. “It’s the strongest connection available in this size range, period.”
It’s also faster. Redman says KM4X63 comes “out of the box” capable to 38,000 rpm, which is higher than HSK-A and “dramatically” faster than competing brands of spindle tooling.
For those shops on the fence about spindle tooling and quick-change, Redman offers the following advice. “There’s nothing worse than going into a shop that just bought a $500,000 machining center or lathe and then discovers they should have opted for a different tooling platform. We as tooling providers have an obligation to educate customers, and get them thinking about what they’re trying to accomplish—whether they need high spindle speeds for an aluminum or die-mold application, or greater low-end torque for titanium and HRSA machining. The majority of tooling systems out there can accommodate one of these things, but not both. We feel KM4X provides a competitive
advantage no matter what you’re cutting.”
Related Glossary Terms
- boring
boring
Enlarging a hole that already has been drilled or cored. Generally, it is an operation of truing the previously drilled hole with a single-point, lathe-type tool. Boring is essentially internal turning, in that usually a single-point cutting tool forms the internal shape. Some tools are available with two cutting edges to balance cutting forces.
- boring bar
boring bar
Essentially a cantilever beam that holds one or more cutting tools in position during a boring operation. Can be held stationary and moved axially while the workpiece revolves around it, or revolved and moved axially while the workpiece is held stationary, or a combination of these actions. Installed on milling, drilling and boring machines, as well as lathes and machining centers.
- collet
collet
Flexible-sided device that secures a tool or workpiece. Similar in function to a chuck, but can accommodate only a narrow size range. Typically provides greater gripping force and precision than a chuck. See chuck.
- lathe
lathe
Turning machine capable of sawing, milling, grinding, gear-cutting, drilling, reaming, boring, threading, facing, chamfering, grooving, knurling, spinning, parting, necking, taper-cutting, and cam- and eccentric-cutting, as well as step- and straight-turning. Comes in a variety of forms, ranging from manual to semiautomatic to fully automatic, with major types being engine lathes, turning and contouring lathes, turret lathes and numerical-control lathes. The engine lathe consists of a headstock and spindle, tailstock, bed, carriage (complete with apron) and cross slides. Features include gear- (speed) and feed-selector levers, toolpost, compound rest, lead screw and reversing lead screw, threading dial and rapid-traverse lever. Special lathe types include through-the-spindle, camshaft and crankshaft, brake drum and rotor, spinning and gun-barrel machines. Toolroom and bench lathes are used for precision work; the former for tool-and-die work and similar tasks, the latter for small workpieces (instruments, watches), normally without a power feed. Models are typically designated according to their “swing,” or the largest-diameter workpiece that can be rotated; bed length, or the distance between centers; and horsepower generated. See turning machine.
- machining center
machining center
CNC machine tool capable of drilling, reaming, tapping, milling and boring. Normally comes with an automatic toolchanger. See automatic toolchanger.
- stiffness
stiffness
1. Ability of a material or part to resist elastic deflection. 2. The rate of stress with respect to strain; the greater the stress required to produce a given strain, the stiffer the material is said to be. See dynamic stiffness; static stiffness.
- turning
turning
Workpiece is held in a chuck, mounted on a face plate or secured between centers and rotated while a cutting tool, normally a single-point tool, is fed into it along its periphery or across its end or face. Takes the form of straight turning (cutting along the periphery of the workpiece); taper turning (creating a taper); step turning (turning different-size diameters on the same work); chamfering (beveling an edge or shoulder); facing (cutting on an end); turning threads (usually external but can be internal); roughing (high-volume metal removal); and finishing (final light cuts). Performed on lathes, turning centers, chucking machines, automatic screw machines and similar machines.