Contact Details
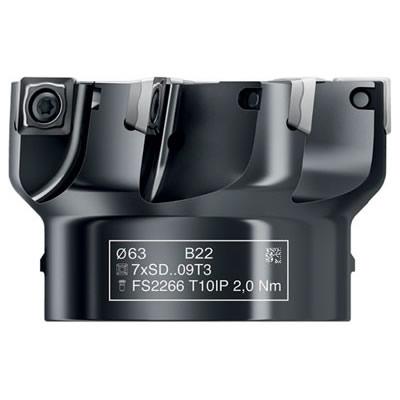
Walter USA LLC has introduced the M4000, a universal milling system that improves production while reducing tooling requirements, thus reducing costs. The system comprises three different cutter bodies, four indexable inserts and can be employed in an array of milling applications, including facemilling, shoulder milling and chamfering. The system is ideal in all steel and cast iron materials, stainless steels and difficult-to-cut materials. Because one insert can handle several different milling applications, the user's tool and storage costs are reduced.
The flank faces on the four cutting edges of these versatile inserts feature a wave profile that displays the geometry of the insert. The more waves that are visible, the more positive the geometry. Like their more specialized relatives in the Walter BLAXX and Walter XtraÌ¢‰ÛÒå»tec product ranges, the M4000 inserts are coated with Tiger-tec Silver. The inserts, which have rake face markings to ensure accurate orientation when changing the cutting edge, come in stable and universal geometries, and have a positive shape with a clearance angle of 15 degrees. This means that less power is required for milling, so energy consumption is reduced and economic efficiency is increased.
In addition, the inserts provide for a more stable cutting environment while decreasing vibration, which adds to tool life. And as an added plus for the user, the M4000 features a new type of laser engraving which allows Walter to inscribe all important information, such as details about the tooling's assembly parts and torque requirements, on even the smallest tool diameters.
The system's versatility can be enhanced even further through the use of special indexable inserts. For the M4002 high-feed milling cutter, a circumference-sintered insert with facet for improved surfaces is available. A special insert with a larger corner radius increases cutting edge stability when working with the high-feed mill and shoulder mill. For the M4132 shoulder mill in particular, an indexable insert with a fully ground circumference is available, which can also come with additional facets.
The M4000 not only marks the debut of an innovative product line, but of an ecologically friendly and sustainable approach to manufacturing as well. It is the first Walter product line to have its CO2 footprint completely recorded and compensated from the delivery of the raw material, right through to when the finished product is shipped to the customer.
Related Glossary Terms
- chamfering
chamfering
Machining a bevel on a workpiece or tool; improves a tool’s entrance into the cut.
- clearance
clearance
Space provided behind a tool’s land or relief to prevent rubbing and subsequent premature deterioration of the tool. See land; relief.
- facemilling
facemilling
Form of milling that produces a flat surface generally at right angles to the rotating axis of a cutter having teeth or inserts both on its periphery and on its end face.
- gang cutting ( milling)
gang cutting ( milling)
Machining with several cutters mounted on a single arbor, generally for simultaneous cutting.
- indexable insert
indexable insert
Replaceable tool that clamps into a tool body, drill, mill or other cutter body designed to accommodate inserts. Most inserts are made of cemented carbide. Often they are coated with a hard material. Other insert materials are ceramic, cermet, polycrystalline cubic boron nitride and polycrystalline diamond. The insert is used until dull, then indexed, or turned, to expose a fresh cutting edge. When the entire insert is dull, it is usually discarded. Some inserts can be resharpened.
- milling
milling
Machining operation in which metal or other material is removed by applying power to a rotating cutter. In vertical milling, the cutting tool is mounted vertically on the spindle. In horizontal milling, the cutting tool is mounted horizontally, either directly on the spindle or on an arbor. Horizontal milling is further broken down into conventional milling, where the cutter rotates opposite the direction of feed, or “up” into the workpiece; and climb milling, where the cutter rotates in the direction of feed, or “down” into the workpiece. Milling operations include plane or surface milling, endmilling, facemilling, angle milling, form milling and profiling.
- milling cutter
milling cutter
Loosely, any milling tool. Horizontal cutters take the form of plain milling cutters, plain spiral-tooth cutters, helical cutters, side-milling cutters, staggered-tooth side-milling cutters, facemilling cutters, angular cutters, double-angle cutters, convex and concave form-milling cutters, straddle-sprocket cutters, spur-gear cutters, corner-rounding cutters and slitting saws. Vertical cutters use shank-mounted cutting tools, including endmills, T-slot cutters, Woodruff keyseat cutters and dovetail cutters; these may also be used on horizontal mills. See milling.
- milling machine ( mill)
milling machine ( mill)
Runs endmills and arbor-mounted milling cutters. Features include a head with a spindle that drives the cutters; a column, knee and table that provide motion in the three Cartesian axes; and a base that supports the components and houses the cutting-fluid pump and reservoir. The work is mounted on the table and fed into the rotating cutter or endmill to accomplish the milling steps; vertical milling machines also feed endmills into the work by means of a spindle-mounted quill. Models range from small manual machines to big bed-type and duplex mills. All take one of three basic forms: vertical, horizontal or convertible horizontal/vertical. Vertical machines may be knee-type (the table is mounted on a knee that can be elevated) or bed-type (the table is securely supported and only moves horizontally). In general, horizontal machines are bigger and more powerful, while vertical machines are lighter but more versatile and easier to set up and operate.
- rake
rake
Angle of inclination between the face of the cutting tool and the workpiece. If the face of the tool lies in a plane through the axis of the workpiece, the tool is said to have a neutral, or zero, rake. If the inclination of the tool face makes the cutting edge more acute than when the rake angle is zero, the rake is positive. If the inclination of the tool face makes the cutting edge less acute or more blunt than when the rake angle is zero, the rake is negative.
- stainless steels
stainless steels
Stainless steels possess high strength, heat resistance, excellent workability and erosion resistance. Four general classes have been developed to cover a range of mechanical and physical properties for particular applications. The four classes are: the austenitic types of the chromium-nickel-manganese 200 series and the chromium-nickel 300 series; the martensitic types of the chromium, hardenable 400 series; the chromium, nonhardenable 400-series ferritic types; and the precipitation-hardening type of chromium-nickel alloys with additional elements that are hardenable by solution treating and aging.
Additional Products from Walter USA LLC
Pagination
- First page
- Previous page
- …
- 17
- 18
- 19
- 20
- 21
- 22
- 23
- 24
- 25