Contact Details
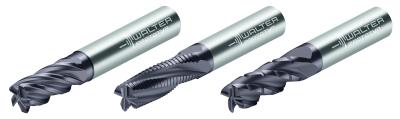
With more than 3,000 new cutting tools in inch sizes, Walter takes the lead in solid carbide milling. The offerings include the MA230, MA320 and MA321 Advance shoulder/slot mills for universal application.
The MA230 Advance solid carbide milling cutting is for universal machining of steel, stainless steel, cast iron and high-temperature superalloys (ISO P, M, K and S workpiece groups) at the highest level. The tool’s unique edge prep enables stable and efficient cutting action. An eccentric relief provides an exceptionally strong cutting edge, and a proprietary coating allows for a higher cutting speed and extended tool life.
The MA230 Advance cutter is for high-performance roughing and finishing and enables reliable milling with an extremely high metal removal rate. Most sizes are available with either a standard or reduced neck. The diameter range is from 0.031 to 1.0 inch. These tools are available in 3, 4, 5, 7 and 9 flute versions. For example, the 7-flute mill offers extreme metal removal rates delivered at full flute length and a 15% radial engagement for high-feed machining processes. The 9-flute mill is excellent for finishing tight tolerance walls.
The MA321/MA320 Advance solid carbide milling cutters were also developed for machining ISO P, M, K and S workpieces. The multiple use tools are designed for roughing and semi-finishing in a single pass. The sinusoidal ground profile ensures optimal chip evacuation, outstanding heat resistance and minimum tool wear. The tools are ideally suited for milling ferrous materials with a medium hardness and appropriate for use when heavy cutting while still providing fine surface finishes. The diameter range is from 3/16 to 1.0 inch. The tools are available with a cylindrical shank in 4 and 5 flute versions.
The Walter lineup of products consists of three categories of tools. Supreme tools indicate the highest level of technology and performance available. Advance tools indicate products efficiently balanced between price and performance and Perform tools are products that provide an economical solution with focused importance on price.
Related Glossary Terms
- cutting speed
cutting speed
Tangential velocity on the surface of the tool or workpiece at the cutting interface. The formula for cutting speed (sfm) is tool diameter 5 0.26 5 spindle speed (rpm). The formula for feed per tooth (fpt) is table feed (ipm)/number of flutes/spindle speed (rpm). The formula for spindle speed (rpm) is cutting speed (sfm) 5 3.82/tool diameter. The formula for table feed (ipm) is feed per tooth (ftp) 5 number of tool flutes 5 spindle speed (rpm).
- gang cutting ( milling)
gang cutting ( milling)
Machining with several cutters mounted on a single arbor, generally for simultaneous cutting.
- hardness
hardness
Hardness is a measure of the resistance of a material to surface indentation or abrasion. There is no absolute scale for hardness. In order to express hardness quantitatively, each type of test has its own scale, which defines hardness. Indentation hardness obtained through static methods is measured by Brinell, Rockwell, Vickers and Knoop tests. Hardness without indentation is measured by a dynamic method, known as the Scleroscope test.
- milling
milling
Machining operation in which metal or other material is removed by applying power to a rotating cutter. In vertical milling, the cutting tool is mounted vertically on the spindle. In horizontal milling, the cutting tool is mounted horizontally, either directly on the spindle or on an arbor. Horizontal milling is further broken down into conventional milling, where the cutter rotates opposite the direction of feed, or “up” into the workpiece; and climb milling, where the cutter rotates in the direction of feed, or “down” into the workpiece. Milling operations include plane or surface milling, endmilling, facemilling, angle milling, form milling and profiling.
- milling machine ( mill)
milling machine ( mill)
Runs endmills and arbor-mounted milling cutters. Features include a head with a spindle that drives the cutters; a column, knee and table that provide motion in the three Cartesian axes; and a base that supports the components and houses the cutting-fluid pump and reservoir. The work is mounted on the table and fed into the rotating cutter or endmill to accomplish the milling steps; vertical milling machines also feed endmills into the work by means of a spindle-mounted quill. Models range from small manual machines to big bed-type and duplex mills. All take one of three basic forms: vertical, horizontal or convertible horizontal/vertical. Vertical machines may be knee-type (the table is mounted on a knee that can be elevated) or bed-type (the table is securely supported and only moves horizontally). In general, horizontal machines are bigger and more powerful, while vertical machines are lighter but more versatile and easier to set up and operate.
- relief
relief
Space provided behind the cutting edges to prevent rubbing. Sometimes called primary relief. Secondary relief provides additional space behind primary relief. Relief on end teeth is axial relief; relief on side teeth is peripheral relief.
- shank
shank
Main body of a tool; the portion of a drill or similar end-held tool that fits into a collet, chuck or similar mounting device.
- superalloys
superalloys
Tough, difficult-to-machine alloys; includes Hastelloy, Inconel and Monel. Many are nickel-base metals.
- tolerance
tolerance
Minimum and maximum amount a workpiece dimension is allowed to vary from a set standard and still be acceptable.
Additional Products from Walter USA LLC
Pagination
- First page
- Previous page
- …
- 17
- 18
- 19
- 20
- 21
- 22
- 23
- 24
- 25