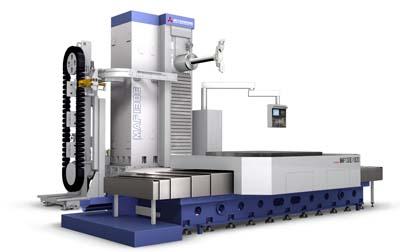
Mitsubishi Heavy Industries Ltd. (MHI) has developed a new series of table-type horizontal boring mills, known as the "MAF-E Series," targeting applications in the machining of parts used in various industrial fields, including construction machinery, heavy-duty vehicles, power generation systems and decelerators. The company today launched two models: the MAF130E and MAF150E featuring boring spindle diameters of 130 and 150mm, respectively. Both machines have an 800mm extendable spindle stroke, the longest among the same class for medium-size workpiece machining, thereby expanding the range of machinable medium-size workpieces. The new offerings also achieve high-speed, high-accuracy machining through their enhanced structural rigidity.
The MAF-E Series, being aimed at the medium-size workpiece machining market, is designed to fill the gap between the company's MAF-C Series, which are floor-type horizontal boring machines that provide outstanding performance and flexibility for cutting large-size workpieces, and its existing MHT Series, table-type horizontal boring machines featuring superior operability suited to small workpiece machining. The MAF-E Series was developed to offer the advantages of both of those system lineups in order to realize economically efficient machining of medium-size workpieces, a task that has conventionally been performed using costly floor-type machines.
By increasing the main spindle stroke extension upto 800mm, the new MAF-E Series units enable deep boring not possible with convertional machines. The main spindle features motor outputs of 30/37 (continuous/30 minutes rated) kW (kilowatts), maximum torque of 2,441⁄3,011 (ditto) Nm (newton meters), spindle rotation speed of max 3,000rpm and a feed rate of 15m (meters) per minute.
To achieve high rigidity, major structures are cast-iron and designed to perform stable machining in both heavy and high-speed cutting applications employing 3D FEM analysis. For all sliding surfaces – X-axis (table travel), B-axis (rotation), Y-axis (main spindle travel) and Z-axis (column travel) – high-rigidity, maintenance-free hydrostatic guide surfaces are adopted. As a result, both static and dynamic rigidity (resistance to vibration) have been enhanced by 20 percent. By minimizing droop (deflection) even when the main spindle is extended, the MAF-E Series machines achieve the highest level of high-speed, heavy-cutting performance in their class.
Three table sizes are available for medium-size workpiece machining, the largest accommodating workpieces weighing up to 20 tons. All units are equipped with operator-friendly on-screen functions such as instructions for performing maintenance, trouble recovery support, and easy centering during workpiece setup. The machines also have a remote monitoring maintenance service function that enables prompt servicing when an irregularity is detected through monitoring of machine conditions at MHI's service center. Other operability enhancing features include an automatic right angle head change mechanism enabling adjustment of the main spindle angle.
MHI expects robust demand for the MAF-E Series for use at various production worksites as a high-efficiency horizontal boring mill applicable to a broad variety of medium-size workpieces, including small-lot wide-variation type production. Anticipated applications include structural components of heavy-duty vehicles such as construction machinery and trucks: for example, hydraulic excavator mainframes, reduction gearboxes, and major components of extruders and hydraulic presses.
Contact Details
Related Glossary Terms
- boring
boring
Enlarging a hole that already has been drilled or cored. Generally, it is an operation of truing the previously drilled hole with a single-point, lathe-type tool. Boring is essentially internal turning, in that usually a single-point cutting tool forms the internal shape. Some tools are available with two cutting edges to balance cutting forces.
- centering
centering
1. Process of locating the center of a workpiece to be mounted on centers. 2. Process of mounting the workpiece concentric to the machine spindle. See centers.
- feed
feed
Rate of change of position of the tool as a whole, relative to the workpiece while cutting.
- milling machine ( mill)
milling machine ( mill)
Runs endmills and arbor-mounted milling cutters. Features include a head with a spindle that drives the cutters; a column, knee and table that provide motion in the three Cartesian axes; and a base that supports the components and houses the cutting-fluid pump and reservoir. The work is mounted on the table and fed into the rotating cutter or endmill to accomplish the milling steps; vertical milling machines also feed endmills into the work by means of a spindle-mounted quill. Models range from small manual machines to big bed-type and duplex mills. All take one of three basic forms: vertical, horizontal or convertible horizontal/vertical. Vertical machines may be knee-type (the table is mounted on a knee that can be elevated) or bed-type (the table is securely supported and only moves horizontally). In general, horizontal machines are bigger and more powerful, while vertical machines are lighter but more versatile and easier to set up and operate.
- recovery
recovery
Reduction or removal of workhardening effects, without motion of large-angle grain boundaries.