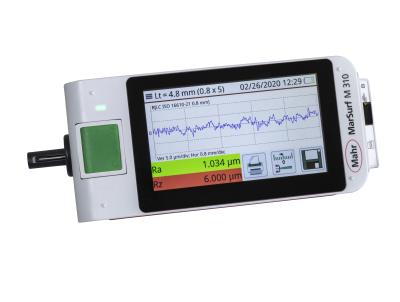
Mahr Inc., a global manufacturer of precision measurement equipment used for dimensional metrology, today introduced the new MarSurf M 310 mobile surface measurement system. The successor to the popular MarSurf M 300, the all-new M 310 brings ease-of-use to new levels with a large, illuminated, rotatable 4.3” high-resolution touch screen built right into the unit. It was designed to provide high-precision measurements to test surface roughness on small and large workpieces.
The new portable unit brings features that were previously only available in PC-based systems to the mobile world. Features including automatic creation of measuring reports in PDF format, integration of a barcode or data matrix scanner, and printing reports to letter size paper are now all standard. An optional portable printer is also available.
The MarSurf M 310 also provides error-free operation through standard-compliant settings.
Automatic cutoff selection ensures the correct measurement results — even for inexperienced technicians. Additionally, a highly efficient battery allows for more than 1,200 measurements on a single charge. Integrated memory enables more than 500,000 measurement results to be stored, 1,500 PDF protocols and an optional Micro SD card slot allows additional memory to be added to increase that up to 320 times — or 160 million results.
“The new MarSurf M 310 is a very convenient, portable surface roughness measurement instrument that even users with little prior knowledge of quality control can operate,” said George Schuetz, Director Precision Gages of Mahr, Inc. “It’s as easy as using a smartphone.”
Weighing in at just a pound, the unit's display adjusts to allow users to measure in all positions – horizontally, vertically or upside down. In addition, the unit can be mounted on a measuring stand to provide a stationary roughness measuring instrument for small workshops. The range of measuring applications is expanded by the ability to remove the drive unit from the MarSurf M 310 and operate it separately from the display, providing the user with more flexibility. The drive also incorporates built in "Vees" to support small diameter parts during the measurement cycle.
MarSurf M 310 software features 31 parameters to choose from, offering performance range on par with a laboratory instrument. Tolerance limits can be set for all selected parameters, and exceedances are signaled in the display and in the protocol. Measurements are made according to the standards and rules for stylus instruments (DIN ISO, ASME, JIS, MOTIF), and can be quickly and easily saved in the device. Free MarWin Roughness Viewer software for Windows is also available, which allows the measurements to be brought over to a PC for archival or use in quality documentation reports.
Contact Details
Related Glossary Terms
- cutoff
cutoff
Step that prepares a slug, blank or other workpiece for machining or other processing by separating it from the original stock. Performed on lathes, chucking machines, automatic screw machines and other turning machines. Also performed on milling machines, machining centers with slitting saws and sawing machines with cold (circular) saws, hacksaws, bandsaws or abrasive cutoff saws. See saw, sawing machine; turning.
- metrology
metrology
Science of measurement; the principles on which precision machining, quality control and inspection are based. See precision machining, measurement.
- precision machining ( precision measurement)
precision machining ( precision measurement)
Machining and measuring to exacting standards. Four basic considerations are: dimensions, or geometrical characteristics such as lengths, angles and diameters of which the sizes are numerically specified; limits, or the maximum and minimum sizes permissible for a specified dimension; tolerances, or the total permissible variations in size; and allowances, or the prescribed differences in dimensions between mating parts.
- quality assurance ( quality control)
quality assurance ( quality control)
Terms denoting a formal program for monitoring product quality. The denotations are the same, but QC typically connotes a more traditional postmachining inspection system, while QA implies a more comprehensive approach, with emphasis on “total quality,” broad quality principles, statistical process control and other statistical methods.
- tolerance
tolerance
Minimum and maximum amount a workpiece dimension is allowed to vary from a set standard and still be acceptable.